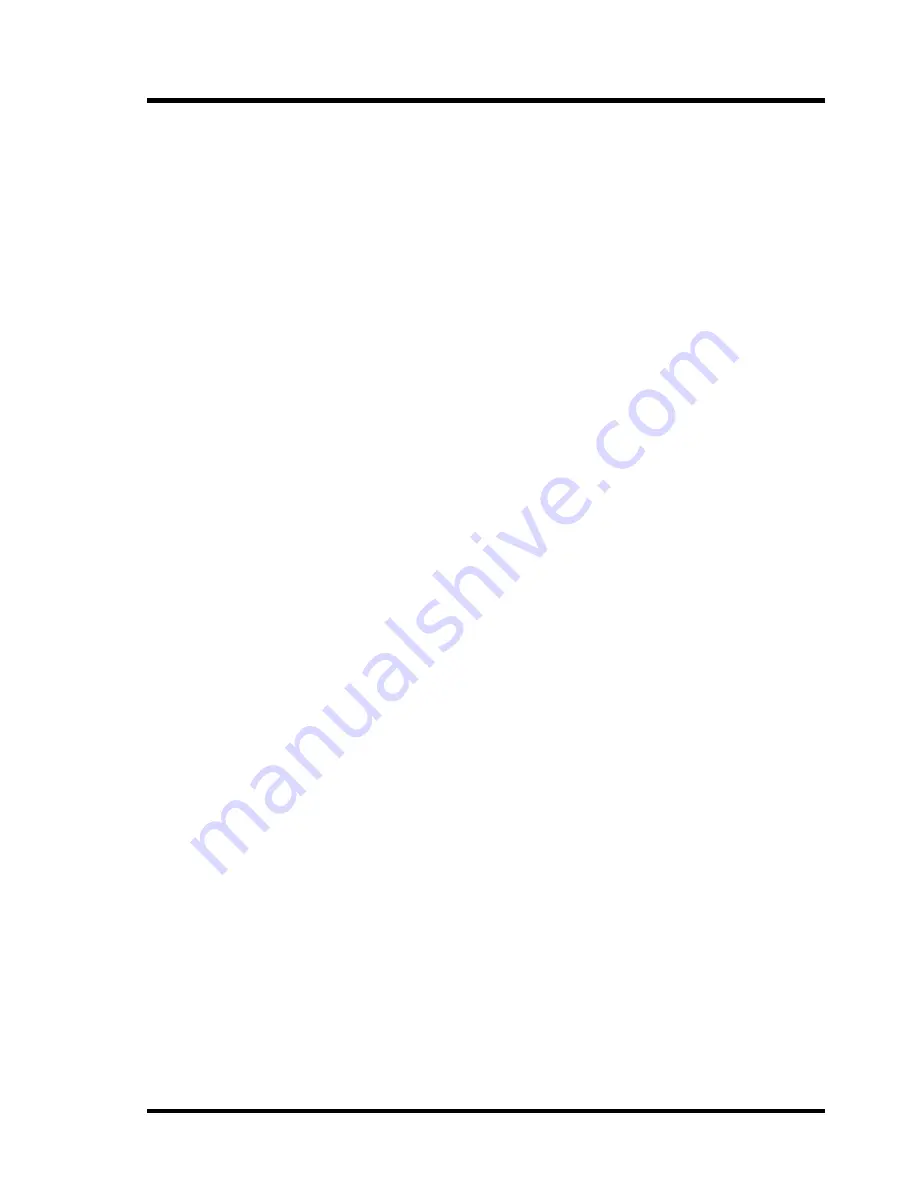
v
5.2 Adjusting the Scale Factor and the Zero Position
184
5.2.1
Adjusting the Scale Factor
184
5.2.2
Zero Position Adjustment Description
185
5.2.3
Adjusting the Zero Position
190
6.
Troubleshooting
192
6.1 Self-test
192
6.2 LED Fault Conditions
193
6.3 System Event List Messages
194
6.4 Alarm Event List Messages
205
7.
Ordering Information
206
8.
Specifications
209
Artisan Technology Group - Quality Instrumentation ... Guaranteed | (888) 88-SOURCE | www.artisantg.com