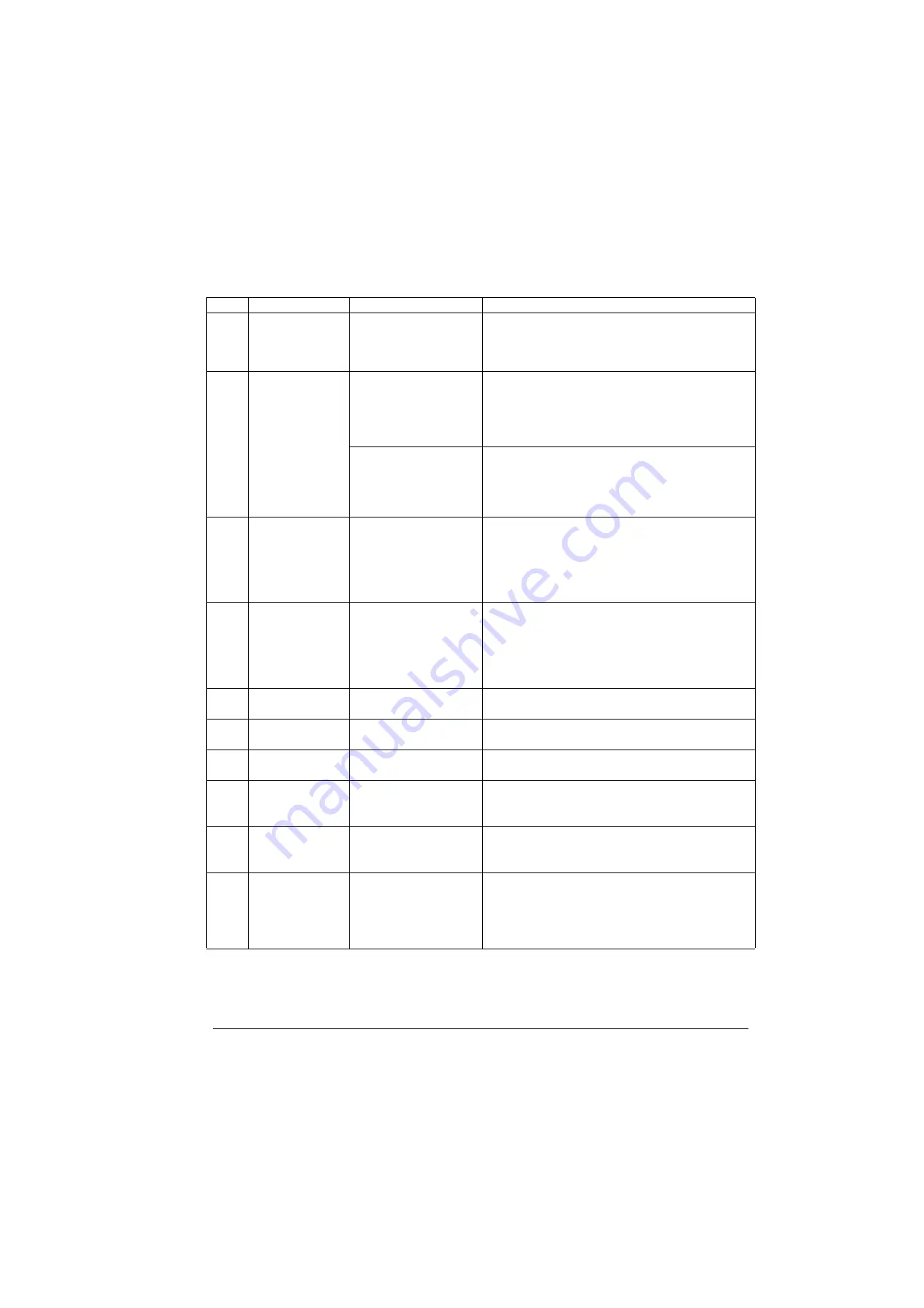
Fault tracing
275
2009
DEVICE
OVERTEMP
(4210)
bit 8
Drive IGBT temperature is
excessive. Alarm limit is
120°C.
Check ambient conditions. See also section
page
.
Check air flow and fan operation.
Check motor power against unit power.
2010
MOTOR TEMP
(4310)
bit 9
(programmable fault
function
/
)
Motor temperature is too
high (or appears to be too
high) due to excessive
load, insufficient motor
power, inadequate cooling
or incorrect start-up data.
Check motor ratings, load and cooling.
Check start-up data.
Check fault function parameters.
Measured motor
temperature has exceeded
alarm limit set by
parameter
ALARM
LIMIT.
Check value of alarm limit.
Check that actual number of sensors corresponds to value
set by parameter (
SENSOR TYPE).
Let motor cool down. Ensure proper motor cooling: Check
cooling fan, clean cooling surfaces, etc.
2011
UNDERLOAD
(FF6A)
bit 10
(programmable fault
function
)
Motor load is too low due to
e.g. release mechanism in
driven equipment.
Check for problem in driven equipment.
Check fault function parameters.
Check motor power against unit power.
2012
MOTOR STALL
(7121)
bit 11
(programmable fault
function
)
Motor is operating in stall
region due to e.g.
excessive load or
insufficient motor power.
Check motor load and drive ratings.
Check fault function parameters.
2013
AUTORESET
bit 12
Automatic reset alarm
Check parameter group
settings.
2018
PID SLEEP
bit 1
Sleep function has entered
sleeping mode.
See parameter groups
.
2019
ID RUN
bit 2
Motor Identification Run is
on.
This alarm belongs to normal start-up procedure. Wait until
drive indicates that motor identification is completed.
2021
START ENABLE 1
MISSING
bit 4
No Start Enable 1 signal
received
Check parameter
START ENABLE 1settings.
Check digital input connections.
Check fieldbus communication settings.
2022
START ENABLE 2
MISSING
bit 5
No Start Enable 2 signal
received
Check parameter
START ENABLE 2 settings.
Check digital input connections.
Check fieldbus communication settings.
2023
EMERGENCY
STOP
bit 6
Drive has received
emergency stop command
and ramps to stop
according to ramp time
defined by parameter
EMER DEC TIME.
Check that it is safe to continue operation.
Return emergency stop push button to normal position.
CODE
ALARM
CAUSE
WHAT TO DO
Summary of Contents for ACS350 Series
Page 1: ...ACS350 User s Manual ACS350 Drives 0 37 22 kW 0 5 30 HP ...
Page 4: ......
Page 8: ...Safety 8 ...
Page 18: ...Table of contents 18 ...
Page 24: ...Hardware description 24 ...
Page 44: ...Installation checklist 44 ...
Page 56: ...Start up control with I O and ID Run 56 ...
Page 140: ...Program features 140 ...
Page 242: ...Actual signals and parameters 242 ...
Page 266: ...Fieldbus control with embedded fieldbus 266 ...
Page 284: ...Fault tracing 284 ...
Page 288: ...Maintenance and hardware diagnostics 288 ...
Page 309: ...Dimensions 309 Frame size R2 IP20 NEMA 1 3AFE68586658 A Frame size R2 IP20 NEMA 1 VAR EMC ...
Page 311: ...Dimensions 311 Frame size R3 IP20 NEMA 1 3AFE68579872 B Frame size R3 IP20 NEMA 1 VAR EMC ...
Page 313: ......