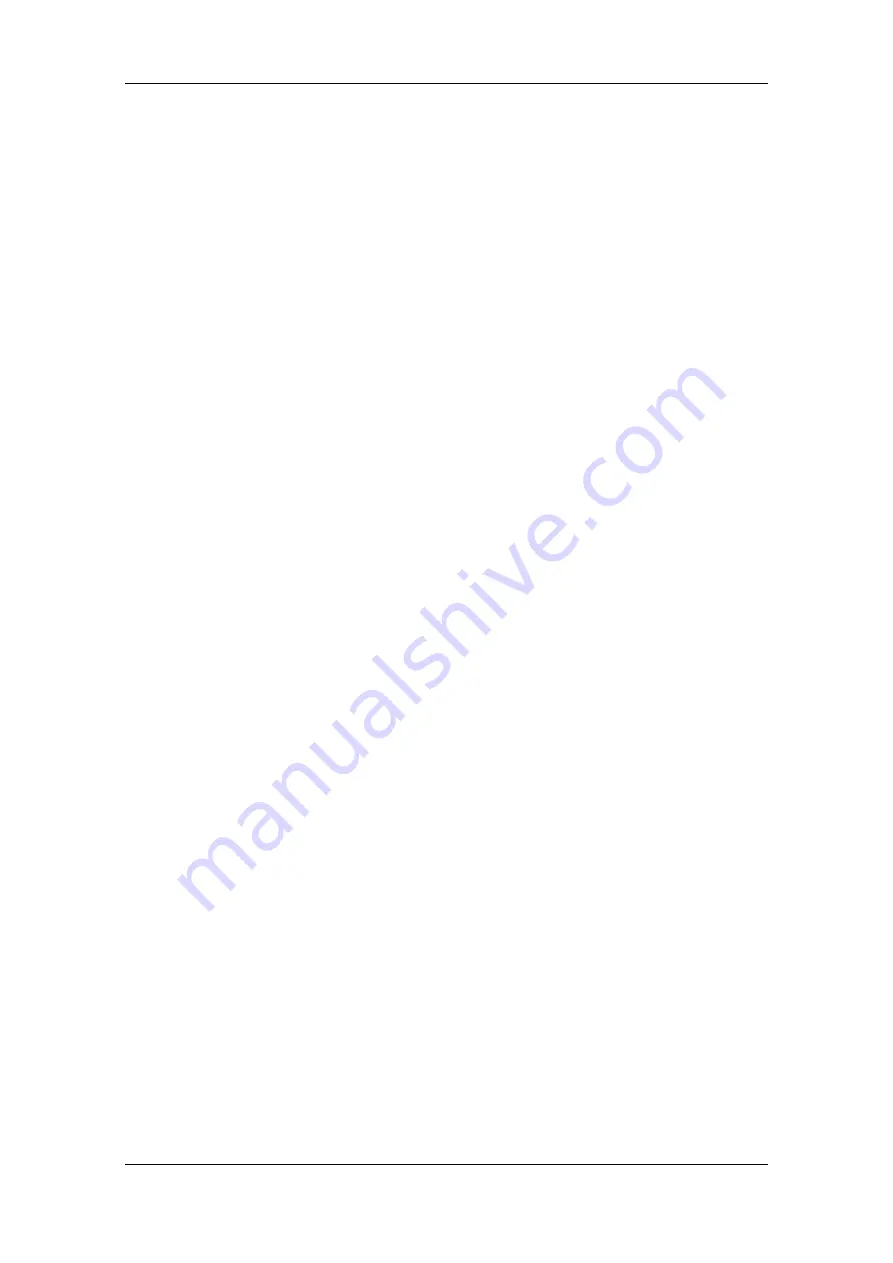
Technology Option F01
08.2012
6SE7087-6QX70 (Version AN) Siemens AG
9-126
Compendium Motion Control
SIMOVERT MASTERDRIVES
The numbers in circles indicate the corresponding areas on the
overview diagram.
The "mode", "acknowledge" and "MDI no." switches, which are
connected to the 4 digital inputs (
, function diagram, sheet [90]), are
routed to positioning control word [809]; the mode is generated from
free blocks via a small logic circuit (described below). The
"acknowledge" and "ON/OFF1" switches act directly on basic unit
control word 1 [180].
The mode selector
activates the synchronization
, homing
and
MDI (point-to-point positioning
) modes. The mode manager
ensures that the output signals of the active mode are switched through
to the setpoint command on the position and speed controller
.
The virtual master axis
contains the velocity ramp-function generator
for both drives and the "saw-tooth pulse generator" for the position
setpoint generation (master value, period corresponds to 10 motor
revolutions). The virtual master axis is only calculated on drive 2. It is
not activated on drive 1. This, and the velocity setpoint potentiometer,
which is only connected to drive 2, are the only differences in the
parameter settings for both drives. We will initially limit our description
to drive 2. The further procedure is as follows:
♦
Commission the positioning functions on drive 2 (sections
9.7.2.3...8).
♦
Test the positioning functions on drive 2 (section 9.7.2.8). Users
whose application only involves positioning can skip the following
steps.
♦
Commission the virtual master axis on drive 2.
♦
Test the virtual master axis on drive 2.
♦
Commission the synchronization on drive 2.
♦
Commission the positioning and synchronization functions on drive 1.
♦
Test the positioning and synchronization functions on drives 1 and 2.
The parameters marked with (WE) do not have to be entered, since the
factory settings are suitable.