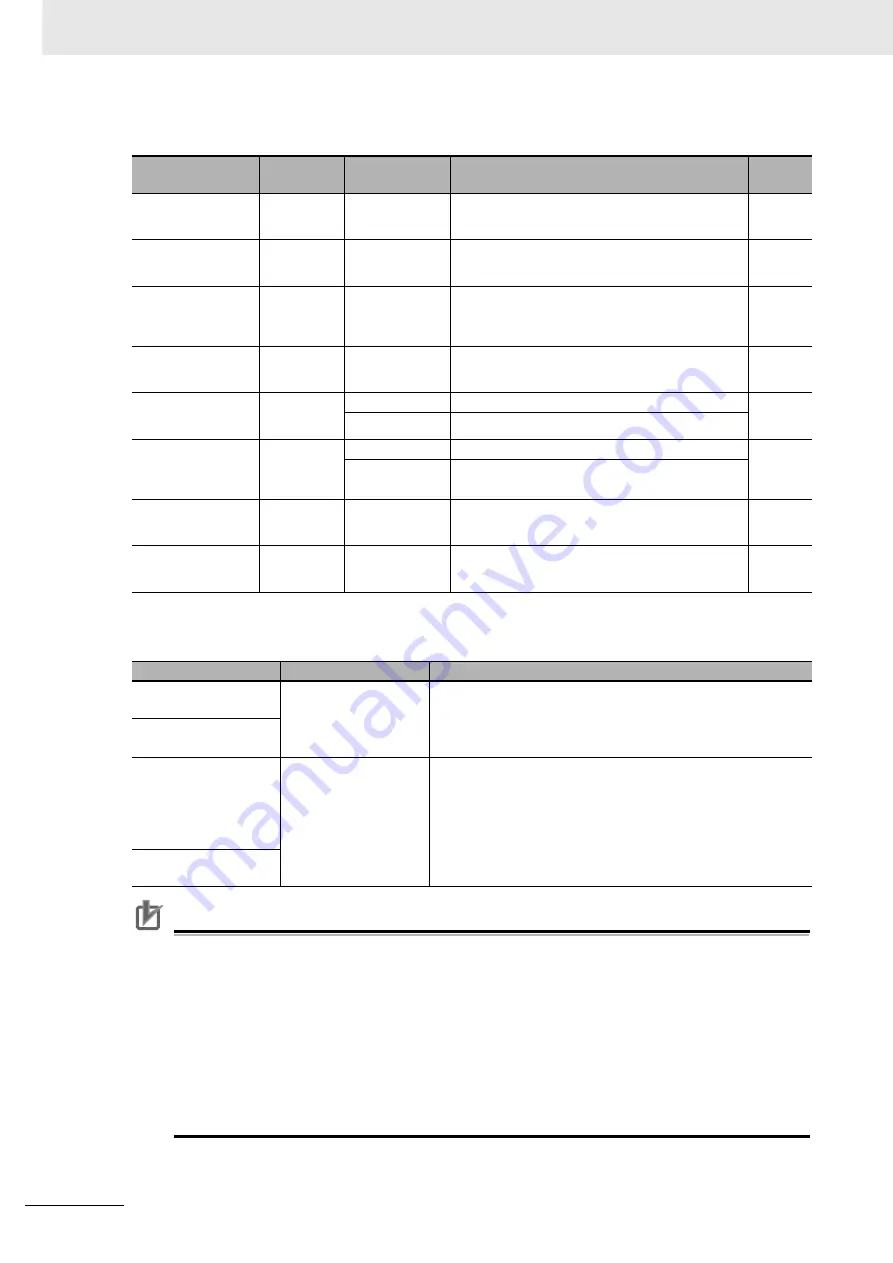
7 Advanced Settings
7 - 18
High-function General-purpose Inverter RX2 Series User’s Manual
Parameter
In addition to the adjustment of the sensorless vector control, refer to the following description.
Precautions for Correct Use
• Set the carrier speed setting, 1st-motor [bb101] at a value of 2.0 kHz or higher. A set fre-
quency of 1.9 kHz or lower may cause hunting.
• When the revolution of the motor is hindered by such causes as the braking or the motor lock
caused by foreign objects, such hindrance may cause over current or the like. When no such
adjustment as ones mentioned above improves the state, checking the portion around the
motor may sometimes improves it.
• If an application of load results in a great amount of change in the inverter’s output frequency
monitor [dA-01], a function to automatically change the frequencies for the overload limiting
function, the momentary-stop non-stop function, the over voltage suppression function may
work depending upon the settings of the functions.
Item
Parameter
Data
Description
Default
data
Control mode
selection,
1st-motor
[AA121]
09
*1
*1. Cannot be selected if [Ub-03] duty spec selection is 01 (LD) or 00 (VLD).
To use the zero-speed range sensorless vector
control (IM) function.
00
Speed response
for Async.M,
1st-motor
[HA115]
0 to 1000(%)
To adjust the responsiveness of the control.
A larger value enhances the responsiveness.
100
Zero speed area
limit for
Async.M-0SLV,
1st-motor
[HC110]
0 to 100(%)
To limit the current at the start so as not to allow
the rising of the current to rise too high.
80
Boost value at start
for Async.M-0SLV,
1st-motor
[HC112]
0 to 50(%)
To adjust the current command at the start when
the starting torque is not sufficient.
10
Secondary resis-
tance correction,
1st-motor
[HC113]
00
Disabled
00
01
Enabled Requiring a temperature thermistor.
Counter direction
run protection
selection,
1st-motor
[HC114]
00
Disabled
00
01
Enabled Limit the output to prevent the output in
the reverse direction.
Torque current ref-
erence filter time
constant, 1st-motor
[HC120]
0 to 100(ms)
To adjust the filter for the torque current.
2
Speed feedfor-
ward compensa-
tion gain, 1st-motor
[HC121]
0 to 1000(%)
To adjust the feed forward control of the speed
controller.
0
Phenomenon
Estimated cause(s)
Exemplar measures to be taken
Socks occur during the
revolutions at the start. Boost amount is too
large.
• Make an adjustment by decrementing the zero-speed range
limiter [HC110] by 5% each time.
• Make an adjustment by decrementing the zero-speed range
boost at the start [HC112] by 5% each time.
Over current occurs at
the start
The motor cannot pro-
vide enough torque for
the load is too high for
the motor to at the
start.
Boost amount is too
small.
Make an adjustment by incrementing the zero-speed range
boost at the start [HC112] by 5% each time.
Acceleration is not
possible.
Содержание RX - 2
Страница 1: ...High function General purpose Inverter RX2 Series User s Manual I620 E1 01 3G3RX2...
Страница 54: ...1 Overview 1 22 High function General purpose Inverter RX2 Series User s Manual...
Страница 136: ...2 Design 2 82 High function General purpose Inverter RX2 Series User s Manual...
Страница 592: ...8 Applied Settings 8 192 High function General purpose Inverter RX2 Series User s Manual...
Страница 754: ...11 Options 11 56 High function General purpose Inverter RX2 Series User s Manual...
Страница 794: ...12 Troubleshooting 12 40 High function General purpose Inverter RX2 Series User s Manual...
Страница 919: ......