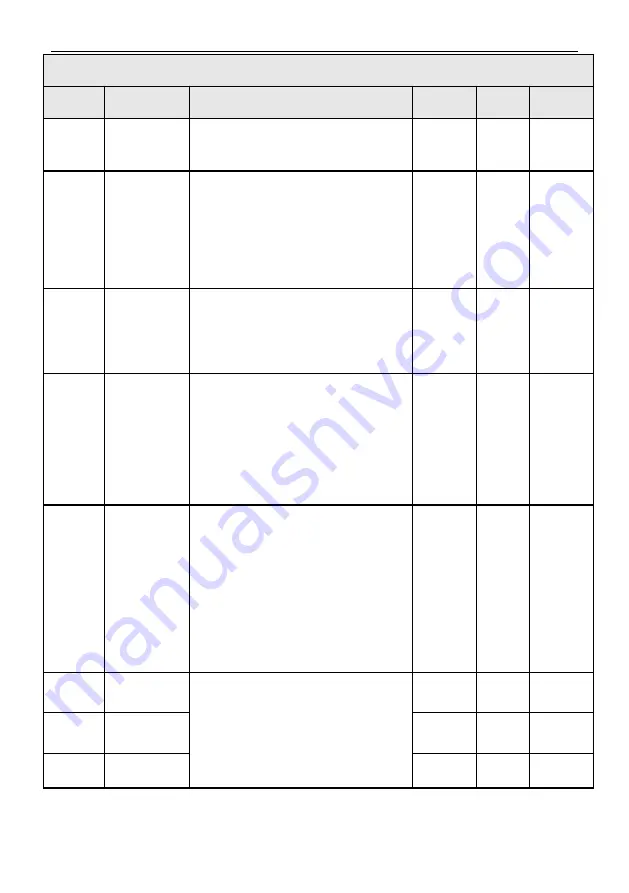
HV100 Series High Performance Current Vector Inverter
40
008group-PID Control Parameter
Function
code
Name
Content
Setting
range
Factory
Alteration
08.00
PID operation
mode
0: Automatic
1: Manually operation through the defined multi-function
terminal
0
~
1
0
×
08.01
PID setting
channel selection
0: Digital given
1: AI1
2: AI2
3: Pulse given
4: RS485 communication
5: Pressure given
(
MPa
、
Kg
)
6: Potentiometer given
0
~
6
0
○
08.02
Set by digital
quantity
When using analog feedback, this function code realizes
setting the given quantity of closed-loop control with the
keypad, and this function is effective only when the
digital given channel of closed-loop is selected (08.01 is
0).
0.0
~
100.0
%
50.0%
○
08.03
PID feedback
channel selection
0: AI1
1: AI2
2: AI1+AI2
3: AI1-AI2
4: MAX
{
AI1
,
AI2
}
5: MIN
{
AI1
,
AI2
}
6: Pressure given
7: RS485 communication
0
~
7
0
○
08.04
Advanced
characteristic
setting of PID
controller
LED single digit:PID polarity selection
0: Positive 1: Negative
LED10 digit:
)
Scaling characteristics
0: Constant proportional integral regulation
1: Automatic proportional intergral regulation
LED100 digit: Integral regulation characteristic
0: when the frequency reaches the upper and lower
limit,stop the integral adjustments
1: when the frequency reaches the upper and lower
limit,continue the integral adjustments
LED1000 digit: Reserved
000
~
111
000
×
08.05
Proportional gain
KP1
The speed of PID adjustment is set by two parameters:
proportional gain and integration time. For fast
adjustment, it is necessary to increase proportional gain
and reduce integration time; for slow adjustment, it is
necessary to reduce proportional gain and increase
integration time. Under normal circumstances, the
differential time is not set; 0.0: no differentiation.
0.01
~
100.00
2.50
○
08.06
Integration time
Ti1
0.01
~
10.00s
0.10
○
08.07
Differential time
Td1
0.01
~
10.00s
0.00
○