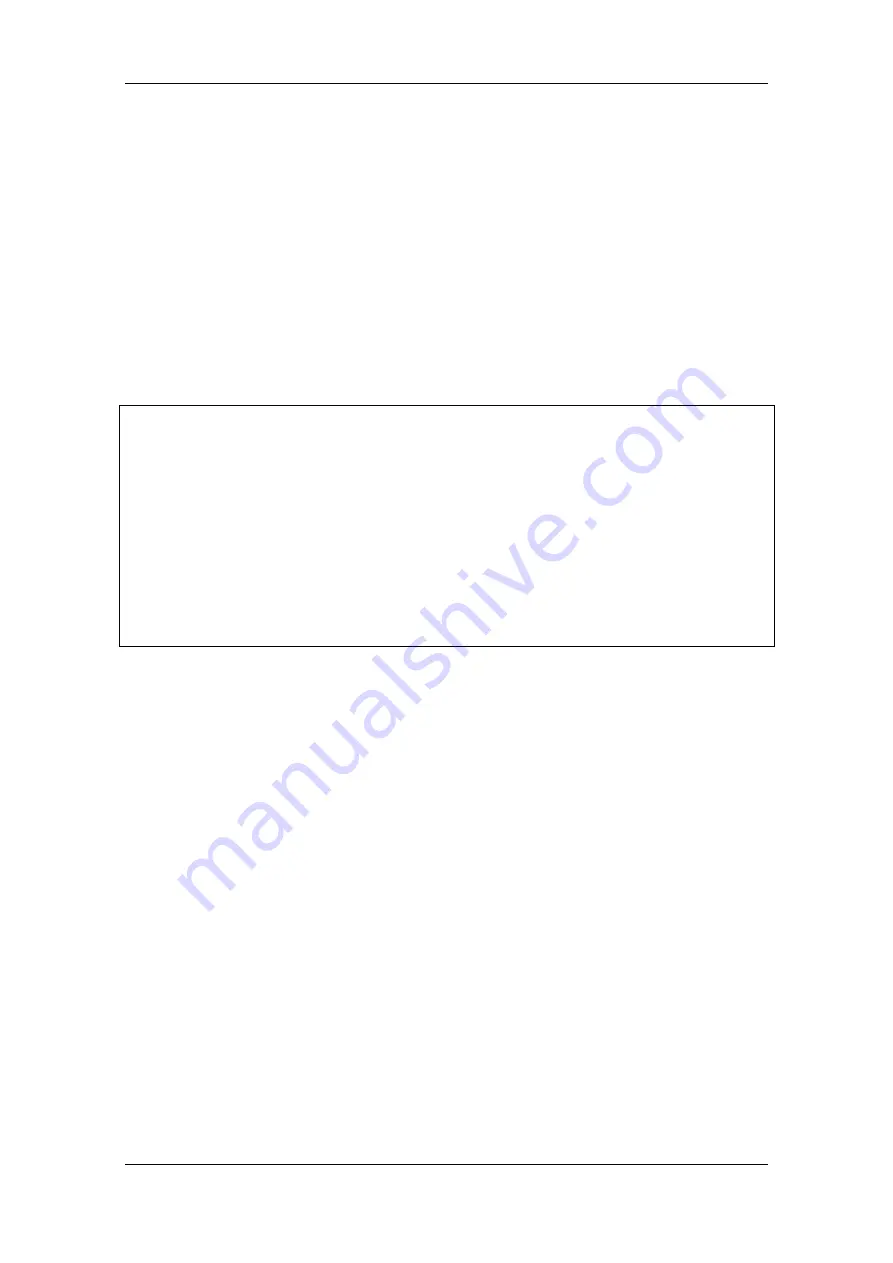
Technology Option F01
08.2012
6SE7087-6QX70 (Version AN) Siemens AG
9-140
Compendium Motion Control
SIMOVERT MASTERDRIVES
9.7.2.14
Setting the parameters for drive 1 (SIMOLINK slave)
In Sections 9.7.2.3 to 13, we commissioned drive 2 completely, step-
by-step with its positioning functions and the virtual master axis. We
can now focus on drive 1 and commission it for position control mode
before we tackle the testing of the SIMOLINK and the synchronization
functions.
The procedure for setting the parameters and commissioning the
positioning functions for drive 1 is identical to the description in steps 3
to 12 for drive 2. You can omit steps 10 and 11, since the virtual master
axis is not required in drive 1.
You can then configure the SIMOLINK drive interface for drive 1 as
slave ("transceiver") as follows:
; Configuration of the SIMOLINK slave (transceiver) [140+150]
P60=4
; Select the "board configuration" parameter menu
P740=1
; SIMOLINK address of drive 1 (>0 = "transceiver")
P741=100ms
; Message timeout
P742=1
; "Low output power" adequate with
; short cable
P749.01=0,0 ; 1st SIMOLINK receive double word KK7031 [150.7] =
; Channel 0 of station 0 (i.e. of master) = path
; setpoint of virtual master axis in drive 2
P749.02=0,1 ; 2nd SIMOLINK receive double word KK7032 =
; channel 1 of master (reserve channel) [150.7]
P60=1
; Exit board configuration
; SLB send words do not have to be wired, since
; drive 1 is only to receive, not send data
9.7.2.15
Testing the synchronization in the application example
Check whether the SIMOLINK fiber-optic cables are correctly
connected "crosswise" to the SLB boards (each transmitter connected
to the receiver of the other drive). If the wiring and configuration is
correct, all 3 LEDs should flash on all SLB boards.
Start the virtual master axis on drive 2 with the start switch (terminal 7),
and check at r750.01 and .02 [150.5] on drive 1 whether the virtual
master value transmitted from drive 2 is received correctly.
The further procedure for testing the synchronization function is
described below with reference to the example of the 2-axis
demonstration pack. An LED light beam visible through both flywheels
indicates that the synchronization function is operating correctly.
Checking the
SIMOLINK
connection