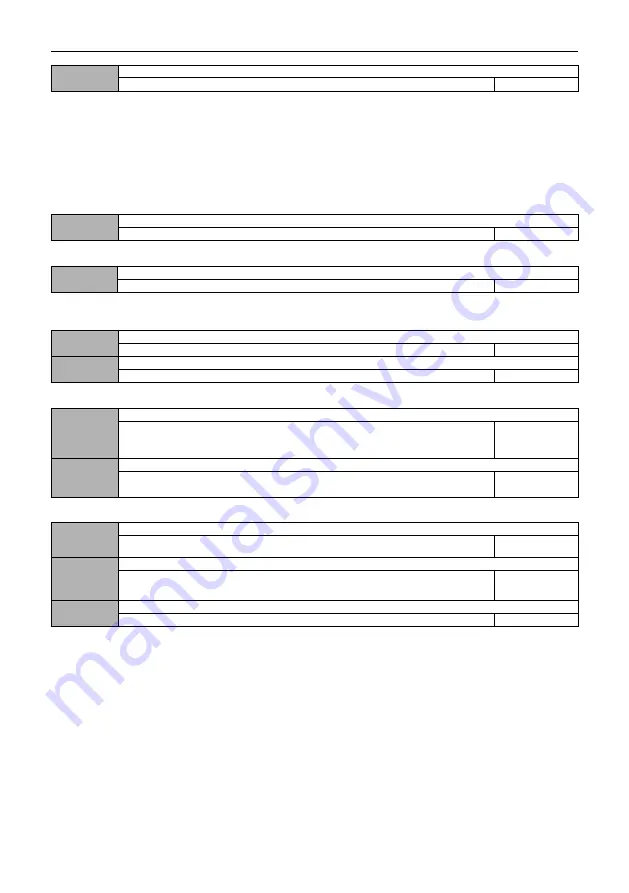
HV100 Series High Performance Current Vector Inverter
73
04.15
Speed limit channel selection 2 of torque control mode (reverse direction)
0
~
2
0
This function code sets the reverse speed limit channel during torque control.
0
:
Keypad digit given 2
See 04.17 Settings for details.
1
:
AI1
The reverse speed limit channel for torque control is given by AI1. Please refer to the description of function code
06.00 ~ 06.05.
2
:
AI2
The reverse speed limit channel for torque control is given by AI2. Please refer to the description of function code
06.06 ~ 06.11.
04.16
Keyboard numbers limit speed 1
0.0 ~ 100.0% * [00.12] maximum frequency
100.0%
Keyboard numerals limit speed 1 to a limit relative to the maximum output frequency. This function code corresponds
to the limit value of forward speed when 04.14=0.
04.17
Keyboard digital limit speed 2
0.0 ~ 100.0% * [00.12] maximum frequency
100.0%
Keyboard digital limit speed 2 to a limit relative to the maximum output frequency. This function code corresponds to
the limit value of reverse speed when 04.15=0.
04.18
Torque rise time
0.0S
~
10.0S
0.1
04.19
Torque fall time
0.0S
~
10.0S
0.1
Torque rise/fall time defines the time when the torque rises from 0 to the maximum value or falls from the maximum
value to 0.
04.20
Electric torque limitation in vector mode
G type: 0.0% ~ 200.0% * motor rated current 180.0%
P type
:
0.0% ~ 200.0% * rated current of motor 120.0%
Model setting
04.21
Brake torque limitation in vector mode
G type: 0.0% ~ 200.0% * rated current of motor 180.0% P type: 0.0% ~ 200.0% *
rated current of motor 120.0%
Model setting
The above function code defines the magnitude of torque limit value when vector control is performed
04.22
Torque detection action selection
0
~
8
0
04.23
Torque detection level
G type: 0.0% ~ 200.0% * rated current of motor 150.0% P type: 0.0% ~ 200.0% *
rated current of motor 110.0%
Model setting
04.24
Torque detection time
0.0
~
10.0S
0.0
When the actual torque is within 04.24 (torque detection time) and continuously exceeds 04.23 (torque check level),
the inverter will make corresponding actions according to the setting of 04.22. When the set value of torque detection level
is 100%, it corresponds to the rated torque of the motor.
0: Detection invalid
Torque detection is not performed.
1: Continue to run after detecting torque at constant speed
Over-torque is detected only in the constant speed operation process, and after the torque is detected, the inverter
continues to run.
2: Continue to run after detecting torque during operation
After the torque is detected in the whole operation process, the inverter continues to run.
3: Cut off the output after the torque is detected at constant speed
Over-torque is detected only in the constant speed operation process, and after the torque is detected, the inverter
stops output, and the motor slides to stop freely.
4: Cut off the output after detecting torque in operation
After the torque is detected in the whole running process, the inverter stops outputting and the motor slides and stops
freely.