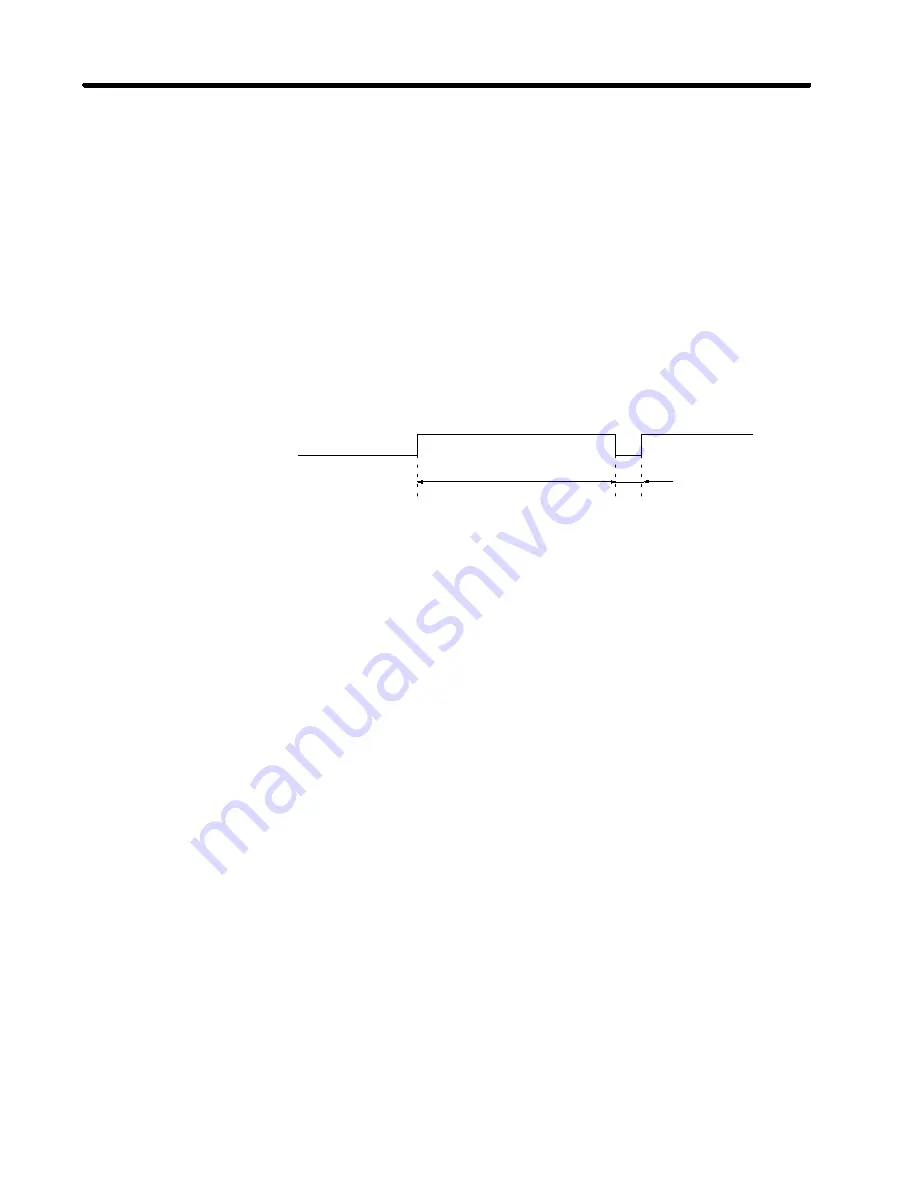
2-65
D
+ Deviation Counter Reset (15: +ECRST)
-- Deviation Counter Reset (14: --ECRST)
The content of the deviation counter will be reset when the deviation counter reset signal turns ON and
the position loop will be disabled. Pn200.1 (position control setting 1: deviation counter reset) can be
used to set either a status signal (high or low) or a differential signal (low to high or high to low). Input the
reset signal for 20
µ
s minimum. The counter will not be reset if the signal is too short.
D
Sensor ON Input (4: SEN)
Sensor ON Input Ground (2: SENGND)
SEN signal ON, OFF, and ON again.
When the SEN signal turns ON (low to high), the absolute encoder’s multi-turn amount and the initial
incremental pulses are sent. When the SEN signal is OFF, power cannot be supplied to the Servomotor
even if a RUN command is input. The RUN command will not be enabled until the SEN signal turns ON
and the encoder achieves normal operation. Do not turn ON the SEN signal for at least 3 s after turning
on the power supply. Refer to the following diagram for turning the SEN signal ON, OFF, and ON again.
SEN signal
1.3 s min.
15 ms min.
D
Backup B Input (21: BAT)
Backup Battery -- Input (22: BATGND)
These are the connection terminals for a backup battery for when power to the absolute encoder is inter-
rupted. Normally a Backup Battery Unit is used and the battery is connected to CN8 (Battery Connec-
tor), so in that case do not connect anything to these terminals. The battery voltage is 2.8 to 4.5 V.
D
RUN Command Input (40: RUN)
This is the input that turns ON the power drive circuit for the main circuit of the Servo Driver. If this signal
is not input (i.e., servo-OFF status), the Servomotor cannot operate except for JOG operations.
Note
This is the default allocation. Input terminal allocations (CN1 pins 40 to 46) can be changed by
setting Pn50A.0 (input signal selection mode) to 1. The RUN signal is allocated by Pn50A.1.
D
Gain Reduction Input (41: MING)
This signal is enabled for position control, speed control, and internally-set control. When it is input,
speed loop control is changed from PI to P control. Use it when it is necessary to weaken servo rigidity
(repellant force with respect to external force). If position control is executed without including a position
loop, there may be some position deviation due to temperature drift from a device such as the A/D con-
verter. If a gain reduction is input in such a case, the loop gain of the speed loop will be lowered and the
amount of drift will be decreased. If there is static friction torque on the load (5% or more of the rated
torque), the Servomotor can be completely stopped.
If a position loop is included, when parts are inserted after positioning, the insertion operation is made
easier because the repellant force with respect to external force is weakened by the inputting of this
signal. This cannot be used for a vertical shaft where a gravity load is applied, or for applications where
constant external force is applied, because position deviation will occur.
Note 1.
This is the default allocation. Input terminal allocations (CN1 pins 40 to 46) can be changed by
setting Pn50A.0 (input signal selection mode) to 1. The MING signal is allocated by Pn50A.2.
Standard Models and Specifications
Chapter 2
AUDIN - 7 bis rue de Tinqueux - 51100 Reims - France - Tel : 03.26.04.20.21 - Fax : 03.26.04.28.20 - Web : http: www.audin.fr - Email : [email protected]