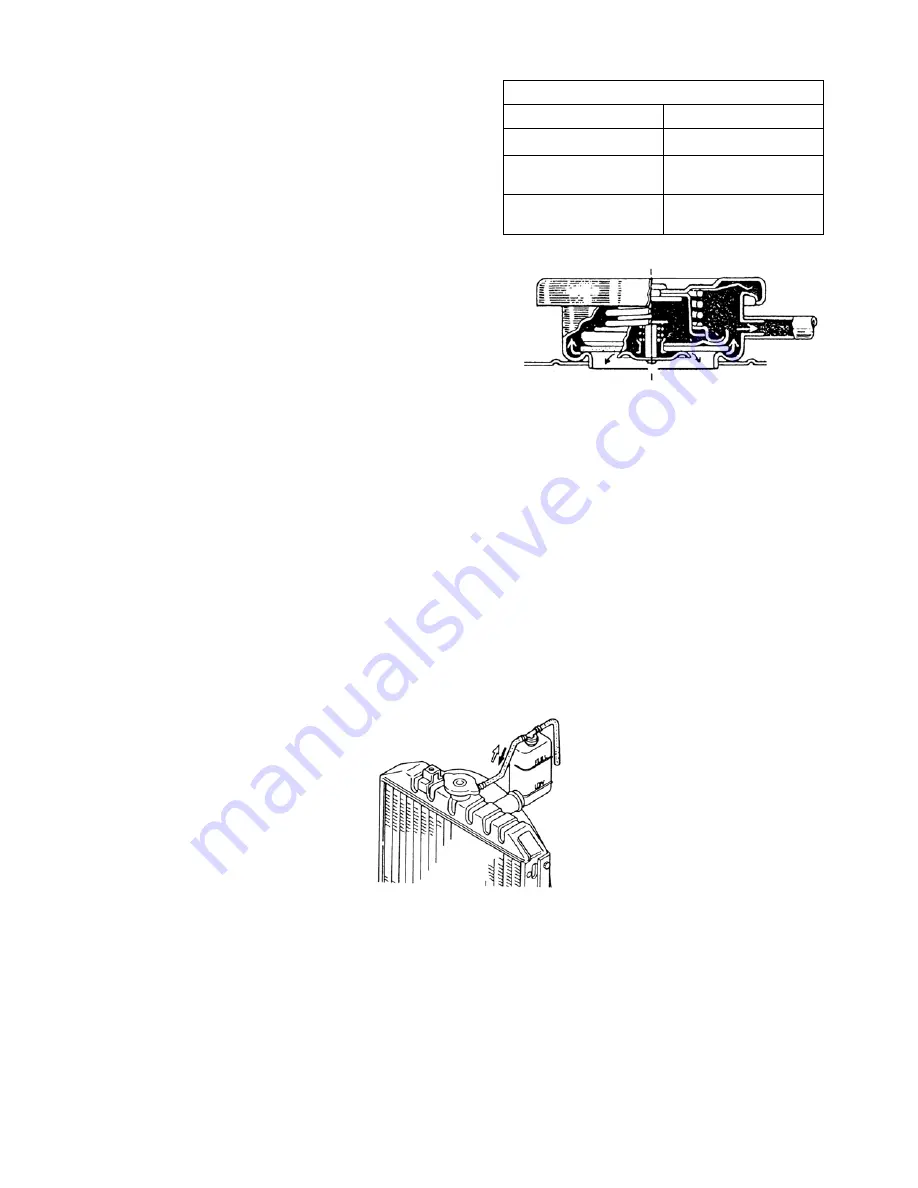
47
17) Radiator
Specifications and structure
Structure
(1) The radiator is provided with the plate fin having
superior anti-vibration characteristics.
(2) The radiator cap is of the pressure type (sealing type)
for higher cooling efficiency.
When the cooling water is heated to high temperature
(high pressure), the pressure valve is pushed and
opened to release excessive pressure from the overflow
pipe (shown by white arrow mark).
When the cooling water temperature reduces and the
inside pressure becomes lower than the atmospheric
pressure, the negative pressure valve is opened to
protect the radiator from being crushed under the
atmospheric pressure (shown by black arrow mark).
144Y
Inspection
a.
Check the radiator, pipe, and reserve tank for water leakage and repair or correct if any.
b.
Check the radiator fin and remove dust, mud, or other foreign matter clogging in the air passage, if any,
c.
Check the pressure valve and negative pressure valve of the radiator cap for valve opening pressure and sealing condition.
Replace if defective.
d.
Check the radiator hose and replace if damaged or aged.
e.
If the net is clogged, remove and clean.
f.
The cooling water level in the reserve tank should be always between FULL and LOW.
145Y
Specifications
Fin type
Corrugated
Cooling water volume
5.0
ℓ
Pressure valve starting
pressure
73.5 – 103 kPa
{0.75 – 1.05 kgf/cm
2
}
Negative pressure valve
starting pressure
– 4.9 kPa
{0.04 – 0.05 kgf/cm
2
}
Summary of Contents for ST330
Page 5: ...1 Chapter 1 GENERAL...
Page 29: ...24 2 1 Engine Sectional View 100Y 101Y...
Page 74: ...64 Chapter 3 TRACTOR MAIN BODY...
Page 96: ...86 1 SECTIONAL VIEW 360Y 3 4 Transmission 1 for HST...
Page 98: ...88 2 HST unit 362Y...
Page 127: ...117 2 Two Speed PTO Model 403Y 9 3 Transmission Without one way clutch 2 Speed PTO...
Page 197: ...186 2 COMPONENT LOCATION 517Y...
Page 245: ...233 4 WIRING 518aY...
Page 246: ...234 518bY...