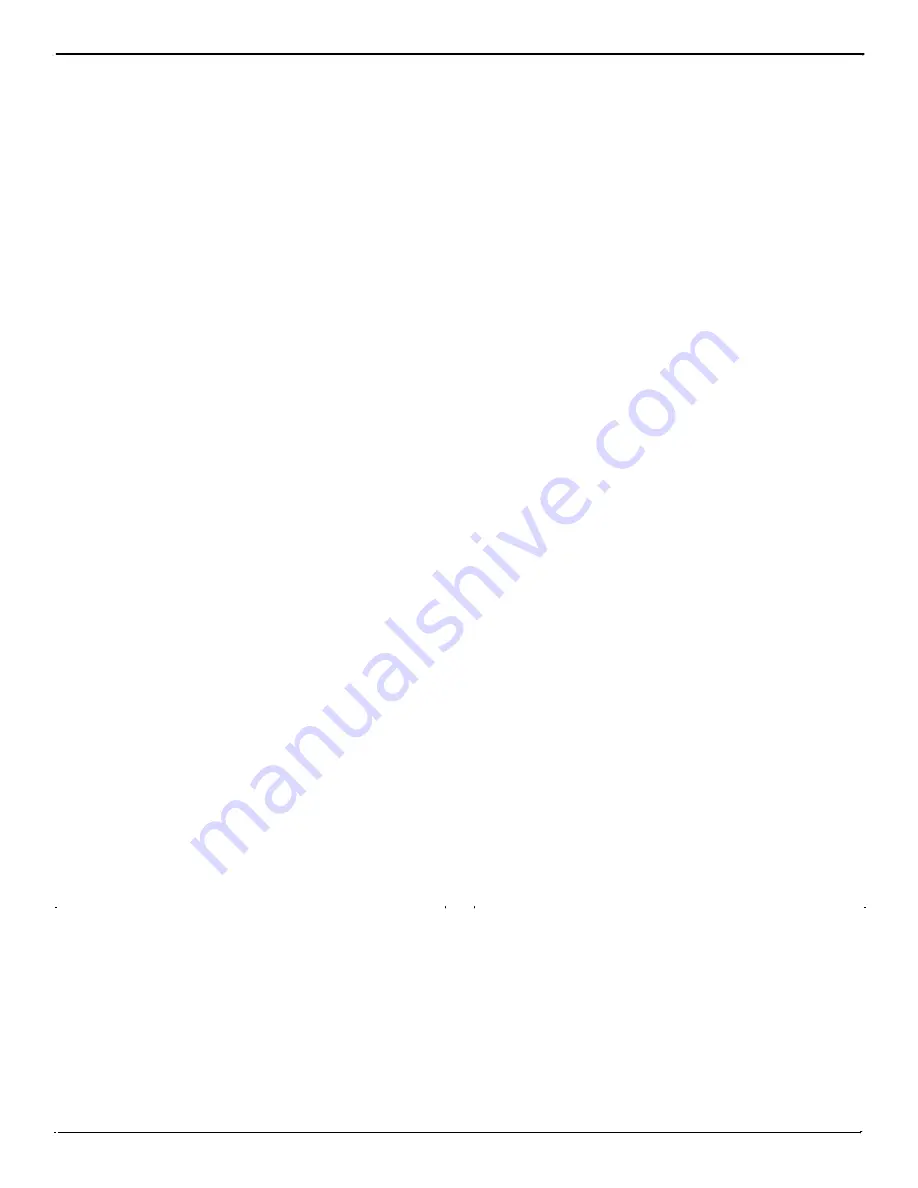
ENGAGING SPRINGS
If clutch pressure plate shows signs of overheating, it is
likely that the engaging springs will require replacement.
Inner and outer springs should be checked for tension at
each overhaul using the Valve Spring Tester Tool KMO-
607 and checking against the tension data as follows:
Inner all © 1-5/8" -- 75 to 85 lbs.
Outer all © 1-5/8" -- 130 to 140 lbs.
THROWOUT FINGERS
Visually check the fingers for wear and uneven surfaces
at the points where the fingers contact the throwout bearing
and retainers, also check the retaining pin bores. Replace
fingers that show noticeable wear.
RETAINERS AND WASHERS
Check retainers for wear at slot where they contact the
lobed surface of the fingers. The bearing surface on the
retainers is practically a line contact. If bearing area of
retainer is grooved deeper than .005" replace the retainer. If,
however, there is only one such groove, the retainer may be
safely continued in service by rotating it 180 degrees from
former position when it is being Installed. Changing the
retainer position by half a turn will bring unworn portion
into contact with finger fulcrum lobe.
NOTE: The plain copper washers interposed between
retainers and cover function as oil seals. Top and bottom
faces of these washers must be flat and free of scores,
otherwise they should be replaced.
CLUTCH COVER
Inner surface of cover must be flat and free from scores
adjacent to the holes for the finger retainers. Cover must be
flat within .005" when front face is checked on a surface
plate.
Distance from front face of cover where it contacts the
flywheel gasket, to points on front wall of cover where
retainer sealing washers fit (B) Figure 6, should not be less
than 2.350" and not more than 2.370" measured 1/8" from
edge of each of the 3-finger retainer holes.
Variation in distance at any of, the 3 holes should not
exceed .008". Covers that are not within these limits should
be replaced unless equipment and skill is available for doing
an accurate job of straightening.
Cover hub bore (C) against which the throwout collar oil
seal contacts, must be smooth and free from nicks and burrs.
If cover hub bore (C) shows considerable wear and
scoring, it is an almost certain indication of misalignment.
Whenever this condition is encountered, b e sure to thor-
oughly check the engine rear support plate, flywheel and
clutch bell housing, for shaft concentricity and face align-
ment in both planes.
THROWOUT BEARING AND SEALS
In the removal of clutch from engine, the throw out
bearing (13), Figure 1, grease retainer (17) and clutch oil seal
(14) will be removed as a single unit with the collar (12).
Leather element of seal must be free of glaze and cuts or
cracks and must be firmly attached to the stamped steel
element. Leather must not rotate in relation to the stamping
and the seal assembly must be stationary on the clutch
collar. Check to see that coil spring is intact and not loose.
Replacement of the oil seal necessitates removal of the
throwout bearing from the clutch collar. Use care when
pressing new seal onto collar, apply a steady pressure to the
(INNER) metal edge. As the seal assembly can be quickly
made ineffective by careless Installation, it is important to
use a close fitting pressing sleeve so as to confine all the load
to the inner edge.
The throwout bearing should be free from roughness or
lumpiness when rotated after cleaning and oiling, otherwise
it should be replaced. If both the throwout bearing and the
oil seal require replacement, it is usually as economical to
Install a new collar assembly.
When Installing throwout bearing to collar, do so with a
press having a ram adaptor large enough to cover the entire
front face of the bearing. DO NOT drive the bearing into
place on the collar as such action is likely to mark or brinnel
the races causing subsequent noise in operation.
CLUTCH 7 - 7
Содержание 1948 - 1952
Страница 1: ...HUDSON SHOP SERVICE MANUAL 1 9 4 8 1 9 5 2...
Страница 2: ...This manual courtesy of Hudson Essex Terraplane Club member Drew Meyer...
Страница 10: ...VIII...
Страница 12: ...1 2 LUBRICATION FIGURE 1...
Страница 13: ...LUBRICATION 1 3...
Страница 14: ...1 4 LUBRICATION...
Страница 46: ...3 4 ENGINE FIGURE 1...
Страница 52: ...3 10 ENGINE FIGURE 8...
Страница 70: ...3 28 ENGINE FIGURE 32...
Страница 71: ...ENGINE 3 29 FIGURE 33...
Страница 76: ...3 34 ENGINE FIGURE 40...
Страница 78: ...3 36 ENGINE FIGURE 41...
Страница 81: ...ENGINE 3 39 FIGURE 44...
Страница 117: ...FUEL SYSTEM EXHAUST 4 33 FIGURE 105 COPYRIGHT 1949 BY CARTER CARBURETOR CORPORATION ALL RIGHTS RESERVED...
Страница 119: ...FUEL SYSTEM EXHAUST 4 35 FIGURE 106...
Страница 148: ...6 12 ELECTRICAL SYSTEM FIGURE 10...
Страница 149: ...ELECTRICAL SYSTEM 6 13...
Страница 152: ...6 16 ELECTRICAL SYSTEM FIGURE 12...
Страница 180: ...8 2 TRANSMISSION FIGURE 1...
Страница 198: ...8 20 TRANSMISSION FIGURE 10...
Страница 209: ...OVERDRIVE 9 1...
Страница 215: ...OVERDRIVE 9 7 FIGURE 10...
Страница 238: ...9 30 OVERDRIVE REFERENCE Source of Information Date Subject...
Страница 260: ...11 18 REAR AXLE FIGURE 25...
Страница 286: ...12 18 FRONT SUSPENSION REFERENCE Source of Information Date Subject...
Страница 306: ...14 8 SPRINGS SHOCK ABSORBERS STABILIZERS REFERENCE Source of Information Date Subject...
Страница 322: ...15 16 BRAKES REFERENCE Source of Information Date Subject...
Страница 330: ...REFERENCE Source of Information Date Subject...
Страница 331: ......
Страница 332: ......
Страница 333: ......