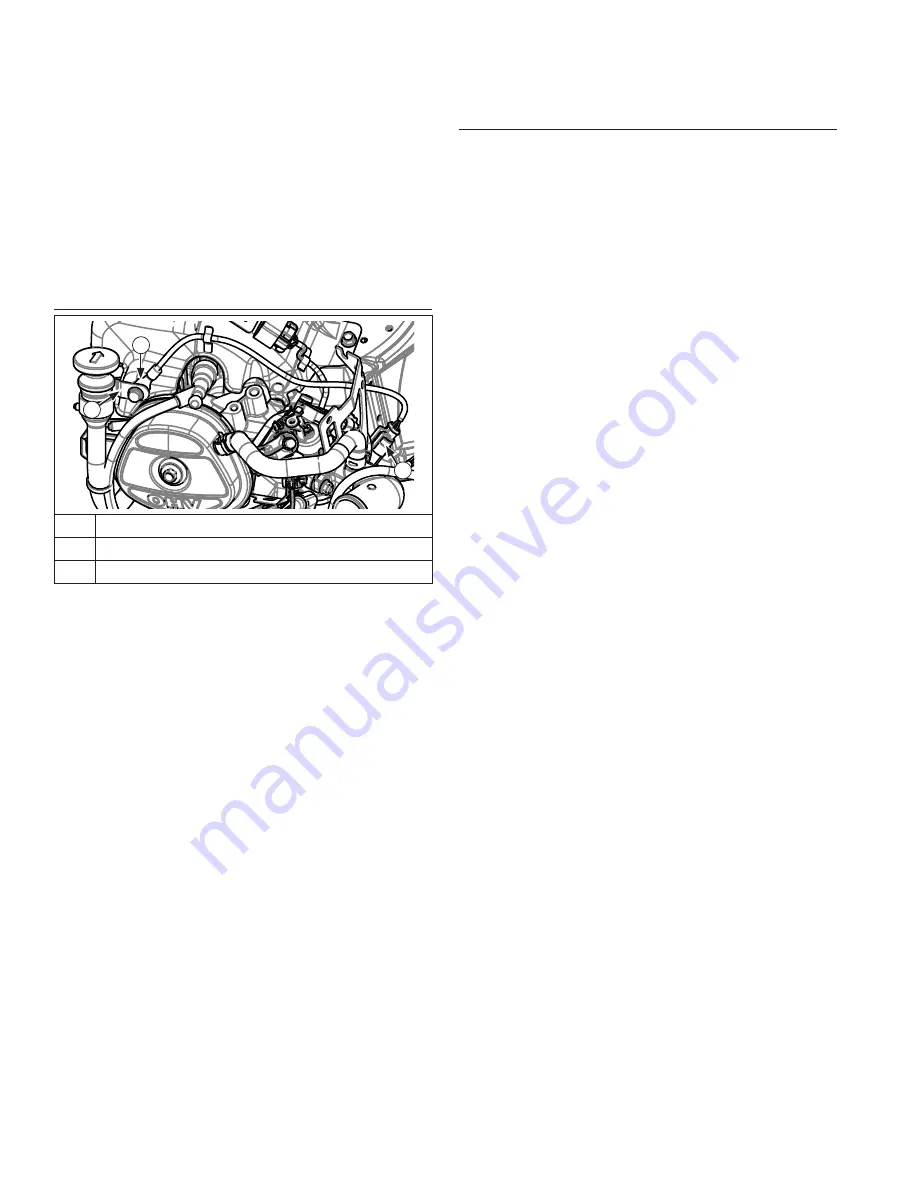
EFI SYSTEM
32
17 690 15 Rev. --
KohlerEngines.com
4. With throttle blade in full open position (WOT), press
magnet assembly fully on to throttle shaft. Full
insertion can be checked by measuring height from
throttle body sensor mounting face to end of magnet
assembly. This should be no more than 8.6 mm
(0.34 in.). Installation process requires signifi cant
force, so take care that all parts are aligned. Tapping
magnet assembly on can fracture/damage brittle
magnet within assembly and throttle body assembly
and is NOT RECOMMENDED.
5. Install sensor and secure with screws. Torque
screws to 1.3 N·m (11.5 in. lb.).
Engine Temperature Sensor
C
A
B
A
Engine Temperature Sensor
B
Unplug Sensor to Replace
C
Dipstick Tube Bracket
NOTE: Engine temperature sensor resembles a ground
wire.
A sealed, serviceable assembly. A faulty sensor requires
replacement. If a fault code indicates a problem with
temperature sensor, it can be tested as follows:
1. Shut off engine and allow it to return to room
temperature (25°C, 77°F).
2. With sensor still connected, check temperature
sensor circuit resistance between Black pin 10 and
14 terminals. Value should be 9000-11000 Ω.
3. If resistance is out of specifi cations, unplug sensor
from wiring harness and replace. Note that sensor is
installed under dipstick tube bracket.
Temperature/Manifold Absolute Pressure (TMAP)
Sensor
A sealed non-serviceable integrated sensor that checks
both intake air temperature and manifold absolute
pressure. Complete replacement is required if it is faulty.
Sensor and wiring harness can be checked as follows.
If a fault code indicates a problem with Intake Air
Temperature (TMAP) Sensor Circuit (P0112 or P0113), it
can be tested as follows:
1. Remove TMAP sensor from throttle body.
2. Allow it to reach room temperature (20°C, 68°F).
3. Unplug Black connector from ECU.
4. With sensor still connected, check temperature
sensor circuit resistance between Black pin 10 and 8
pin terminals. Value should be 1850-2450 Ω.
5. Unplug sensor from wire harness and check sensor
resistance separately across pin. Resistance value
should again be 1850-2450 Ω.
a. If resistance is out of specifi cations, check local
temperature. Sensor resistance will go down as
temperature is higher. Replace TMAP sensor if
determined to be faulty.
b. If it is within specifi cations, proceed to Step 6.
6. Check circuits (input, ground), from main harness
connector to sensor plug for continuity, damage, etc.
Connect one ohmmeter lead to Black pin 8 in main
harness connector (as in step 4). Connect other lead
to terminal #3 in sensor plug. Continuity should be
indicated. Repeat test between Black pin 10 and
terminal #4 in sensor plug.
7. Reinstall sensor.
If a fault code indicates a problem with Manifold Absolute
Pressure (TMAP) Sensor Circuit (P0107 or P0108), it
can be tested as follows:
1. Make sure all connections are making proper
contact and are free of dirt and debris. Slide locking
tab out and pull off TMAP connector. Turn key switch
to ON and check with a volt meter by contacting red
lead to pin 1 and black lead to pin 2. There should
be 5 volts present, indicating ECU and wiring
harness are functioning.
2. Check continuity in wire harness. Ohms between Pin
3 at sensor connector and Black pin 11 connector at
ECU should be near zero ohms. If no continuity is
measured or very high resistance, replace wire
harness.
3. Check to make sure throttle body is not loose and
TMAP sensor is not loose. Loose parts would allow
a vacuum leak, making TMAP sensor report
misleading information to ECU.
a. Tighten all hardware and perform an ECU Reset
and a TPS Learn Procedure to see if MIL will
display a fault with sensor again. If MIL fi nds a
fault with TMAP sensor, replace it.
Summary of Contents for Carryall 300 2021
Page 2: ......
Page 16: ......
Page 551: ...80 2018 by Kohler Co All rights reserved KohlerEngines com 17 690 15 Rev...
Page 565: ...GASOLINE ENGINE HARNESS Wiring Diagrams Gasoline Engine Harness 26...
Page 566: ...Page intentionally left blank...
Page 567: ...GASOLINE KEY START MAIN HARNESS Wiring Diagrams Gasoline Key Start Main Harness 26...
Page 568: ...Page intentionally left blank...
Page 569: ...GASOLINE PEDAL START MAIN HARNESS Wiring Diagrams Gasoline Pedal Start Main Harness 26...
Page 570: ...Page intentionally left blank...
Page 571: ...GASOLINE INSTRUMENT PANEL HARNESS Wiring Diagrams Gasoline Instrument Panel Harness 26...
Page 572: ...Page intentionally left blank...
Page 573: ...GASOLINE FNR HARNESS Wiring Diagrams Gasoline FNR Harness 26...
Page 574: ...Page intentionally left blank...
Page 575: ...ELECTRIC MAIN HARNESS Wiring Diagrams Electric Main Harness 26...
Page 576: ...Page intentionally left blank...
Page 577: ...ELECTRIC INSTRUMENT PANEL HARNESS Wiring Diagrams Electric Instrument Panel Harness 26...
Page 578: ...Page intentionally left blank...
Page 579: ...ELECTRIC ACCESSORIES HARNESS Wiring Diagrams Electric Accessories Harness 26...
Page 580: ...Page intentionally left blank...
Page 588: ...NOTES...
Page 589: ...NOTES...
Page 590: ...NOTES...
Page 591: ...NOTES...
Page 592: ...NOTES...
Page 593: ...NOTES...
Page 594: ...NOTES...
Page 595: ......
Page 596: ......