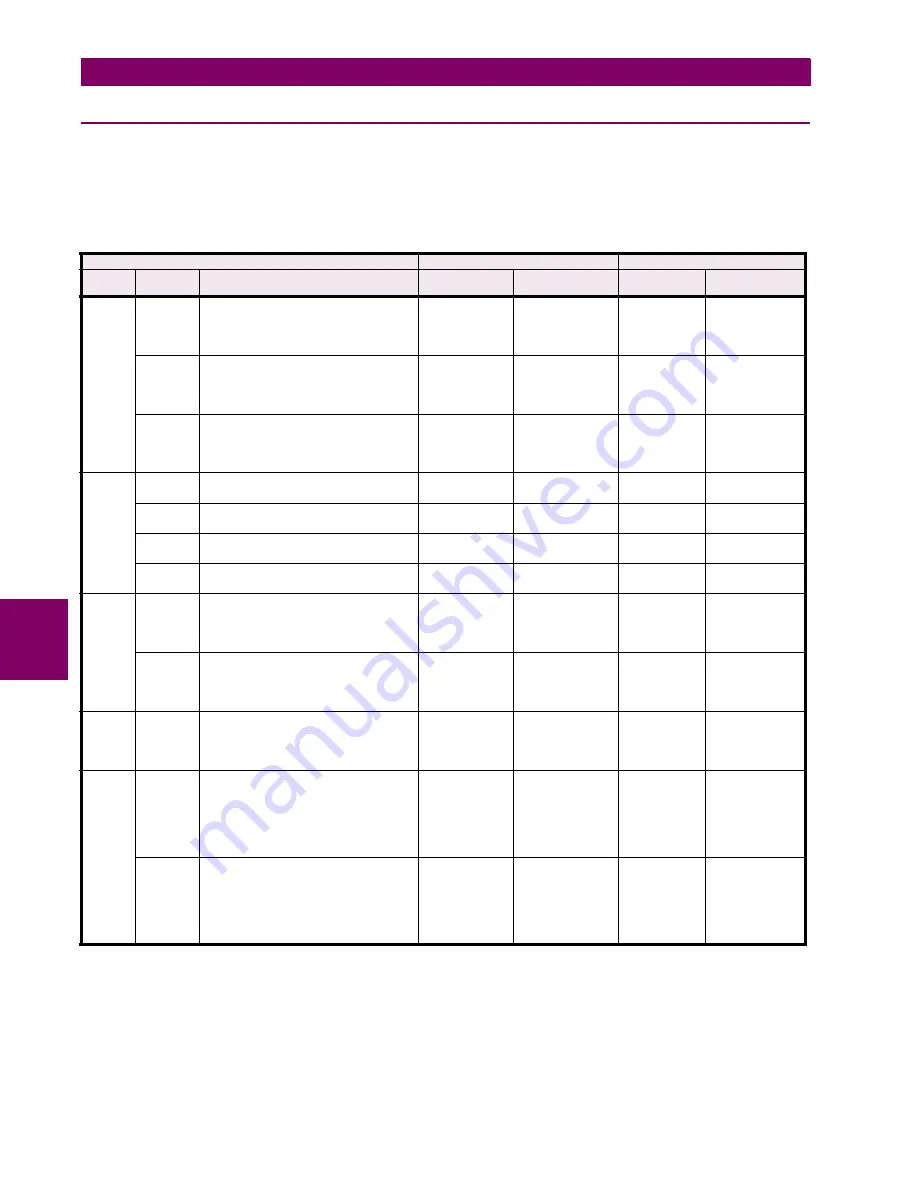
F-4
F60 Feeder Protection System
GE Multilin
F.1 DEVICE PROFILE DOCUMENT
APPENDIX F
F
F.1.2 IMPLEMENTATION TABLE
The following table identifies the variations, function codes, and qualifiers supported by the F60 in both request messages
and in response messages. For static (non-change-event) objects, requests sent with qualifiers 00, 01, 06, 07, or 08, will be
responded with qualifiers 00 or 01. Static object requests sent with qualifiers 17 or 28 will be responded with qualifiers 17 or
28. For change-event objects, qualifiers 17 or 28 are always responded.
Table F–2: IMPLEMENTATION TABLE (Sheet 1 of 4)
OBJECT
REQUEST
RESPONSE
OBJECT
NO.
VARIATION
NO.
DESCRIPTION
FUNCTION
CODES (DEC)
QUALIFIER
CODES (HEX)
FUNCTION
CODES (DEC)
QUALIFIER
CODES (HEX)
1
0
Binary Input (Variation 0 is used to request
default variation)
1
(read)
22
(assign class)
00, 01
(start-stop)
06
(no range, or all)
07, 08
(limited quantity)
17, 28
(index)
1
Binary Input
1
(read)
22
(assign class)
00, 01
(start-stop)
06
(no range, or all)
07, 08
(limited quantity)
17, 28
(index)
129
(response)
00, 01
(start-stop)
17, 28
(index)
(
see Note 2)
2
Binary Input with Status
1
(read)
22
(assign class)
00, 01
(start-stop)
06
(no range, or all)
07, 08
(limited quantity)
17, 28
(index)
129
(response)
00, 01
(start-stop)
17, 28
(index)
(see Note 2)
2
0
Binary Input Change (Variation 0 is used to
request default variation)
1
(read)
06
(no range, or all)
07, 08
(limited quantity)
1
Binary Input Change without Time
1
(read)
06
(no range, or all)
07, 08
(limited quantity)
129
(response)
130
(unsol. resp.)
17, 28
(index)
2
Binary Input Change with Time
1
(read)
06
(no range, or all)
07, 08
(limited quantity)
129
(response
130
(unsol. resp.)
17, 28
(index)
3
Binary Input Change with Relative Time
1
(read)
06
(no range, or all)
07, 08
(limited quantity)
10
0
Binary Output Status (Variation 0 is used to
request default variation)
1
(read)
00, 01
(start-stop)
06
(no range, or all)
07, 08
(limited quantity)
17, 28
(index)
2
Binary Output Status
1
(read)
00, 01
(start-stop)
06
(no range, or all)
07, 08
(limited quantity)
17, 28
(index)
129
(response)
00, 01
(start-stop)
17, 28
(index)
(see Note 2)
12
1
Control Relay Output Block
3
(select)
4
(operate)
5
(direct op)
6 (
dir. op, noack)
00, 01
(start-stop)
07, 08
(limited quantity)
17, 28
(index)
129
(response)
echo of request
20
0
Binary Counter
(Variation 0 is used to request default
variation)
1
(read)
7
(freeze)
8
(freeze noack)
9
(freeze clear)
10
(frz. cl. noack)
22
(assign class)
00, 01
(start-stop)
06
(no range, or all)
07, 08
(limited quantity)
17, 28
(index)
1
32-Bit Binary Counter
1
(read)
7
(freeze)
8
(freeze noack)
9
(freeze clear)
10
(frz. cl. noack)
22
(assign class)
00, 01
(start-stop)
06
(no range, or all)
07, 08
(limited quantity)
17, 28
(index)
129
(response)
00, 01
(start-stop)
17, 28
(index)
(see Note 2)
Note 1:
A default variation refers to the variation responded when variation 0 is requested and/or in class 0, 1, 2, or 3 scans. The default varia-
tions for object types 1, 2, 20, 21, 22, 23, 30, and 32 are selected via relay settings. See the
Communications
section in Chapter 5 for
details. This optimizes the class 0 poll data size.
Note 2:
For static (non-change-event) objects, qualifiers 17 or 28 are only responded when a request is sent with qualifiers 17 or 28, respec-
tively. Otherwise, static object requests sent with qualifiers 00, 01, 06, 07, or 08, will be responded with qualifiers 00 or 01 (for change-
event objects, qualifiers 17 or 28 are always responded.)
Note 3:
Cold restarts are implemented the same as warm restarts – the F60 is not restarted, but the DNP process is restarted.
Summary of Contents for F60
Page 10: ...x F60 Feeder Protection System GE Multilin TABLE OF CONTENTS ...
Page 30: ...1 20 F60 Feeder Protection System GE Multilin 1 5 USING THE RELAY 1 GETTING STARTED 1 ...
Page 138: ...4 28 F60 Feeder Protection System GE Multilin 4 2 FACEPLATE INTERFACE 4 HUMAN INTERFACES 4 ...
Page 454: ...5 316 F60 Feeder Protection System GE Multilin 5 10 TESTING 5 SETTINGS 5 ...
Page 500: ...7 14 F60 Feeder Protection System GE Multilin 7 1 COMMANDS 7 COMMANDS AND TARGETS 7 ...
Page 508: ...8 8 F60 Feeder Protection System GE Multilin 8 2 FAULT LOCATOR 8 THEORY OF OPERATION 8 ...
Page 522: ...10 12 F60 Feeder Protection System GE Multilin 10 6 DISPOSAL 10 MAINTENANCE 10 ...
Page 660: ...B 116 F60 Feeder Protection System GE Multilin B 4 MEMORY MAPPING APPENDIX B B ...
Page 706: ...E 10 F60 Feeder Protection System GE Multilin E 1 IEC 60870 5 104 APPENDIX E E ...
Page 718: ...F 12 F60 Feeder Protection System GE Multilin F 2 DNP POINT LISTS APPENDIX F F ...
Page 728: ...H 8 F60 Feeder Protection System GE Multilin H 2 ABBREVIATIONS APPENDIX H H Z Impedance Zone ...
Page 730: ...H 10 F60 Feeder Protection System GE Multilin H 3 WARRANTY APPENDIX H H ...