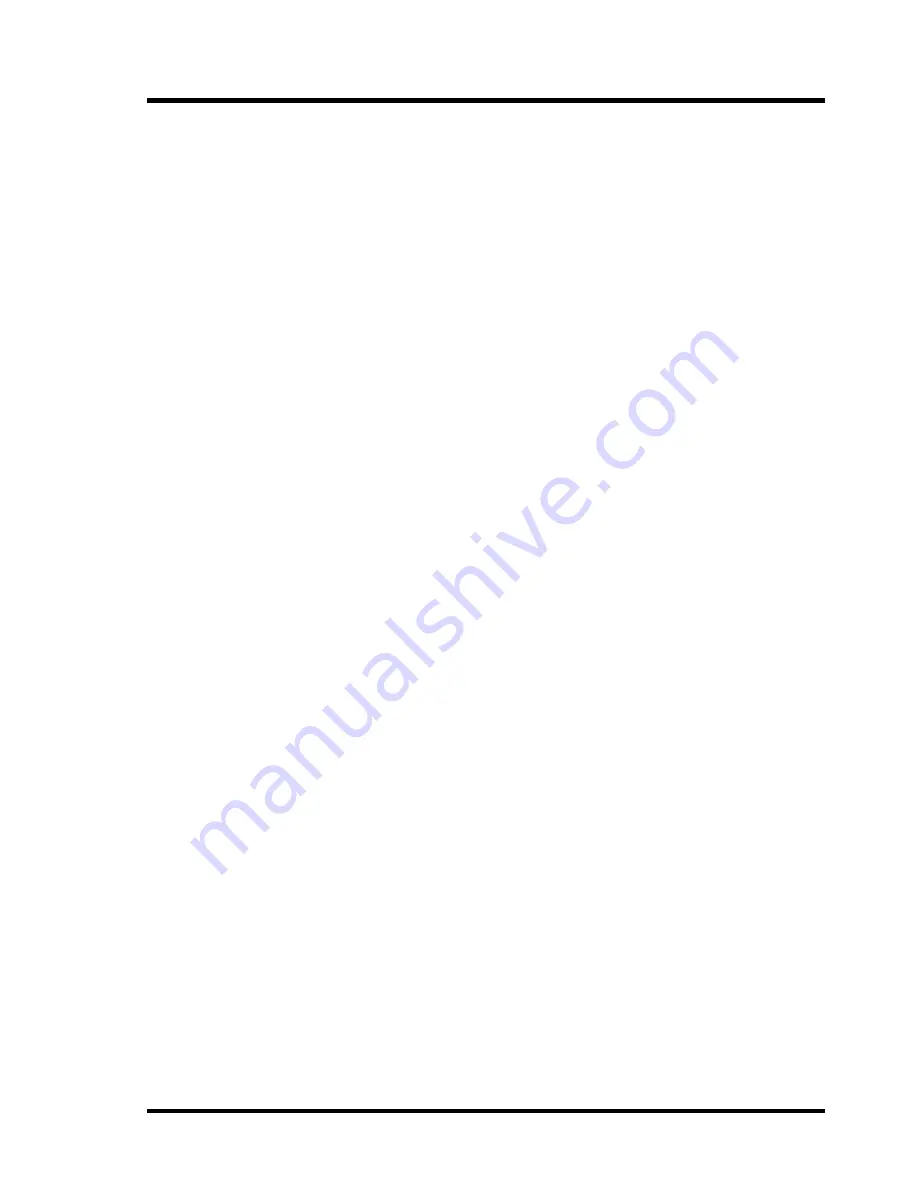
3500/42 Operation and Maintenance
Maintenance
129
Value field has no alarm indication.
5. Adjust the power supply voltage such that the signal just exceeds the Gap
Over Alert/Alarm 1 setpoint level. Wait for 2 or 3 seconds until the alarm time
delay expires and verify that the bar graph indicator for Gap changes color
from green to yellow and that the Current Value Field indicates an Alarm.
6. Press the RESET switch on the Rack Interface Module (RIM). Verify that the
bar graph indicator for Gap remains yellow and that the Current Field still
indicates an Alarm.
7. Adjust the power supply such that the signal just exceeds the Gap Over
Danger/Alarm 2 setpoint level. Wait for 2 or 3 seconds after the alarm time
delay expires and verify that the bar graph indicator for Gap changes color
from yellow to red and that the Current Value Field indicates an Alarm.
8. Press the RESET switch on the Rack Interface Module (RIM). Verify that the
bar graph indicator for Gap remains red and that the Current Value Field still
indicates an Alarm.
9. Adjust the power supply voltage such that the signal reads below the Over
Alarm setpoint levels. If the nonlatching option is configured, observe that
the bar graph indicator for Gap changes color to green and that the Current
Value Box contains no indication of alarms. Press the RESET switch on the
Rack Interface Module (RIM) to reset latching alarms.
10. Repeat steps 5 through 9 to test the Under Alert/Alarm 1 and Under
Danger/Alarm 2 setpoints by adjusting the power supply to exceed the Under
Alarm setpoint levels.
11. If you can not verify any configured alarm, recheck the configured setpoints.
If the monitor still does not alarm properly or fails any other part of this test,
go to Section 5.1.11 (If a Channel Fails a Verification Test).
12. Disconnect the test equipment and reconnect the PWR, COM, and SIG field
wiring to the channel terminals on the I/O module. Verify that the OK LED
comes on and the OK relay energizes. Press the RESET switch on the Rack
Interface Module (RIM) to reset the OK LED.
13. Repeat steps 1 through 12 for all configured channels.
5.1.6.3
Verify Channel Values - Thrust Position and Differential Expansion
The general approach for testing these parameters is to simulate the Thrust
Position and Differential Expansion signal with a power supply. The output
values are verified by varying the input DC voltage and observing that the correct
results are reported in the Verification screen on the test computer.
Direct
1. Disconnect PWR, COM, and SIG field wiring from the channel terminals on
the I/O module.
Artisan Technology Group - Quality Instrumentation ... Guaranteed | (888) 88-SOURCE | www.artisantg.com