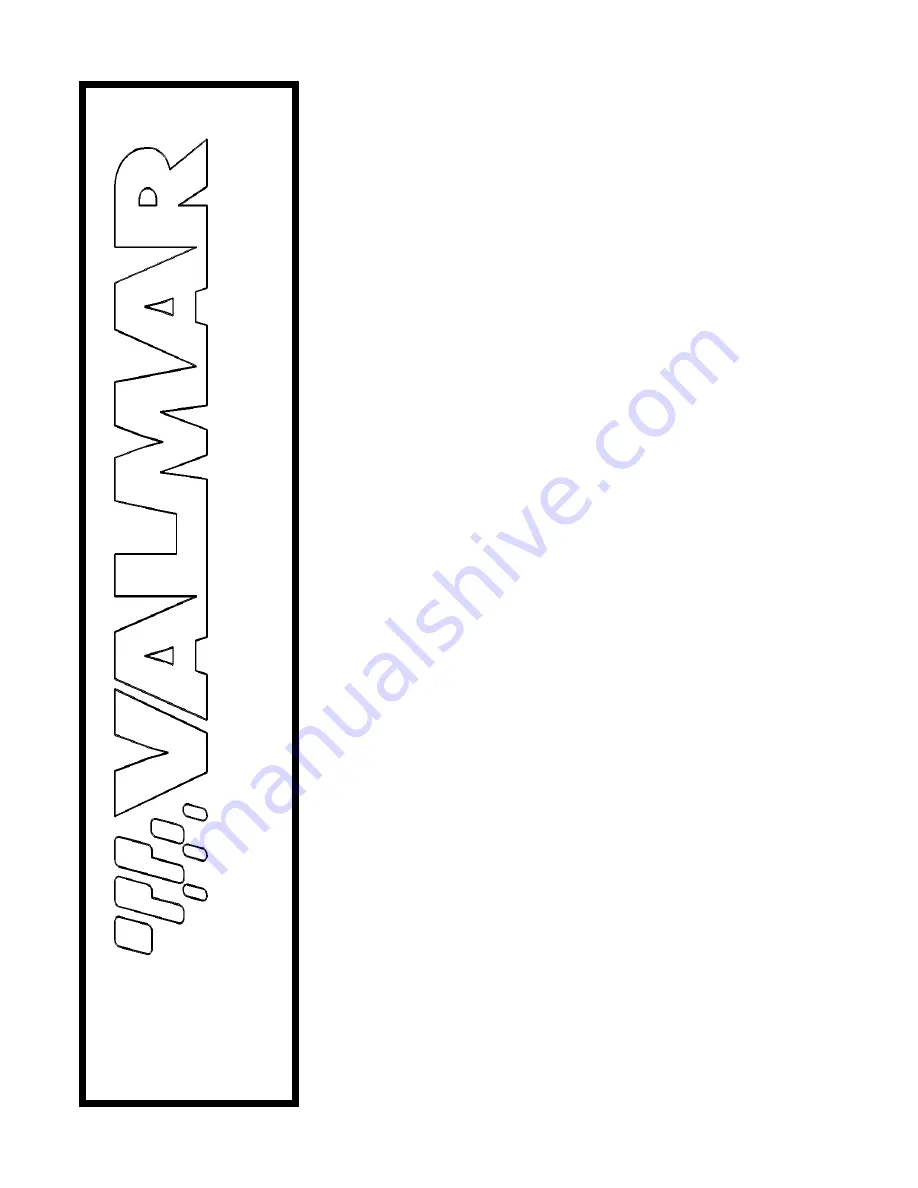
2055 / 2455 / 3255 Pneumatic
Granular Applicator
OPERATOR'S
MANUAL
Valmar Airflo Inc.
Box 100
Elie, MB R0H 0H0
Phone (204) 353
Issue Date: June 1999
FAX (204) 353-2864
Email: [email protected]
Summary of Contents for 2055
Page 4: ......
Page 5: ...Page 3...
Page 7: ...Page 3...
Page 13: ...Valmar Safety Decals Page 7...
Page 15: ...Valmar Safety Decals Page 9 Decal 1 Decal 2 Decal 3 Decal 4 4 5 6...
Page 16: ...Safety Decals Valmar Page 10 Decal 5 Decal 6...
Page 23: ...VALMAR Operation Page 17 Figure 4 13 Funnel Installation...
Page 24: ...Operation VALMAR Page 18...
Page 28: ...Calibration Valmar Page 22...
Page 29: ...Valmar Calibration Page 23...
Page 30: ...Calibration Valmar Page 24...
Page 31: ...Valmar Calibration Page 25...
Page 33: ...Valmar Calibration Page 27...
Page 34: ...Calibration Valmar Page 28...
Page 43: ...Valmar Adjustments Service Page 37...
Page 49: ...Assembly Options VALMAR Page 42...
Page 54: ...VALMAR Specifications Page 47 Figure 8 4 Electric Clutch Wiring...
Page 55: ...Specifications VALMAR Page 48...
Page 56: ...VALMAR Specifications Page 49...
Page 57: ...Page 48 10 Parts...
Page 59: ...Parts VALMAR Page 50...
Page 61: ...Parts VALMAR Page 52...
Page 63: ...Parts VALMAR Page 54...
Page 65: ...Parts VALMAR Page 56...
Page 67: ...Parts VALMAR Page 58...
Page 69: ...Parts VALMAR Page 60...
Page 71: ...Parts VALMAR Page 62...
Page 73: ...Parts VALMAR Page 64...
Page 75: ...Parts VALMAR Page 66...
Page 77: ...Parts VALMAR Page 68...