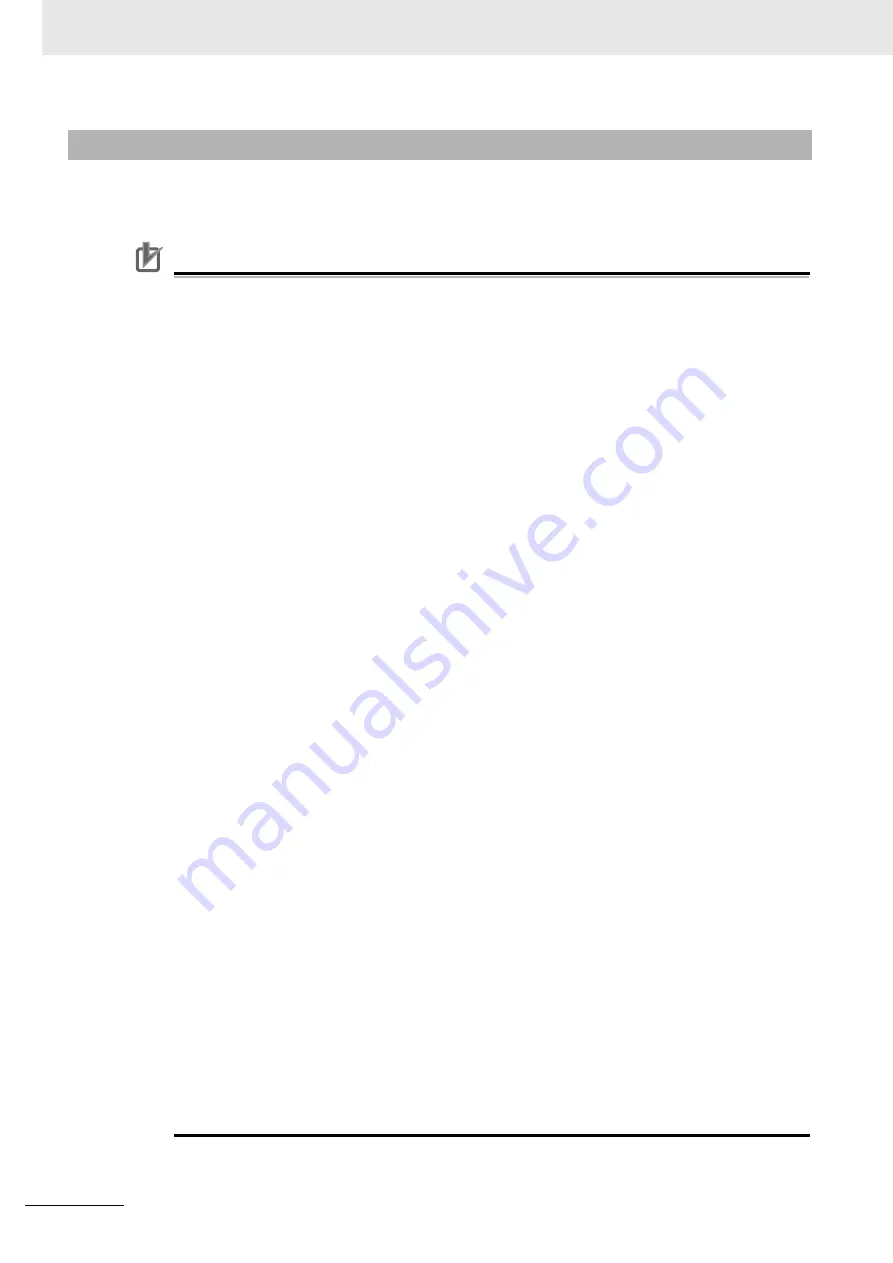
7 Advanced Settings
7 - 22
High-function General-purpose Inverter RX2 Series User’s Manual
Controlling a synchronous motor (permanent magnet motor) requires the setting-up of the motor con-
stant. See,
6-2 Parameter Setting for Motor Related
on page 6-8 The motor constant is data corre-
sponding to one phase of Y-connection (including wiring).
Precautions for Correct Use
• Set an appropriate over current level of the inverter [bb160]. Do not drive a motor whose
maximum current (demagnetization level) is below the 150% of [bb160].
• Be aware of the root-mean-square value and the peak value. The rated output current listed
in the specification table is the root-mean-square value.
• This is the control mode for the reducing torque applications where the motor that has the
same frame number as the inverter’s rating needs a torque at the start that is 50% or smaller.
• This mode can be used neither in applications that require a constant torque from low speeds
nor in applications that involve rapid acceleration or deceleration and that require a large
torque from low speeds. Never use this mode for applications involving a gravity load, such
as lifts.
• Synchronous motors (permanent magnet motors) cannot be operated by a direct input from
the commercial power supply.
• Multiple synchronous motors (permanent magnet motors) cannot be driven by a single
inverter.
• Synchronous motors (permanent magnet motors) are more likely to cause over voltage
errors than non-synchronous motors (induction motors). If the rapid deceleration and/or the
direct-current braking function need to be used, consider the possible use of an optional
braking resistor, a regenerative braking unit.
• When a hold brake is used, release the brake before the motor starts operation. Otherwise,
the motor may lose its synchronism.
• The motor may move in the reverse direction at the start of its revolution. When a malfunction
is caused by the reverse revolution, use the starting Method for Sync.M, 1st-motor [Hd132].
• Set the carrier speed setting, 1st-motor [bb101] at a value of 8.0kHz or higher. Some low car-
rier frequencies may make the motor generate a lot of heat.
• The tolerable load moment of inertia is 50 times as large as the motor’s moment of inertia or
smaller. Some applications whose loads moment of inertia exceed the above mentioned
range may result in a performance that is below the desired one.
• If the wiring length between the motor and the inverter is about 20m or longer, the motor
could not exhibit the full properties.
• In some cases of a long wiring (approximately longer than 20 m), frequency-synchronized
re-start may cause an over current error.
• Driving a motor whose sync.Motor rated current, 1st-motor [Hd108] exceeds the inverter’s
rated current or a motor whose frame number is smaller than the maximum applicable motor
by 2 or more may result in a performance that is below the desirable one.
• Set not only the sync.Motor rated current, 1st-motor [Hd108] but also the electronic thermal
level setting, 1st-motor [bC110].
• If the initial position estimation is enabled in the starting Method for Sync.M, 1st-motor
[Hd132], a shrill sound caused by the position detection action may be heard, but this sound
has nothing to do with any abnormality.
• If the initial position estimation is enabled in the Carrier speed setting, 1st-motor [Hd132],
start the operation from the state in which the motor stopped. Failure to acquire the correct
position may occur, which may result in unintended revolution, over current, or loss of syn-
chronization.
7-2-11 Synchronous Motor (Permanent Magnet Motor) Control
Содержание RX - 2
Страница 1: ...High function General purpose Inverter RX2 Series User s Manual I620 E1 01 3G3RX2...
Страница 54: ...1 Overview 1 22 High function General purpose Inverter RX2 Series User s Manual...
Страница 136: ...2 Design 2 82 High function General purpose Inverter RX2 Series User s Manual...
Страница 592: ...8 Applied Settings 8 192 High function General purpose Inverter RX2 Series User s Manual...
Страница 754: ...11 Options 11 56 High function General purpose Inverter RX2 Series User s Manual...
Страница 794: ...12 Troubleshooting 12 40 High function General purpose Inverter RX2 Series User s Manual...
Страница 919: ......