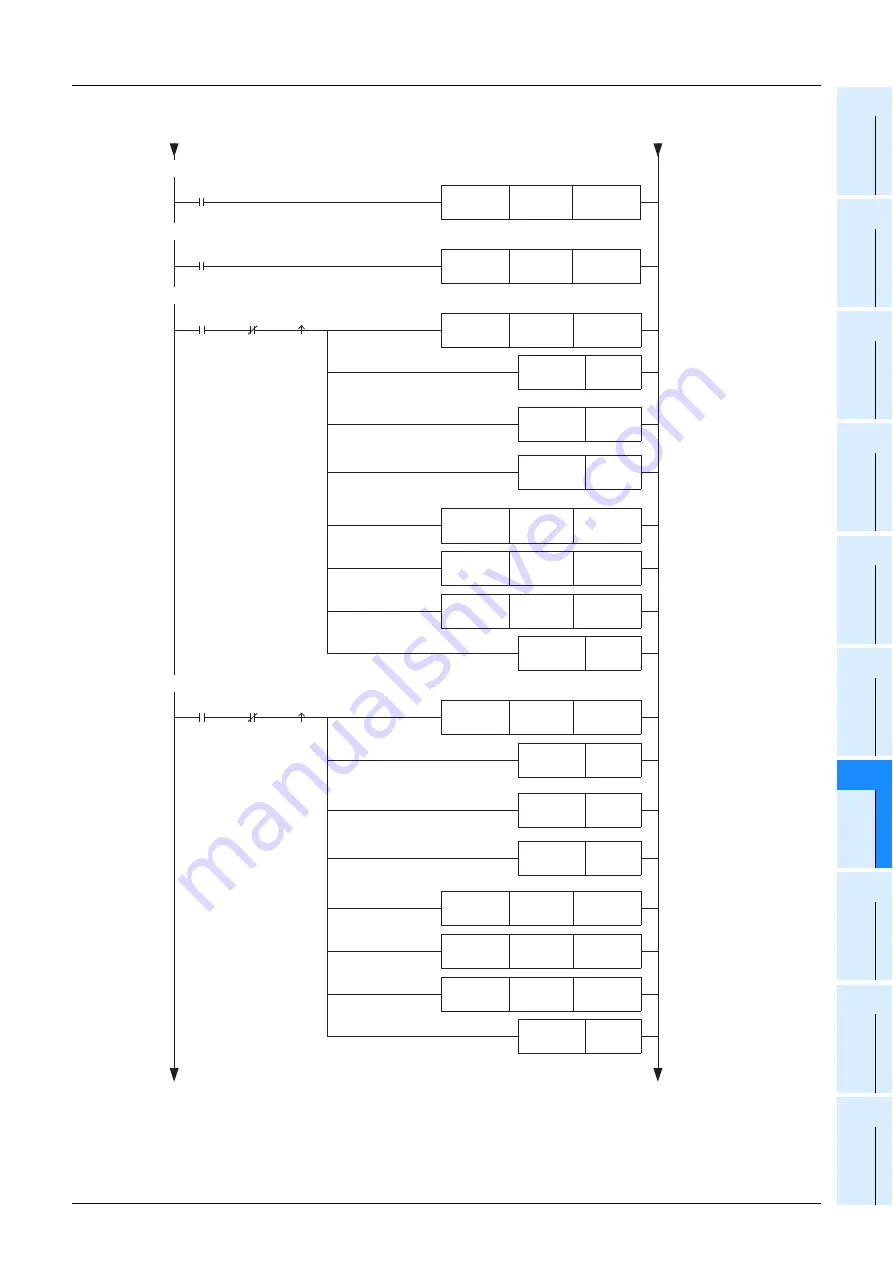
7 Before Starting Positioning Operation
101
FX
3U
-20SSC-H Positioning Block User's Manual
1
Int
roduct
ion
2
Sy
stem
conf
igur
ati
on
3
Exam
ple
C
onnect
ion
4
Ins
tall
a
tion
5
Wi
rin
g
6
Me
m
o
ry
confi
gur
at
ion
and da
ta
7
Befor
e
star
ting
positi
oning
contr
o
l
8
M
anual c
ont
ro
l
9
Posit
ioni
ng
C
ont
rol
10
Table O
per
at
ion
7.6 Changing During Operation (Operation Speed, Target Address)
To the next page
To the next page
From the previous page
From the previous page
M370
D270.E
During
target address
change flag
(X-axis)
RST
D272.C
Preparing to change the target position (X-axis)
U1\G518
D272
FNC 12
MOV
RST
D272.D
RST
D272.E
D272
U1\G518
FNC 12
MOV
K5000000
U1\G514
FNC 12
DMOV
SET
M372
Reads the operation
command 1 (X-axis) in
unit No. 1.
Resets the change
command in operation
disabled (X-axis) in unit
No. 1.
Resets the speed change
command in positioning
operation (X-axis) in
unit No. 1.
Resets the target position
change command in
positioning operation
(X-axis) in unit No. 1.
Sets (writes) the operation
command 1 (X-axis) in
unit No. 1.
Sets the target position
change value (address)
(X-axis) in unit No. 1.
Preparing to change the target position (Y-axis)
M371
D271.E
During
target address
change flag
(Y-axis)
RST
D273.C
U1\G618
D273
FNC 12
MOV
RST
D273.D
RST
D273.E
D273
U1\G618
FNC 12
MOV
K5000000
U1\G614
FNC 12
DMOV
Reads the operation
command 1 (Y-axis) in
unit No. 1.
Resets the change
command in operation
disabled (Y-axis) in unit
No. 1.
Resets the speed change
command in positioning
operation (Y-axis) in
unit No. 1.
Resets the target position
change command in
positioning operation
(Y-axis) in unit No. 1.
Sets (writes) the operation
command 1 (Y-axis) in
unit No. 1.
K2000000
U1\G516
FNC 12
DMOV
Sets the target position
change value (speed)
(X-axis) in unit No. 1.
SET
M373
K2000000
U1\G616
FNC 12
DMOV
Sets the target position
change value (address)
(Y-axis) in unit No. 1.
Sets the target position
change value (speed)
(Y-axis) in unit No. 1.
M370
Reads the status
information (X-axis) in
unit No. 1.
U1\G28
D270
FNC 12
MOV
U1\G128
D271
FNC 12
MOV
Reads the status
information (Y-axis) in
unit No. 1.
Reading the status information (X-axis)
Reading the status information (Y-axis)
M371