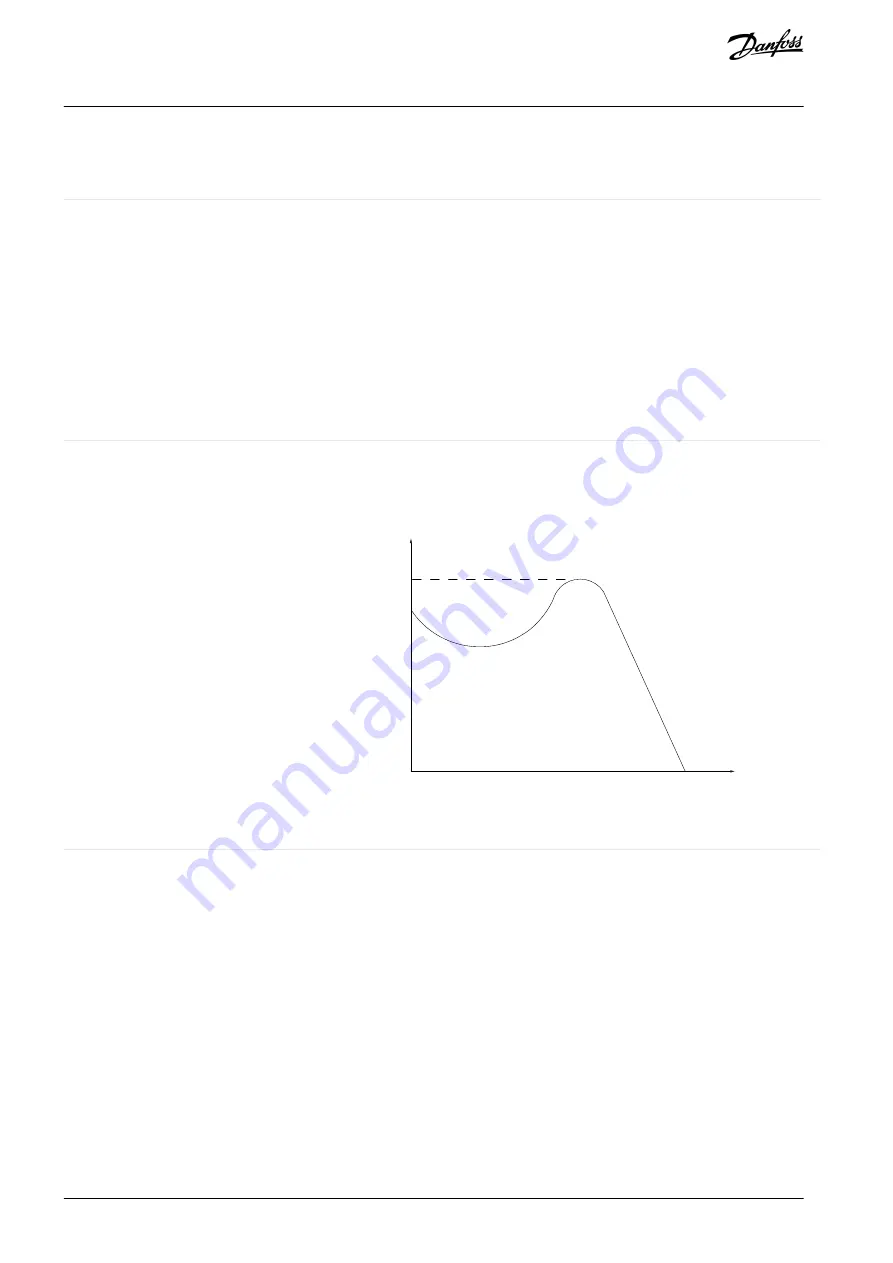
VLT FC 321 Glossary
A
Actual position
The actual position from an encoder, or a value that the motor control cal-
culates in open loop. The drive uses the actual position as feedback for po-
sition PI.
Analog reference
A signal transmitted to the analog inputs 53 or 54 (voltage or current).
Analog inputs
The analog inputs are used for controlling various functions of the drive.
There are 2 types of analog inputs:
Current input, 0–20 mA, and 4–20 mA
Voltage input, -10 V DC to +10 V DC.
Analog outputs
The analog outputs can supply a signal of 0–20 mA, 4–20 mA.
B
BDM
A BDM is a drive module, which consists of a power converter module and a
control and regulating device for speed, torque, current, or voltage.
Binary reference
A signal transmitted to the serial communication port.
Break-away torque
e
7
5
za
0
7
8
.1
0
(1)
(2)
(3)
C
CDM
A CDM is a drive system without the motor and without the measuring sen-
sors, which are mechanically connected to the motor shaft. The drive sys-
tem consists of, but is not restricted to, the BDM and extensions, such as the
feed module and auxiliary equipment.
CT characteristics
Constant-torque characteristics used for all applications such as conveyor
belts, displacement pumps, and cranes.
Commanded position
The actual position reference calculated by the profile generator. The drive
uses the commanded position as setpoint for position PI.
Control command
Functions are divided into 2 groups.
Functions in group 1 have higher priority than functions in group 2.
AU373327181955en-000101/130R1208
374 | Danfoss A/S © 2021.08
Glossary
VLT® AutomationDrive EZ FC 321
Programming Guide