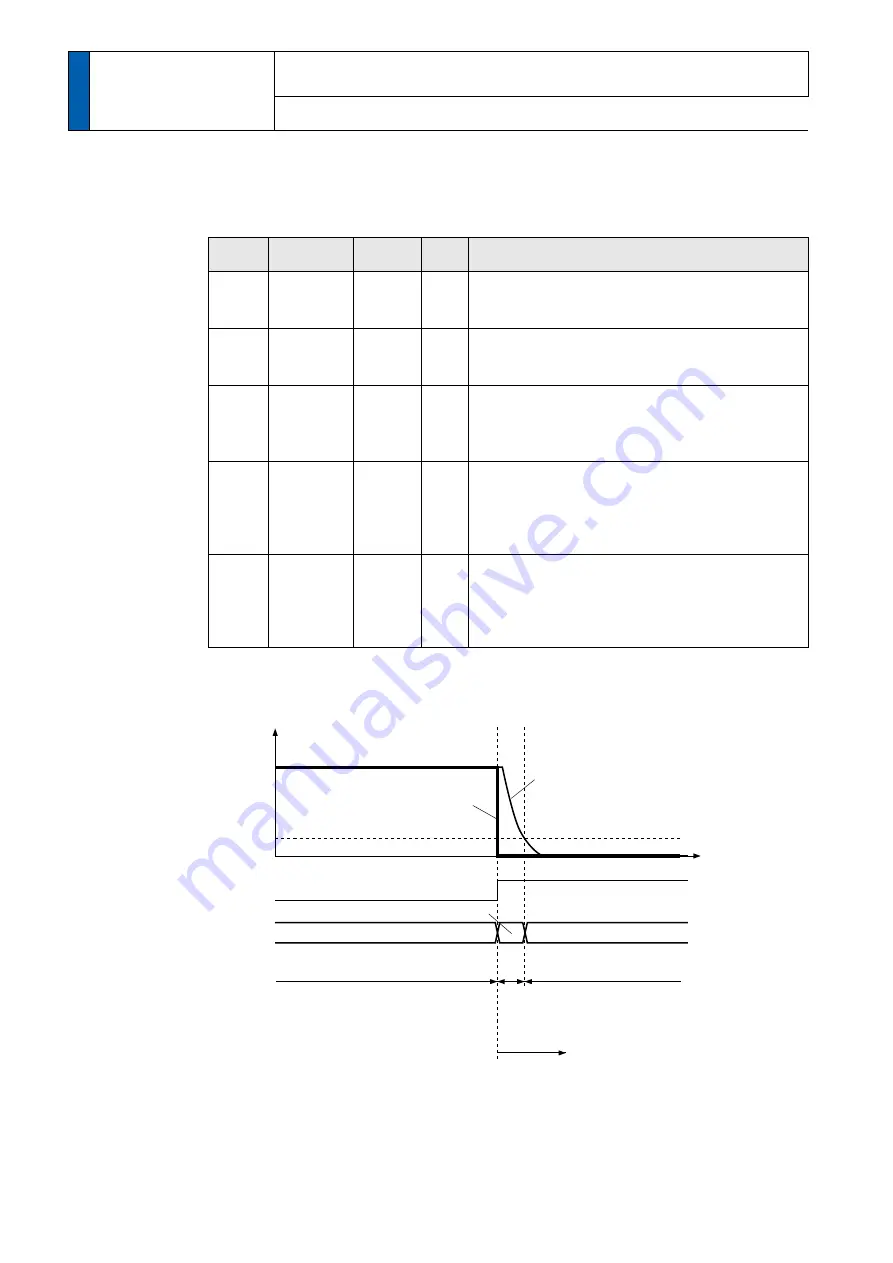
6-32
Rev.2.00
When an alarm requiring emergency stop occurs, the system controls and immediately stops
the motor.
1
)
Relevant parameters
P
anameter
No.
Title
Range
Unit
Function
Pr5.10
Sequence at
alarm
0 to 7
—
Specify the status during deceleration and after stop, af-
ter occurrence of alarm.Setting the parameter to one of 4
to 7, enables emergency stop.
Pr5.11
Torque setup
for emergency
stop
0 to 500
%
Set up the torque limit at emergency stop.
When setup value is 0, the torque limit for normal opera-
tion is applied.
Pr5.13
Over-speed
level setup
0 to 20000
r/min
If the motor speed exceeds this setup value, Err26.0
Over-speed protection occurs.The over-speed level be-
comes internal value of the over-speed protection level.
speed by setting up this to 0.
Pr6.14
Emergency
stop time at
alarm
0 to 1000
ms
Set up the time allowed to complete emergency stop in
an alarm condition. Exceeding this time puts the system
in alarm state.
When setup value is 0, immediate stop is disabled and
the immediate alarm stop is enabled.
Pr6.15
2nd
over-speed
level setup
0 to 20000
r/min
When the motor speed exceeds this setup time during
emergency stop sequence in an alarm condition, Err 26.1
2nd over-speed protection will be activated. The over-
speed level becomes internal value of the over-speed
protection level. speed by setting up this to 0.
2
)
Emergency stop sequence upon occurrence of an alarm requiring emergency stop
Speed
[r/min]
Stop
reference
speed
(30r/min)
Alarm state (operation after stop: DB/free run)
Emergency stop
Operation
Emergency stop time
Normal operation according to
the command from the host device
Motor velocity
Velocity instruction
Time
Alarm
No alarm
Alarm requiring emergency stop occurs.
Torque limit
For normal operation
Pr5.11
*
Pr 5.11 “Torque setup for emergency
stop”—shock relief upon emergency
After occurrence of an alarm requiring emergency stop: when the speed has not dropped
down to 30 r/min after the elapse of time set by Pr 6.14 “Emergency stop time at alarm”, the
system generates the alarm. The system also enters the alarm state if an alarm that does not
require emergency stop occurs in the driver during the sequence of the emergency stop.
For normal operation
6
1. Troubleshooting
When in Trouble
Emergency Stop upon Occurrence of Alarm
Содержание MINAS A6N Series
Страница 14: ...14 Rev 2 00 MEMO ...
Страница 30: ...1 16 Rev 2 00 MEMO ...
Страница 104: ...2 74 Rev 2 00 MEMO ...
Страница 228: ...3 124 Rev 2 00 MEMO ...
Страница 491: ...7 108 Rev 2 00 MEMO ...