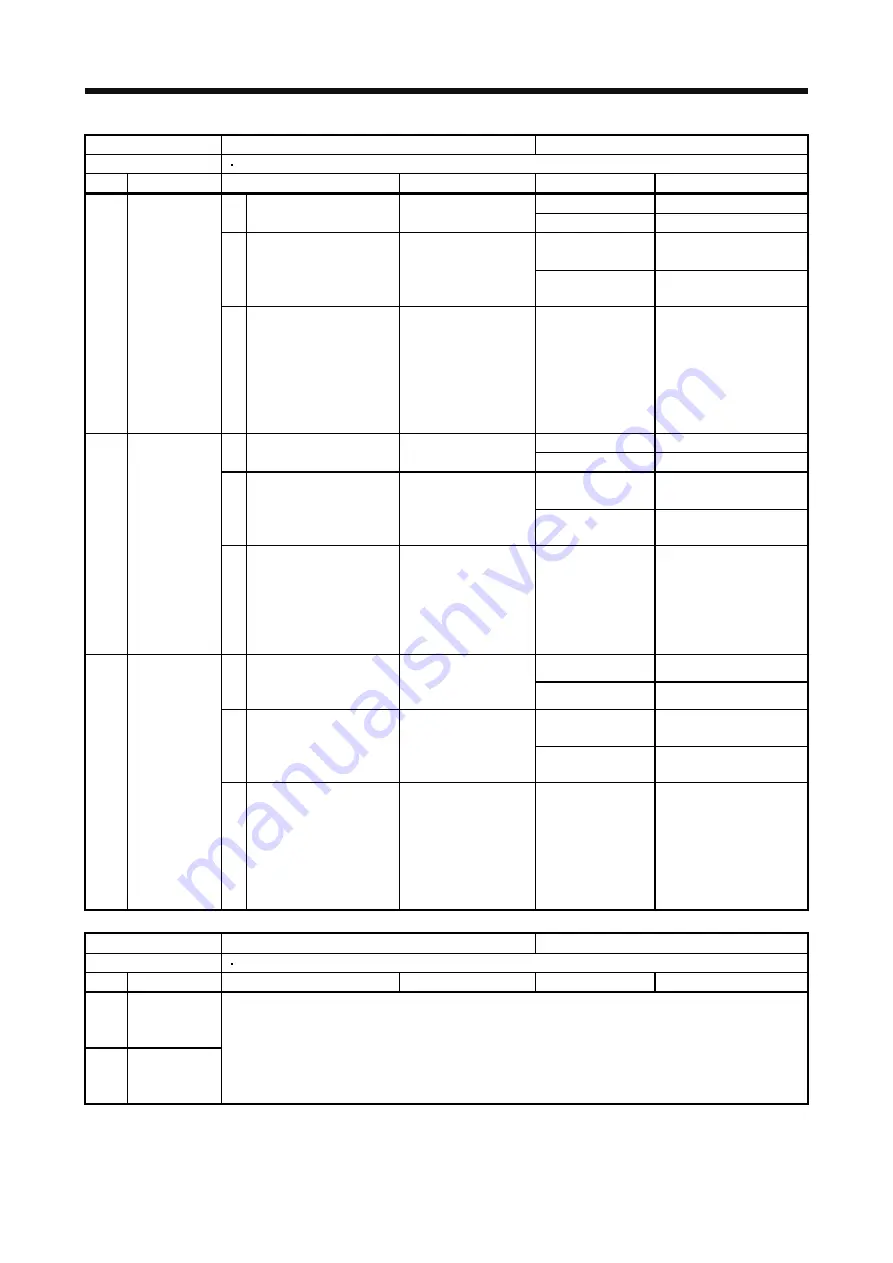
14. USING A DIRECT DRIVE MOTOR
14 - 52
Alarm No.: 42
Name: Servo control error
Stop system: Each axis
Alarm content
A servo control error occurred.
Display
Detail name
Cause
Check method
Check result
Action
42.1
Problem found.
Wire it correctly.
1) Connection of the direct
drive motor is not correct.
Check the wiring.
No problem found.
Check 2).
Servo control
error by position
deviation
It is not repeatable.
Execute the magnetic pole
detection.
2) The initial magnetic pole
detection was not
executed.
Execute the magnetic
pole detection again,
and then check the
repeatability.
It is repeatable.
Check 3).
3) The position deviation
reached the detection level.
Check the operation
status.
(Check the value of
droop pulses.)
The deviation is
large.
Review the operation
status.
Review the setting of
parameter No.PS05 (Servo
control position deviation
error detection level) as
required.
42.2
Problem found.
Wire it correctly.
1) Connection of the direct
drive motor is not correct.
Check the wiring.
No problem found.
Check 2).
Servo control
error by speed
deviation
It is not repeatable.
Execute the magnetic pole
detection.
2) The initial magnetic pole
detection was not
executed.
Execute the magnetic
pole detection again,
and then check the
repeatability.
It is repeatable.
Check 3).
3) The speed deviation
reached the detection level.
Check the operation
status.
(Calculate the deviation
between the speed
command and direct
drive motor speed.)
The deviation is
large.
Review the operation
status. Review the setting
of parameter No.PS06
(Servo control speed
deviation error detection
level) as required.
42.3
Problem found.
Wire it correctly.
Servo control
error by torque
detection
1) Connection of the direct
drive motor is not correct.
Check the wiring.
No problem found.
Check 2).
It is not repeatable.
Execute the magnetic pole
detection.
2) The initial magnetic pole
detection was not
executed.
Execute the magnetic
pole detection again,
and then check the
repeatability.
It is repeatable.
Check 3).
3) The thrust deviation
reached the detection level.
Check the operation
status.
(Calculate the deviation
between the current
command and torque.)
The deviation is
large.
Review the operation
status.
Review the setting of
parameter No.PS07 (Servo
control torque deviation
error detection level) as
required.
Alarm No.: 45
Name: Main circuit device overheat
Stop system: All axes
Alarm content
Inside of the servo amplifier overheated.
Display
Detail name
Cause
Check method
Check result
Action
45.1 Main
circuit
device overheat
error
45.5 Board
temperature
error
Same as for the rotary servo motors.
Refer to section 8.3.
Содержание MELSERVO-J3W Series
Страница 17: ...8 MEMO ...
Страница 27: ...1 FUNCTIONS AND CONFIGURATION 1 10 MEMO ...
Страница 87: ...4 STARTUP 4 14 MEMO ...
Страница 117: ...5 PARAMETERS 5 30 MEMO ...
Страница 129: ...6 GENERAL GAIN ADJUSTMENT 6 12 MEMO ...
Страница 185: ...10 CHARACTERISTICS 10 8 MEMO ...
Страница 241: ...11 OPTIONS AND AUXILIARY EQUIPMENT 11 56 MEMO ...
Страница 274: ...13 USING A LINEAR SERVO MOTOR 13 25 1 2 3 4 ...