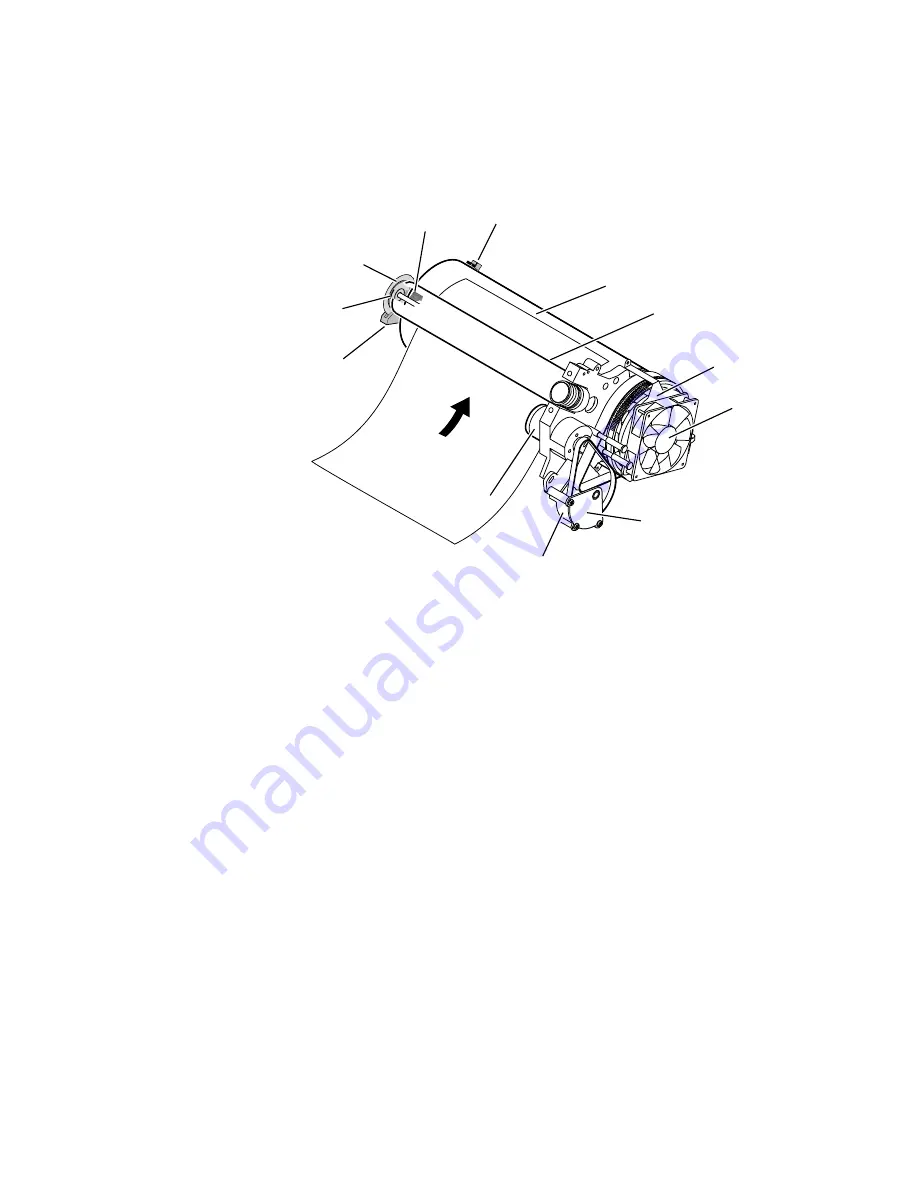
Service Manual
5-15
Theory of Operation
5
The drum is driven by a closed-loop servo motor which, through a double
reduction belt drive, rotates the drum at 112.8 rpm for imaging and a constant
low speed for image transfer to paper.
Warning
Keep your fingers away from the drum drive system; it uses a
closed-loop drive system. This closed-loop servo drive system is
dangerous since the motor torque increases if it senses the drum
slowing down. Fingers caught in the drum belts and gears can be
severely injured.
Figure 5-9 The drum/transfix assembly
Drum
Transfix roller
Drum
heater
9661-79
Fan
Belt drive
Servo motor
Warning: Closed-loop
servo drive
Paper
path
Home sensor
Temperature
sensor (~49
°
C)
Encoder
Encoder
disk
Home
flag
Summary of Contents for PHASER 380
Page 92: ......
Page 318: ......
Page 328: ......
Page 334: ......
Page 346: ...C 4 Phaser 380 Color Printer C Wiring Diagrams Figure C 6 Wire dressing behind the printhead...