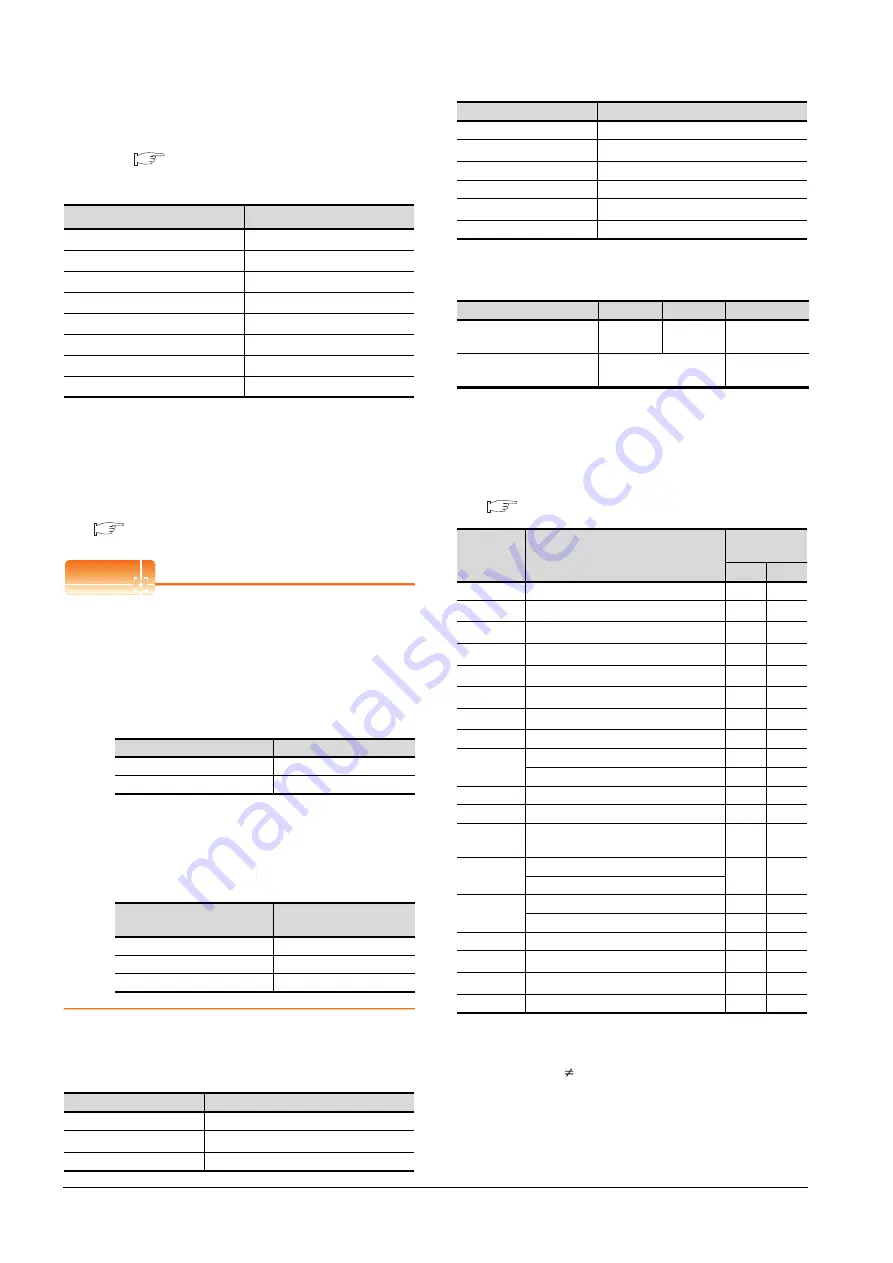
15 - 52
15. INVERTER CONNECTION
15.6 Device Range that Can Be Set
*2
Write a value to parameter Pr.185, Pr.186, Pr.188, or Pr.189
that corresponds to a signal within parentheses. Doing so
issues the corresponding run command (WS8 to WS11). For
the details of the inverter rameters, refer to the following.
Manual of the inverter used
(3) Alarm definition
*1
Only reading is possible for A0 to A7.
These devices cannot be used for a write object (numerical input etc.).
(4) Parameter
The numbers of virtual devices for inverter (parameter
(Pr)), used by GOT, correspond to the inverter
parameter numbers.
For the inverter parameters, refer to the following.
Manual of the inverter being used
POINT
POINT
POINT
(1) Monitoring Pr.37
GOT cannot monitor the parameter (Pr.37) of
FREQROL-E500/S500(E)/F500J/D700/F700PJ/
E700.
(2) When setting "8888" or "9999" to inverter parameter (Pr)
"8888" and "9999" designate special function.
To set these numbers from GOT, designate a
number as shown below.
(3) Precautions for setting calibration parameter
(Pr900 to Pr905)
When setting a calibration parameter (Pr900 to
Pr905), it is necessary to set the value below for
extension second parameter (SP108), depending on
the device number to be used and the inverter model.
(5) Programmed operation
The devices below correspond to the parameters
(Pr.201 to Pr.230) of FREQROL-A500 series.
*1
To set the start time (PG10 to PG19, PG40 to PG49, PG70
to PG79), set hour or minute in the upper 8bits, and minute
or second in the lower 8bits.
Example) To set 13 hour 35 minute
(6) Special parameter
The numbers of the inverter’s virtual devices (SP) used
for the GOT correspond to instruction codes of the
inverter communication function.
For instruction details, and values to be read and
written, refer to the following,
Manual of the inverter used
*1
GOT cannot monitor SP109 to SP111 if the conditions below
are satisfied at the same time.
(Only FREQROL-E500/S500(E)/F500J/D700/F700PJ/E700
series)
• Pr37 0
• SP127 = 1
*2
Only reading is possible for SP111 to SP114.
These devices cannot be used for a write object (numerical
input etc.).
*3
Only writing is possible for SP124 and SP125.
These devices cannot be used for read object.
Device name
*1
Description
A0
Second alarm in past
A1
Latest alarm
A2
Fourth alarm in past
A3
Third alarm in past
A4
Sixth alarm in past
A5
Fifth alarm in past
A6
Eighth alarm in past
A7
Seventh alarm in past
Set value of inverter side
Value specified by GOT
8888
65520
9999
65535
Value to be set to extension
second parameter (SP108)
Description
H00
Offset/gain
H01
Analog
H02
Analog value at terminal
Device name
Description
PG0
to
PG9
Program set 1 (running frequency)
PG10
to
PG19
*1
Program set 1 (time)
PG20
to
PG29
Program set 1 (rotation direction)
PG30
to
PG39
Program set 2 (running frequency)
PG40
to
PG49
*1
Program set 2 (time)
PG50
to
PG59
Program set 2 (rotation direction)
PG60
to
PG69
Program set 3 (running frequency)
PG70
to
PG79
*1
Program set 3 (time)
PG80
to
PG89
Program set 3 (rotation direction)
Time to be set
13H
35M
Remark
Convert "hour" and "minute"
into hexadecimal.
H0D
H23
HEX
Combine upper and lower 8-
bit values.
Input H0D23 or 3363.
-
Device
name
Description
Instruction
code
Read
Write
SP108
Second parameter changing
6C
H
EC
H
SP109
*1
Set frequency (RAM)
6D
H
ED
H
SP110
*1
Set frequency (RAM, E
2
PROM)
6E
H
EE
H
SP111
*1*2
Output frequency
6F
H
-
SP112
*2
Output current
70
H
-
SP113
*2
Output voltage
71
H
-
SP114
*2
Special monitor
72
H
-
SP115
Special monitor selection No.
73
H
F3
H
SP116
Alarm definition all clear
-
F4
H
Latest alarm, second alarm in past
74
H
-
SP117
Third alarm in past, fourth alarm in past
75
H
-
SP118
Fifth alarm in past, sixth alarm in past
76
H
-
SP119
Seventh alarm in past, eights alarm in
past
77
H
-
SP121
Inverter status monitor (extended)
79
H
F9
H
Run command (extend)
SP122
Inverter status monitor
7A
H
-
Run command
-
FA
H
SP123
Communication mode
7B
H
FB
H
SP124
*3
All parameter clear
-
FC
H
SP125
*3
Inverter reset
-
FD
H
SP127
Link parameter extended setting
7F
H
FF
H
Device name
Description
Summary of Contents for GT15
Page 2: ......
Page 34: ...A 32 ...
Page 92: ......
Page 110: ...2 18 2 DEVICE RANGE THAT CAN BE SET 2 9 MELSEC WS ...
Page 186: ...5 10 5 BUS CONNECTION 5 2 System Configuration ...
Page 218: ...5 42 5 BUS CONNECTION 5 4 Precautions ...
Page 254: ...6 36 6 DIRECT CONNECTION TO CPU 6 6 Precautions ...
Page 286: ...7 32 7 COMPUTER LINK CONNECTION 7 6 Precautions ...
Page 350: ...8 64 8 ETHERNET CONNECTION 8 5 Precautions ...
Page 368: ...9 18 9 MELSECNET H CONNECTION PLC TO PLC NETWORK 9 5 Precautions ...
Page 420: ...11 26 11 CC Link IE CONTROLLER NETWORK CONNECTION 11 5 Precautions ...
Page 440: ...12 20 12 CC Link IE FIELD NETWORK CONNECTION 12 5 Precautions ...
Page 490: ...13 50 13 CC Link CONNECTION INTELLIGENT DEVICE STATION 13 5 Precautions ...
Page 510: ......
Page 564: ...15 54 15 INVERTER CONNECTION 15 7 Precautions ...
Page 668: ......
Page 712: ...21 12 21 MULTIPLE GT14 GT12 GT11 GT10 CONNECTION FUNCTION 21 5 Precautions ...
Page 713: ...MULTI CHANNEL FUNCTION 22 MULTI CHANNEL FUNCTION 22 1 ...
Page 714: ......
Page 760: ...22 46 22 MULTI CHANNEL FUNCTION 22 5 Multi channel Function Check Sheet ...
Page 761: ...FA TRANSPARENT FUNCTION 23 FA TRANSPARENT FUNCTION 23 1 ...
Page 762: ......
Page 860: ...REVISIONS 4 ...
Page 863: ......