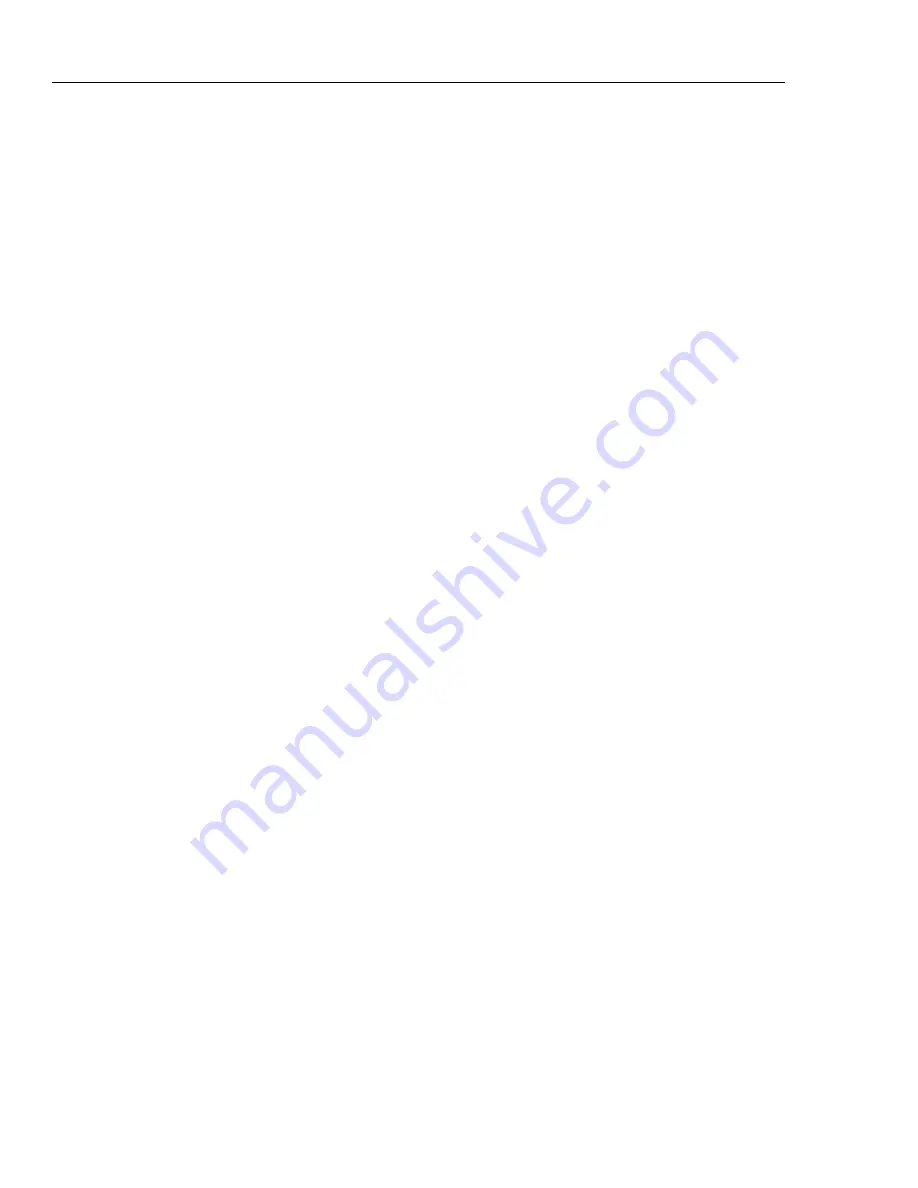
5502A
Operators Manual
5-46
The error queue has a maximum of 16 entries. If many errors occur, only the first
15 errors are kept in the queue. A 16th entry in the queue is an "error queue overflow"
error, and all later errors are discarded until the queue is at minimum partially read. The
first errors are kept, because if many errors occur before the user can acknowledge and
read them, the earliest errors are the most likely to point to the problem. The later errors
are typically repetitions or consequences of the initial problem.
Remote Program Examples
The subsequent programming examples show procedures to handle errors, to read
measurements, get a number of successive indications, lock the range, and calibrate the
Calibrator. These excerpts from programs are written in DOS BASIC.
Guidelines to Program the Calibrator
Commands are done one at a time as they are received. For some commands, a previous
condition must be set before the command will be accepted by the Calibrator. For
example, the waveform must be SQUARE before the DUTY command will be accepted.
Use the subsequent programming guidelines to make sure that the output is programmed
to the necessary condition.
•
All external connections commands must be programmed first. The calibrator will be
put in standby and the output can be changed to accommodate the new external
connection. The setting can be set if the given output does not use the setting (for
example, setting the current post while sourcing voltage).
•
The output and output mode must be programmed subsequently with the OUT
command.
•
All other output parameters such as impedance compensation, offset, and waveforms
must be programmed subsequently. The DUTY command must follow the WAVE
command.
•
The error status should be checked with the ERR? command. The calibrator will not
do the OPER command if an unacknowledged error exists.
•
Finally, the Calibrator must be put in operate with the OPER command.
First, it is necessary for a controller program to initialize the interface and the Calibrator.
Refer to subsequent sample program:
10 INIT PORT 0 \ REMOTE @6 ! PUT THE 5502A INTO THE REMOTE STATE
20 PRINT @6, “*RST;OUT 10V;OPER” ! RESET THE 5502A, PROGRAM IT TO
If necessary, use SRQs, first use the
*SRE
,
*ESE
, and
ISCE
commands to enable the
necessary event. Refer to “Checking 5502A Status.”
You retrieve instrument parameters with a query (a programming command that ends
with a question mark):
200 PRINT @6, “FUNC?”
! RETRIEVE OUTPUT FUNCTION
210 INPUT LINE @6, A$
220 PRINT “Function is: “;A$
230 PRINT @6, “ONTIME?” ! RETRIEVE ON TIME
240 INPUT LINE @6, A$
250 PRINT “The instrument has been on for “;A$;” minutes”
This program gives the subsequent sample output:
Function is: DCV
The instrument has been on for 134 minutes
Summary of Contents for 5502A
Page 4: ......
Page 12: ...5502A Operators Manual xii ...
Page 46: ...5502A Operators Manual 2 2 ...
Page 52: ...5502A Operators Manual 2 8 ...
Page 54: ...5502A Operators Manual 3 2 ...
Page 142: ...5502A Operators Manual 4 68 ...
Page 194: ...5502A Operators Manual 6 2 ...
Page 240: ...5502A Operators Manual 7 2 ...
Page 260: ...5502A Operators Manual 7 22 ...
Page 262: ...5502A Operators Manual 8 2 ...
Page 365: ...B 1 Appendix B ASCII and IEEE 488 Bus Codes ...
Page 366: ...5502A Operators Manual B 2 ...
Page 368: ...5502A Operators Manual B 4 ...
Page 378: ...5502A Operators Manual D 6 ...