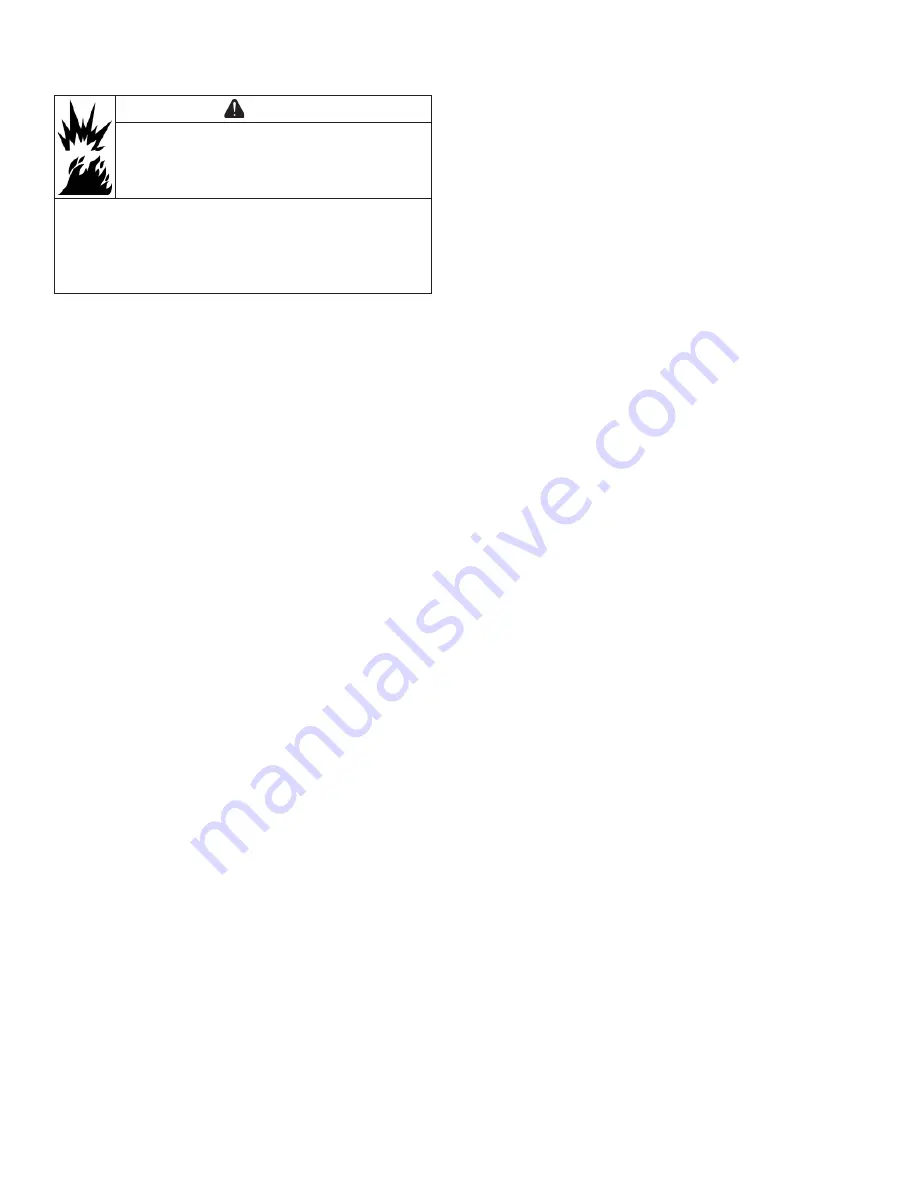
EFI SYSTEM
24
17 690 15 Rev. --
KohlerEngines.com
WARNING
Explosive Fuel can cause fi res and severe
burns.
Do not fi ll fuel tank while engine is hot or
running.
Gasoline is extremely fl ammable and its vapors can
explode if ignited. Store gasoline only in approved
containers, in well ventilated, unoccupied buildings,
away from sparks or fl ames. Spilled fuel could ignite if it
comes in contact with hot parts or sparks from ignition.
Never use gasoline as a cleaning agent.
NOTE: Engines in this application have in-tank fuel
pump, EFI fuel fi lter, and all fuel lines supplied
and installed by OEM. Refer to equipment
manufacturer's manual for information on these
components and before working on fuel system.
Typical electronic fuel injection (EFI) system and related
components include:
● In-tank fuel pump (OEM supplied and installed).
● Fuel fi lter (OEM supplied and installed).
● High pressure fuel line (OEM supplied and installed).
● Fuel injector.
● Throttle body.
● Electronic control unit (ECU).
● Ignition coil.
● Engine temperature sensor.
● Throttle position sensor (TPS).
● Crankshaft position sensor.
● Oxygen sensor.
● Temperature/Manifold Absolute Pressure (TMAP)
sensor.
● Wire harness assembly & affi liated wiring.
● 10 Amp fuse (ignition switch).
● 10 Amp fuse (battery power).
● Malfunction indicator light (MIL) - OEM supplied and
installed).
FUEL RECOMMENDATIONS
Refer to Maintenance.
FUEL LINE (OEM Supplied)
Low permeation fuel line must be installed on all Kohler
Co. engines to maintain EPA and CARB regulatory
compliance.
OPERATION
NOTE: When performing voltage or continuity tests,
avoid putting excessive pressure on or against
connector pins. Pin probes (maximum diameter
0.81 mm (0.032 in.) approximately) are
recommended for testing to avoid spreading or
bending terminals.
EFI system is designed to provide peak engine
performance with optimum fuel effi ciency and lowest
possible emissions. Ignition and injection functions
are electronically controlled, monitored and continually
corrected during operation to maintain ideal air/fuel ratio.
Central component of system is Electronic Control Unit
(ECU) which manages system operation, determining
best combination of fuel mixture and ignition timing for
current operating conditions.
An in-tank fuel pump is used to move fuel from tank
through a fuel fi lter and fuel line. Fuel pump regulates
fuel pressure to a system operating pressure of 50 psi.
Fuel is delivered through high pressure fuel line into
injector, which injects fuel into intake port. ECU controls
amount of fuel by varying length of time that injector
is on. This can range from 2 to over 12 milliseconds
depending on fuel requirements. Controlled injection of
fuel occurs every other crankshaft revolution, or once for
each 4-stroke cycle. When intake valve opens, air/fuel
mixture is drawn into combustion chamber, where it is
compressed, ignited, and burned.
ECU controls amount of fuel being injected and ignition
timing by monitoring primary sensor signals for engine
temperature, speed (RPM), and throttle position (load).
These primary signals are compared to preprogrammed
maps in ECU computer chip, and ECU adjusts fuel
delivery to match mapped values. After engine reaches
operating temperature, an exhaust gas oxygen sensor
provides feedback to ECU based upon amount of
unused oxygen in exhaust, indicating whether fuel
mixture being delivered is rich or lean. Based upon this
feedback, ECU further adjusts fuel input to re-establish
ideal air/fuel ratio. This operating mode is referred to as
closed loop operation. EFI system operates closed loop
when all three of following conditions are met:
● Engine temperature is greater than 40°C (104°F).
● Oxygen sensor has warmed suffi ciently to provide a
signal (minimum 400°C, 752°F).
● Engine operation is at a steady state (not starting,
warming up, accelerating, etc.).
During closed loop operation ECU has ability to readjust
temporary and learned adaptive controls, providing
compensation for changes in overall engine condition
and operating environment, so it will be able to maintain
ideal air/fuel ratio. This system requires a minimum
engine temperature of 40°C (104°F) to properly adapt.
These adaptive values are maintained as long as ECU is
not reset.
During certain operating periods such as cold starts,
warm up, acceleration, high load, etc., a richer air/fuel
ratio is required and system operates in an open loop
mode. In open loop operation oxygen sensor output is
used to ensure engine is running rich, and controlling
adjustments are based on primary sensor signals and
programmed maps only. This system operates open
loop whenever three conditions for closed loop operation
(above) are not being met.
ECU is brain or central processing computer of entire
EFI system. During operation, sensors continuously
gather data which is relayed through wiring harness
to input circuits within ECU. Signals to ECU include:
ignition (on/off ), crankshaft position and speed (RPM),
throttle position, engine temperature, intake air
temperature, exhaust oxygen levels, manifold absolute
pressure, and battery voltage.
ECU compares input signals to programmed maps in
its memory to determine appropriate fuel and spark
requirements for immediate operating conditions. ECU
then sends output signals to set injector duration and
ignition timing.
Summary of Contents for Carryall 300 2021
Page 2: ......
Page 16: ......
Page 551: ...80 2018 by Kohler Co All rights reserved KohlerEngines com 17 690 15 Rev...
Page 565: ...GASOLINE ENGINE HARNESS Wiring Diagrams Gasoline Engine Harness 26...
Page 566: ...Page intentionally left blank...
Page 567: ...GASOLINE KEY START MAIN HARNESS Wiring Diagrams Gasoline Key Start Main Harness 26...
Page 568: ...Page intentionally left blank...
Page 569: ...GASOLINE PEDAL START MAIN HARNESS Wiring Diagrams Gasoline Pedal Start Main Harness 26...
Page 570: ...Page intentionally left blank...
Page 571: ...GASOLINE INSTRUMENT PANEL HARNESS Wiring Diagrams Gasoline Instrument Panel Harness 26...
Page 572: ...Page intentionally left blank...
Page 573: ...GASOLINE FNR HARNESS Wiring Diagrams Gasoline FNR Harness 26...
Page 574: ...Page intentionally left blank...
Page 575: ...ELECTRIC MAIN HARNESS Wiring Diagrams Electric Main Harness 26...
Page 576: ...Page intentionally left blank...
Page 577: ...ELECTRIC INSTRUMENT PANEL HARNESS Wiring Diagrams Electric Instrument Panel Harness 26...
Page 578: ...Page intentionally left blank...
Page 579: ...ELECTRIC ACCESSORIES HARNESS Wiring Diagrams Electric Accessories Harness 26...
Page 580: ...Page intentionally left blank...
Page 588: ...NOTES...
Page 589: ...NOTES...
Page 590: ...NOTES...
Page 591: ...NOTES...
Page 592: ...NOTES...
Page 593: ...NOTES...
Page 594: ...NOTES...
Page 595: ......
Page 596: ......