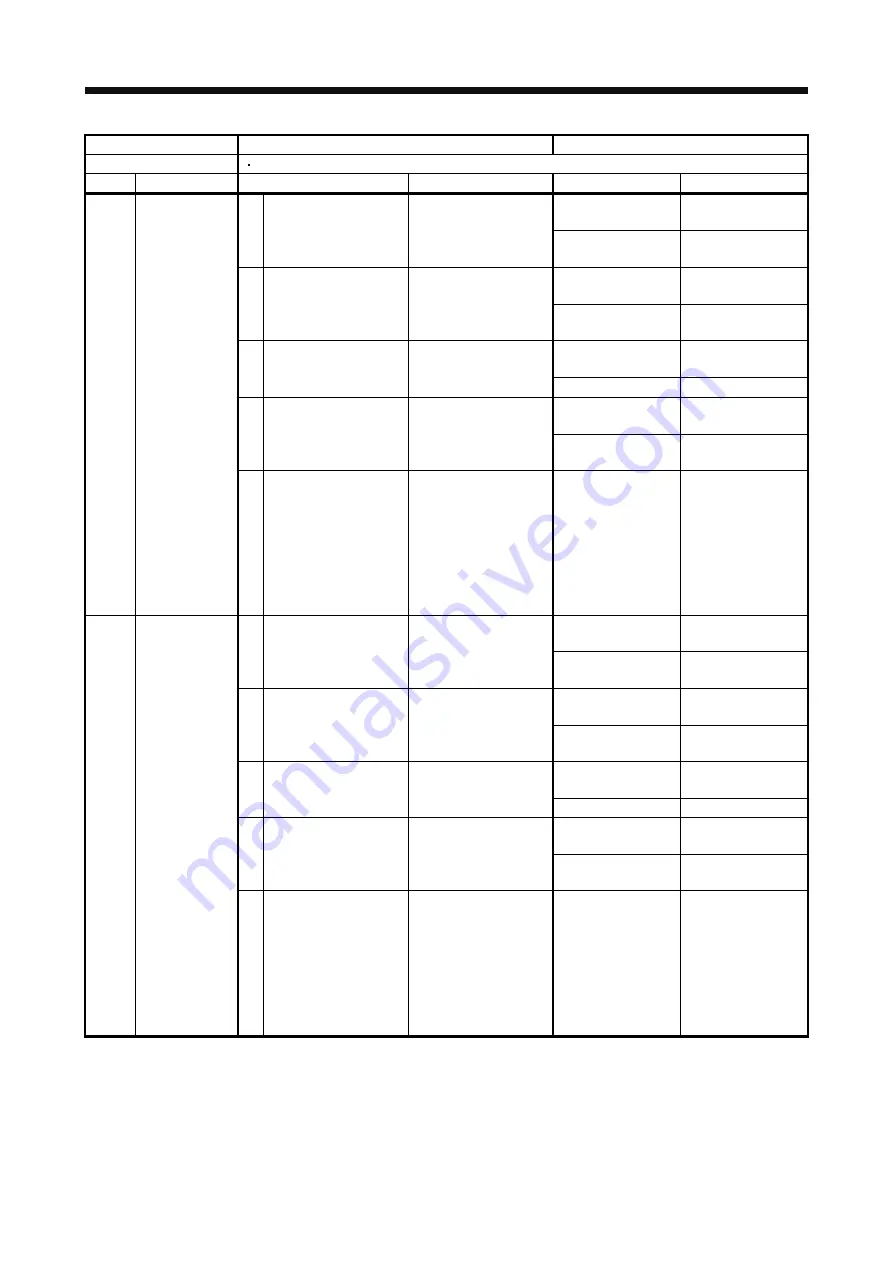
13. USING A LINEAR SERVO MOTOR
13 - 72
Alarm No.42
Name: Linear servo control error
Stop method: Corresponding axis stops
Alarm description
Linear servo control error occurs.
Display Name
Cause
Checkpoint
Finding
Action
42.1
(1)
Setting is incorrect.
Correct the setting.
Linear servo
control error on
the positioning
detection
Resolution of the linear
encoder and the
resolution setting of the
parameter are different.
Review the parameter
No.PS02 and PS03
settings.
Setting is correct.
Check (2).
(2)
The polarity is
incorrect.
Correct the setting.
Polarity of the linear
encoder is incorrect.
(Installation direction is
incorrect.)
Check polarities of the
linear encoder and the
linear servo motor.
Normal. Check
(3).
(3) Connection of the linear
servo motor is incorrect.
Check the wiring.
Problem found.
Perform wiring
correctly.
Normal.
Check
(4).
(4)
Not reproduced.
Perform the magnetic
pole detection.
Initial magnetic pole
detection is not
performed.
Perform the magnetic
pole detection again, and
check the reproducibility
of the error.
Reproduced. Check
(5).
(5)
Position
deviation
reaches the detection
level.
Check the operation
status.
(Check the number of
droop pulses.)
Deviation is large.
Review the operation
status.
Review the parameter
No.PS05 (Linear
servo motor control
position deviation error
detection level) setting
as required.
42.2
(1)
Setting is incorrect.
Correct the setting.
Linear servo
control error on
the speed
detection
Resolution of the linear
encoder and the
resolution setting of the
parameter are different.
Review the parameter
No.PS02 and PS03
settings.
Setting is correct.
Check (2).
(2)
The polarity is
incorrect.
Correct the setting.
Polarity of the linear
encoder is incorrect.
(Installation direction is
incorrect.)
Check polarities of the
linear encoder and the
linear servo motor.
Normal. Check
(3).
(3) Connection of the linear
servo motor is incorrect.
Check the wiring.
Problem found.
Perform wiring
correctly.
Normal.
Check
(4).
(4)
Not reproduced.
Perform the magnetic
pole detection.
Initial magnetic pole
detection is not
performed.
Perform the magnetic
pole detection again, and
check the reproducibility
of the error.
Reproduced. Check
(5).
(5) Speed deviation reaches
the detection level.
Check the operation
status.
(Calculate the deviation
between the speed
command and the linear
servo motor speed.)
Deviation is large.
Review the operation
status.
Review the parameter
No.PS06 (Linear
servo motor control
speed deviation error
detection level) setting
as required.
Содержание MELSERVO-J3W Series
Страница 17: ...8 MEMO ...
Страница 27: ...1 FUNCTIONS AND CONFIGURATION 1 10 MEMO ...
Страница 87: ...4 STARTUP 4 14 MEMO ...
Страница 117: ...5 PARAMETERS 5 30 MEMO ...
Страница 129: ...6 GENERAL GAIN ADJUSTMENT 6 12 MEMO ...
Страница 185: ...10 CHARACTERISTICS 10 8 MEMO ...
Страница 241: ...11 OPTIONS AND AUXILIARY EQUIPMENT 11 56 MEMO ...
Страница 274: ...13 USING A LINEAR SERVO MOTOR 13 25 1 2 3 4 ...