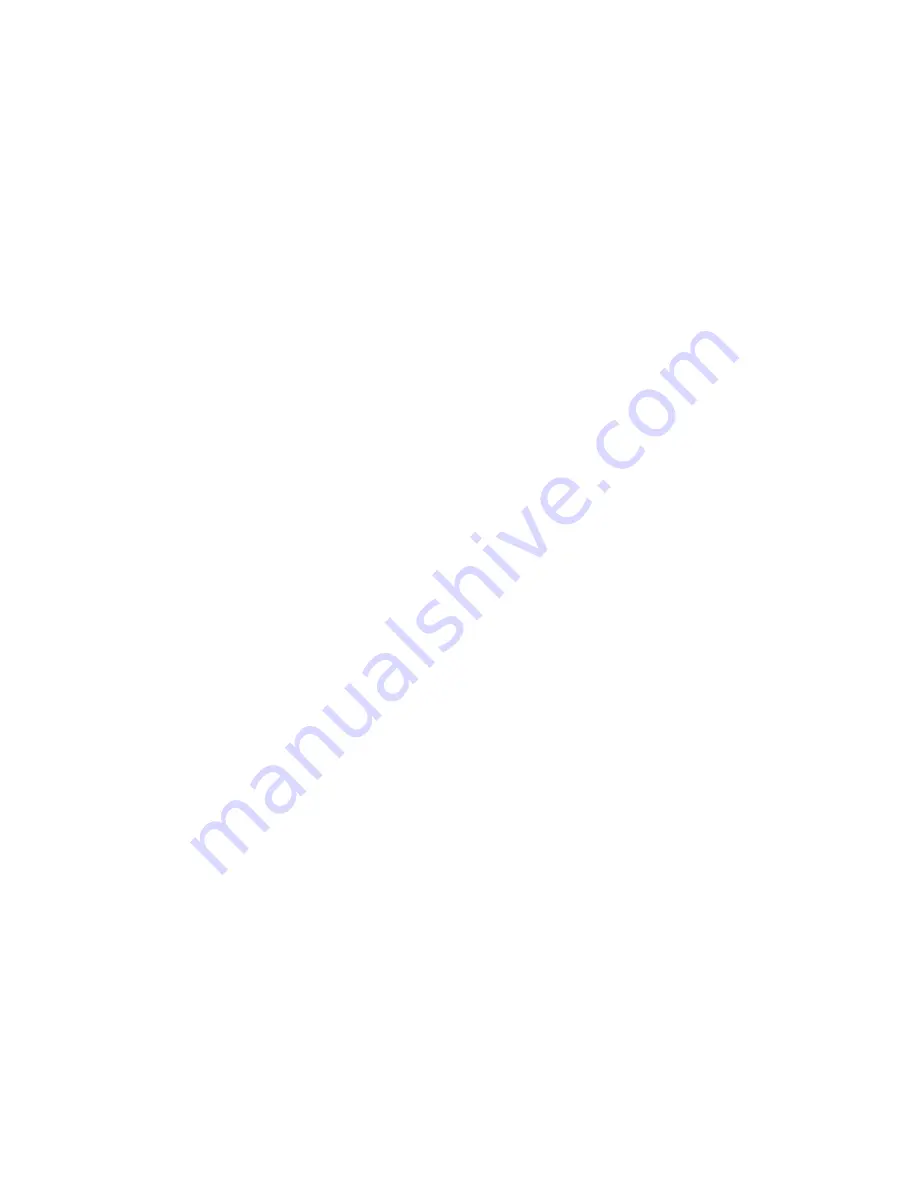
installing ...................................................... 415
removing...................................................... 411
drivelines
driveline guards
installing ...................................................... 303
removing...................................................... 301
installing driveline ............................................. 298
removing driveline from combine to float
module .......................................................... 296
drives
header drive..................................................... 296
E
EasyMove
™
Slow Speed Transport System
changing tow-bar hitch connection from clevis to
pintle ............................................................ 475
EasyMove
™
transport wheels
adjusting ......................................................... 122
electrical system
maintaining electrical system .............................. 295
replacing light bulbs .......................................... 295
sensors
AHHC sensors................................................ 203
reel height sensor
replacing................................................... 164
equipment servicing
—
end of season ...................... 270
equipment servicing
—
preseason ........................... 270
extended center filler ............................................ 489
F
FD2 Series
definition........................................................... 21
feed auger configurations ........................................ 89
medium configuration.......................................... 98
narrow configuration ........................................... 95
ultra narrow configuration .................................... 91
ultra wide configuration ..................................... 103
wide configuration ............................................ 100
feed auger flighting............................................... 489
feed deck
checking link holder hooks.................................. 392
feed deck pan
lowering feed deck pan ...................................... 390
raising feed deck pan ......................................... 391
feed deflectors....................................................... 61
float module
installing on New Holland CR combines ............. 396
feed drapers
adjusting draper tension..................................... 373
adjusting speed ................................................ 158
checking draper tension ..................................... 373
drive roller bearing
installing ...................................................... 380
drive rollers...................................................... 374
installing ...................................................... 377
removing...................................................... 374
idler roller........................................................ 381
installing idler roller........................................... 383
removing drive roller bearing .............................. 378
removing idler roller .......................................... 381
replacing feed draper......................................... 370
replacing idler roller bearing ............................... 386
FFFT
definition........................................................... 21
finger tight
definition........................................................... 21
fingers
auger fingers .................................................... 322
adjusting finger timing .................................... 327
checking finger timing .................................... 327
installing ................................................114, 325
removing................................................112, 322
plastic reel fingers
installing ...................................................... 429
removing...................................................... 428
steel reel fingers
installing ...................................................... 427
removing...................................................... 427
flex float system
flex frown limiter
disable ......................................................... 146
enable ......................................................... 147
flex modes
operating in flex mode ....................................... 143
flighting ........................................................105, 322
installing....................................................107, 110
removing ......................................................... 105
float ................................................................... 128
header float
changing float spring configuration ................... 134
checking and adjusting.................................... 129
header float locks.............................................. 140
wing float locks
lock/unlock ................................................... 140
locked.......................................................... 145
unlocked ...................................................... 143
float modules ...................................................... 488
attaching float module to header ........................... 66
auger drive
adjusting auger drive chain tension ................... 320
augers............................................................. 308
auger fingers................................................. 322
checking finger timing ................................. 327
installing .............................................114, 325
removing ............................................112, 322
auger to pan clearance ................................... 308
fingers