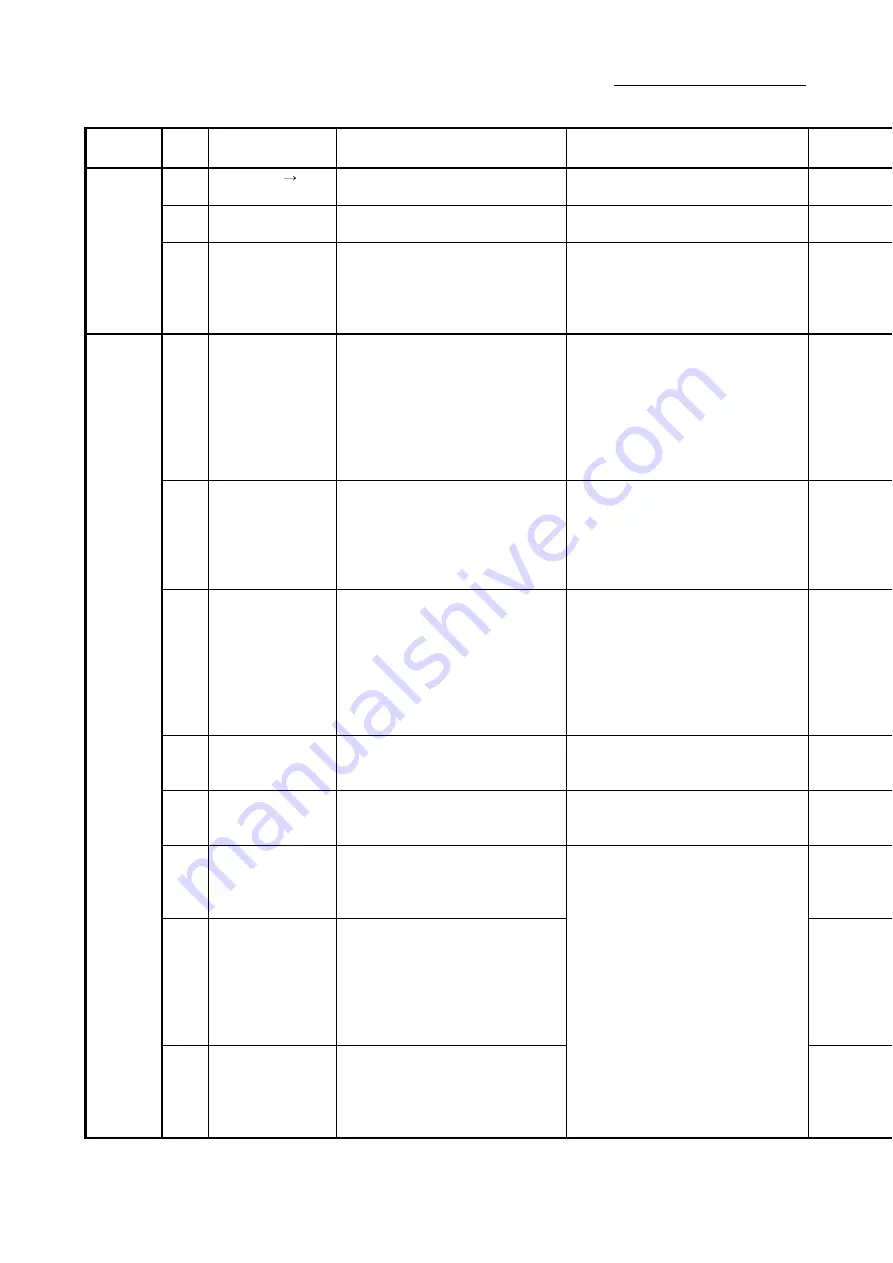
16 - 14
Chapter 16 Troubleshooting
Classification
of errors
Error
code
Error name
Error
Operation status at error occurrence
Common
errors
107
READY OFF
ON
during BUSY
The PLC READY signal is turned from OFF
to ON when BUSY signal is turned ON.
The READY signal [X0] is not turned ON.
108 Start not possible
Start is requested when start is not
possible in the axis operation state.
The system does not start positioning.
190
Operation cycle time
over error
The calculation process time of the
positioning etc. exceeds the operation
cycle.
The operation continues.
Note that the communication might not be
executed if the operation cycle is exceeded
excessively.
Home
position
return (HPR)
201 Start at HP
• When the HPR retry invalid is set, the
proximity dog method machine HPR is
started with the HPR complete flag turned
ON.
• Scale origin signal detection method
machine HPR is started with the HPR
complete flag turned ON and the
proximity dog signal turned ON.
The machine HPR does not start.
203
Dog detection timing
fault
The proximity dog signal is turned OFF
during the deceleration from an HPR speed
to a creep speed by the proximity dog
method machine HPR.
The system stops with the setting
(deceleration stop/rapid stop) of the detailed
parameter 2 rapid stop selection (stop group
3).
(Note that the deceleration stop only occurs
during the manual pulse generator operation.)
206
Count method
movement amount fault
In the count method 1) and 2) machine
HPR, a parameter "Setting for the
movement amount after proximity dog ON"
is smaller than a distance necessary for
deceleration stop from an HPR speed.
At start
: The system does not
operate.
During operation : The system stops with the
setting (deceleration
stop/rapid stop) of the
detailed parameter 2 rapid
stop selection (stop group
3).
207 HPR request ON
The HPR request flag is turned ON when a
fast-HPR is started (positioning start No.
9002).
The fast-HPR does not start.
209
HPR restart not
possible
The restart command is turned ON after
the machine HPR is stopped using a stop
signal.
The restart is not carried out.
210
HPR zero point not
passed
The zero point is not passed when the dog
method, count method or scale origin
signal detection method HPR is re-started,
or data set method HPR is executed.
The HPR does not complete.
211 ZCT read error
The data is not loaded from the servo
amplifier properly upon the HPR.
212
ABS reference point
read error
• The data is not loaded from the servo
amplifier properly upon the HPR.
• The in-position signal is not turned ON
within 1.5 seconds after moving an axis to
the HP.
Содержание MELSEC Q Series
Страница 1: ...MELSEC Q QD77GF Simple Motion Module User s Manual Positioning Control QD77GF4 QD77GF8 QD77GF16 ...
Страница 2: ......
Страница 30: ...A 28 MEMO ...
Страница 32: ...MEMO ...
Страница 97: ...3 29 Chapter 3 Specifications and Functions MEMO ...
Страница 102: ...3 34 Chapter 3 Specifications and Functions MEMO ...
Страница 282: ...5 162 Chapter 5 Data Used for Positioning Control MEMO ...
Страница 374: ...7 16 Chapter 7 Memory Configuration and Data Process MEMO ...
Страница 376: ...MEMO ...
Страница 400: ...8 24 Chapter 8 HPR Control MEMO ...
Страница 425: ...9 25 Chapter 9 Major Positioning Control MEMO ...
Страница 528: ...9 128 Chapter 9 Major Positioning Control MEMO ...
Страница 554: ...10 26 Chapter 10 High Level Positioning Control MEMO ...
Страница 586: ...11 32 Chapter 11 Manual Control MEMO ...
Страница 800: ...16 54 Chapter 16 Troubleshooting MEMO ...
Страница 829: ...Appendix 29 Appendices 3 QD77GF16 Unit mm inch 115 4 53 3 0 12 23 0 91 27 4 1 08 98 3 86 4 0 16 ...
Страница 830: ...Appendix 30 Appendices MEMO ...
Страница 833: ......