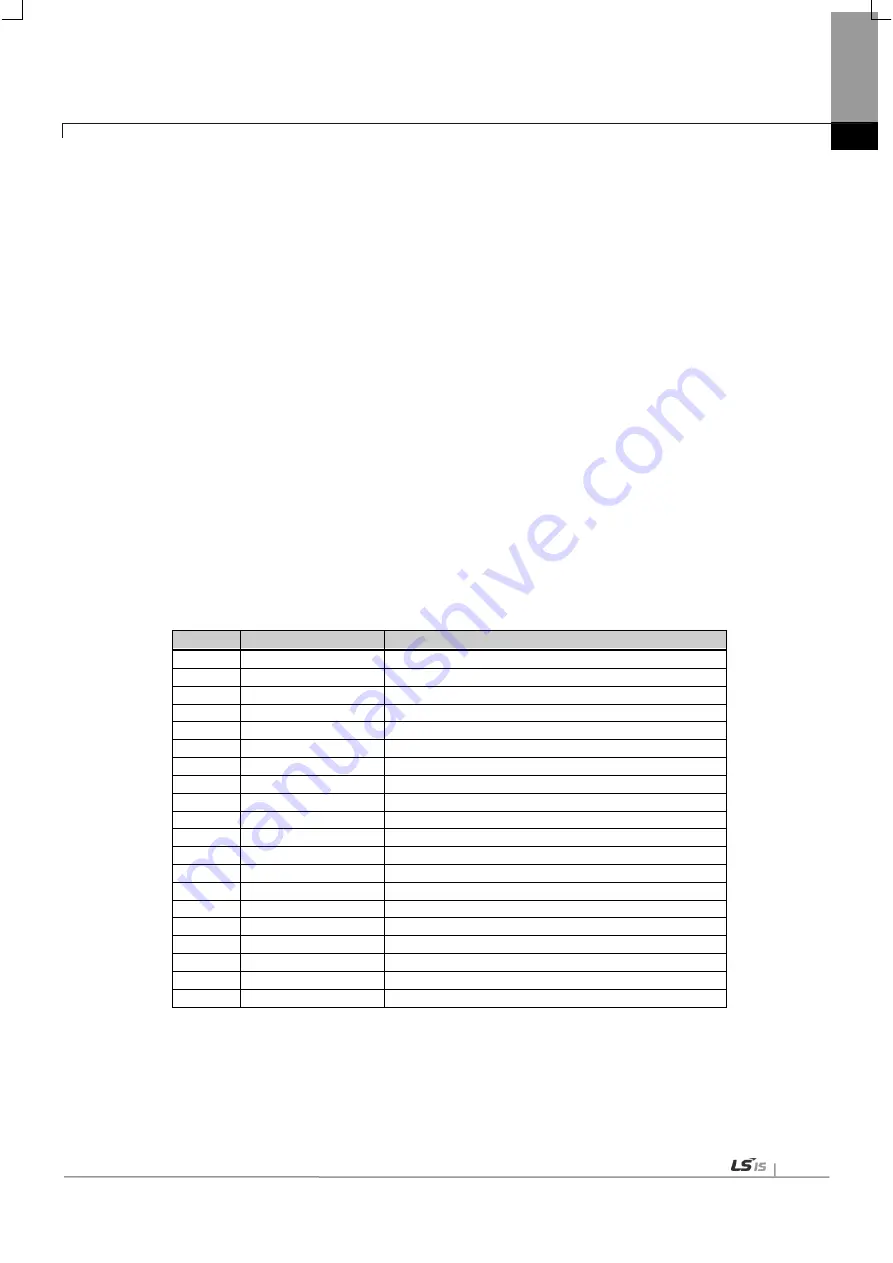
Chapter 8 Program
8-35
(a) Condition of Point Operation
Condition of Point Operation Command (XPST) Point Operation Step Writing (XPWR)
XPWR has to be done before execute the Point Operation.
(b) Axis ready status
If communication between positioning module and servo drive is done, the signal corresponding to each signal
will be on.
(c) Operating state by axis
According to exercise from “Chapter 8.1.2 Current State Reading,” it is a signal of “Operating” for each axis. It
turns on when it is operating. Point operation start command can not be configured while it is running hence
configuration will only be configured when it is not running. If you execute Point Operation while it is running,
the “error 231” would be appeared.
(d) Error state for each axis
According to exercise from “Chapter 8.1.2 Current State Reading,” it is a signal of “Error state” for each axis. It
turns on when an er ror occurred. Operation will only work when there is no error. If you want to operate a
system regardless of errors, you can just inactivate the function.
(e) Servo On signal
When applying the example program of “8.1.2 Current State Read”, this is “Servo On” signal for each axis.
When each axis is Servo On state, it will be on. Since “Point operation start” command can’t be executed
when the axis is not servo on, it makes command executed when servo driver is “Servo On” state.
(f) Address of Positioning Module
In this example, Positioning Module installed at the slot no.3 of 0 bases.
(g) Axis of command execution
You can set an axis for Point Operation. XBF-PN04(8)B can supports for 4(8) axes. In the “execution of axis”
from the configuration of Point Operation, you can set a value for axis 1 through 4(8) axis.
(h) Address of first device where those data for Step Numbers of Point Operation are saved
To execute a Point Operation, you need to set a specific value first. XPWR commands are using for set up
those Point Operation steps. It has to be done before actual Point Operation. Point Operation Step Data will be
set up depends on number of first device as below table.
Value
Device No.
Point start step data
1
0
Point start step data 1
2
1
Point start step data 2
3
2
Point start step data 3
4
3
Point start step data 4
5
4
Point start step data 5
6
5
Point start step data 6
7
6
Point start step data 7
8
7
Point start step data 8
9
8
Point start step data 9
10
9
Point start step data 10
11
10
Point start step data 11
12
11
Point start step data 12
13
12
Point start step data 13
14
13
Point start step data 14
15
14
Point start step data 15
16
15
Point start step data16
17
16
Point start step data17
18
17
Point start step data18
19
18
Point start step data19
20
19
Point start step data20
(i) Amount of Saving Point Operation Steps
Decide how many data will be saved by using XTWR command. In this example above, 10 Point Operation
steps are saved in the axis 1. Therefore those Step data from D01450~D01459 are saved in the module.
(j) Number of Operation amount by Point Operation
Set the number of saving Step numbers by Point Operating Writing command. For more information, reference
for Setting of Point Operation is in the “Chapter 9.2.18.”
Содержание XBF-PN04B
Страница 1: ...Programmable Logic Controller Positioning Module EtherCAT XGB Series XBF PN04B XBF PN08B ...
Страница 626: ...Chapter 9 Functions BPS37 setup RS232 and PC connection BPS37 option board LED 9 193 ...
Страница 628: ...Chapter 9 Functions c Execute BPS37 set up program and enter the setting values as follows 9 195 ...
Страница 796: ...Appendix3 Dimension A3 1 Appendix 3 Dimension Appendix 3 1 Dimension of XBF PN04B PN08B ...