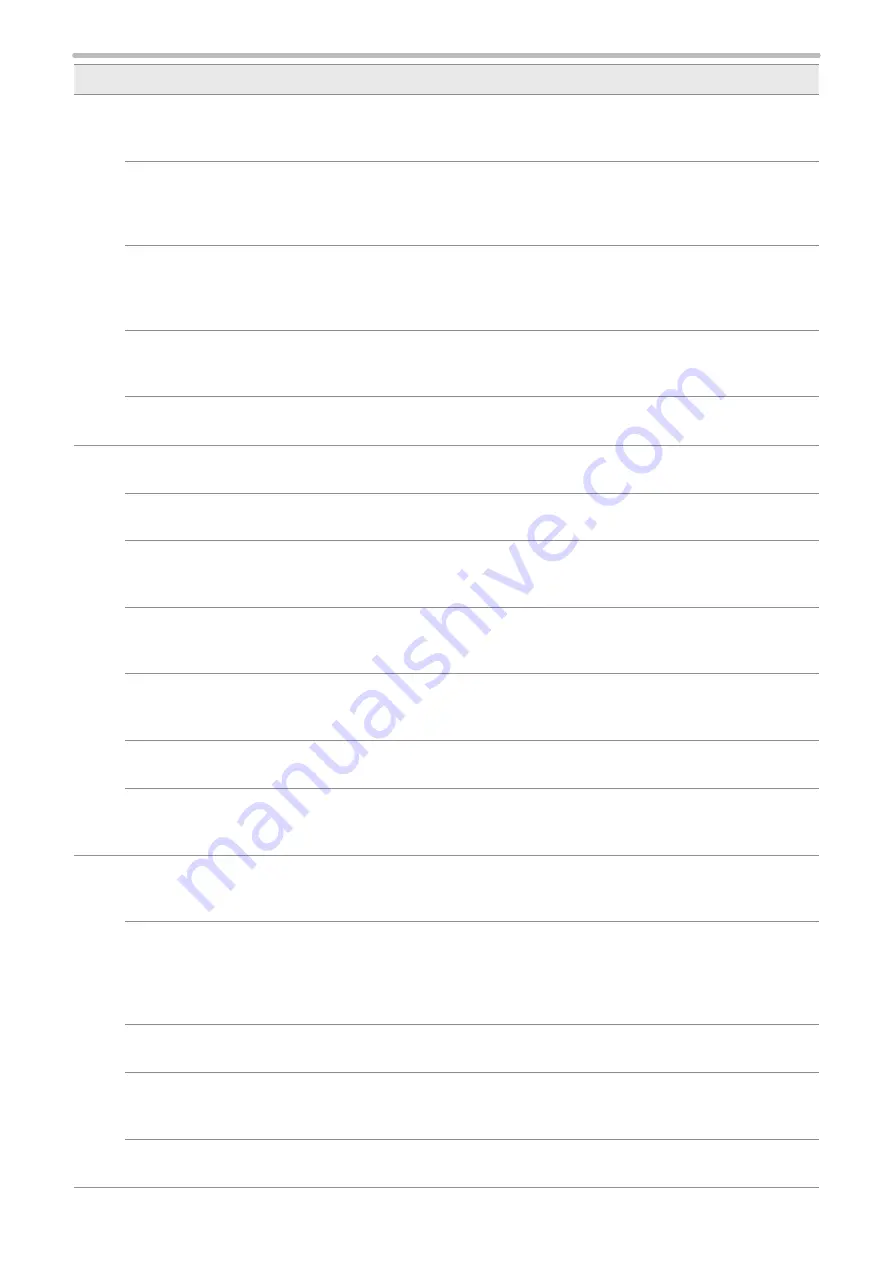
52
Type
Name
Code
Functions
Refer
C
ha
ra
ct
er S
et
tin
g
Character entry (by ASCII code)
MCS
Sets the characters of the character objects (reference
list type) by the ASCII code. Alpha-numeric characters
and symbols are available.
Character entry (by ASCII and
Shift-JIS code)
STR
Sets the characters of the character objects (reference
list type). Characters including alpha-numeric,
functional characters and Japanese characters are
available.
Character entry per trigger
SIN
When “Characters specified by SIN command” is set
for character objects or barcode/2D code objects,
input characters with this command. Send this
command per each marking.
Character object settings
STC
Sets the position and size of the character object
(reference list type) and conditions including text
characteristics.
Character object settings
(shortened)
SPC
Sets only X-/Y-position and laser power correction in
the character object settings.
Fu
nc
tio
na
l c
ha
ra
ct
er
s
Counter settings
CNT
Configures the “counter” function used to mark
consecutive numbers.
Counter reset
CTR
Resets the current value to the starting value.
Expiry date/time settings
LMT
Configures the “expiry” function used to mark the date
with a specified period added or subtracted to/from
the current date.
Lot settings
LTC
Configures the “Lot” function used to change
characters depending on the date/time and counter
values.
Lot character
LTS
Sets the characters used with the “Lot” function to
change characters depending on the date/time and
counter values.
Registered character settings
RKC
Sets the input format of the “Registered characters”
function used to switch characters by I/O input.
Registered character strings
RKS
Sets the character string used with the “Registered
characters” function that switches characters by I/O
input.
B
ar
C
ode
/2
D
C
ode
Bar code/2D code characters (by
ASCII code)
BCS
Sets the characters to encode of the bar code/2D
code objects by the ASCII code. Alpha-numeric
characters and symbols are available.
Bar code/2D code characters (by
ASCII and Shift-JIS code)
BRS
Sets the characters to encode of the bar code/2D
code objects. Characters including control codes
(specified with 2-byte alternative codes), alpha-
numeric, functional characters, and Japanese
characters are available.
Bar code/2D code object settings
BRF
Sets the conditions such as the position and size of
the bar code/2D code as well as code characteristics.
Human readable text settings
BRV
Sets the character conditions to mark the character
strings of bar code/2D code as the human readable
text.
Module filling of 2D codes
BRP
Sets the laser settings and filling details with a font by
each element of the 2D code.
ME-LP-GS-SR-COMP-3
Summary of Contents for LP-GS Series
Page 11: ...1 Preparation of Command Control ME LP GS SR COMP 3...
Page 26: ...2 Communication Control Basics ME LP GS SR COMP 3...
Page 50: ...3 Data Format for Each Command ME LP GS SR COMP 3...
Page 136: ...136 MEMO ME LP GS SR COMP 3...
Page 137: ...Troubleshooting ME LP GS SR COMP 3...
Page 163: ...Character Code Table ME LP GS SR COMP 3...
Page 176: ...Index ME LP GS SR COMP 3...
Page 178: ...178 W Warning 154 ME LP GS SR COMP 3...
Page 179: ......
Page 180: ...Panasonic Industrial Devices SUNX Co Ltd 2014 2019 April 2019...