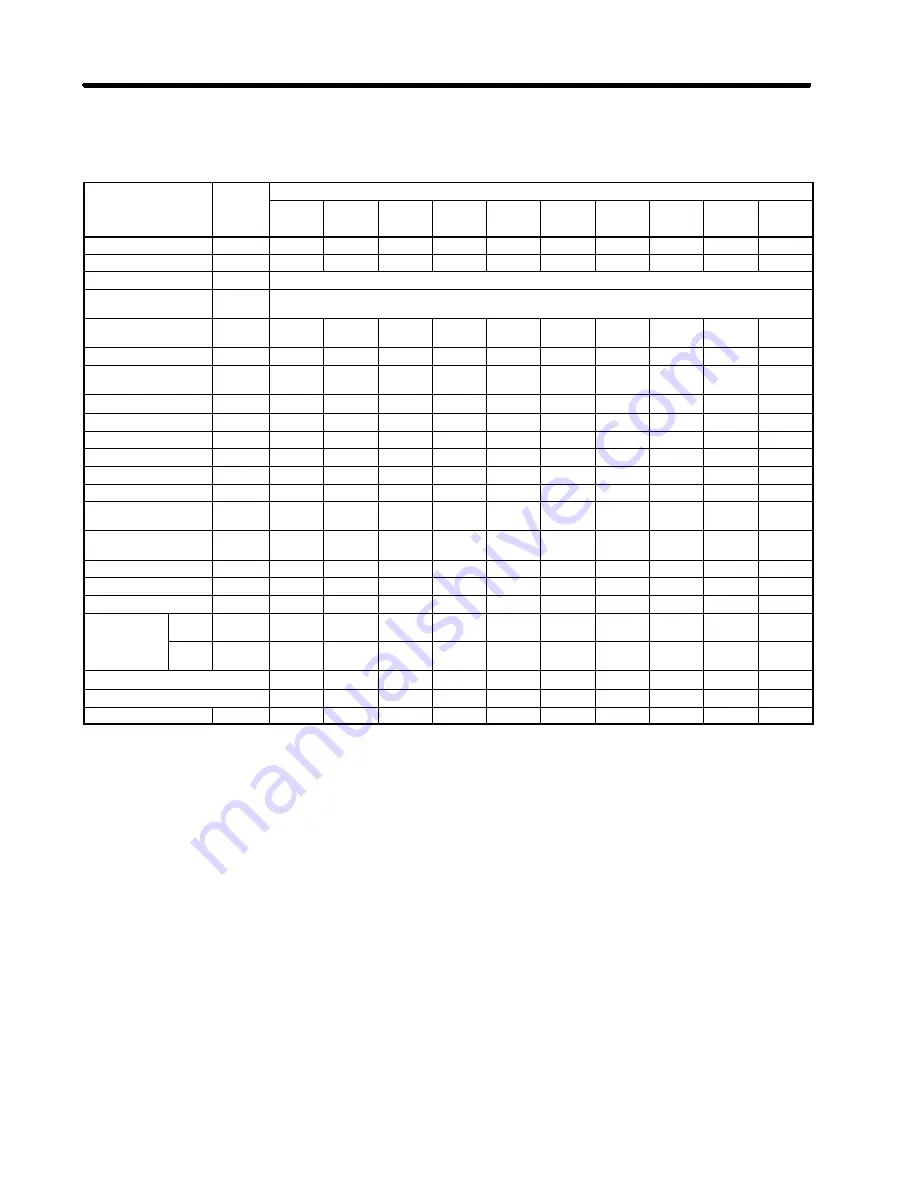
2-80
H
1,500-r/min Servomotors
D
Performance Specifications Table
Item
Unit
400 V AC
e
U
R88M-
W45015F
R88M-
W85015F
R88M-
W1K315F
R88M-
W1K815F
R88M-
W2K915F
R88M-
W4K415F
(C)
R88M-
W5K515F
(C)
R88M-
W7K515F
(C)
R88M-
W11K015F
(C)
R88M-
W15K015F
(C)
Rated output*
KW
0.45
0.85
1.3
1.8
2.9
4.4
5.5
7.5
11
15
Rated torque*
Nm
2.84
5.39
8.34
11.5
18.6
28.4
35.0
48.0
70.0
95.4
Rated rotation speed
r/min
1500
Momentary maximum
speed
r/min
3000
Momentary maximum
torque*
Nm
8.92
13.8
23.3
26.7
45.1
71.1
90.7
123.0
175.0
221.0
Rated current*
A (rms)
1.9
3.5
5.4
8.4
11.9
16.5
20.8
25.4
28.1
37.2
Momentary maximum
current*
A (rms)
5.5
8.5
14
20
28
40.5
55
65
70
85
Rotor inertia
kgm
2
7.24
×
10
--4
13.9
×
10
--4
20.5
×
10
--4
31.7
×
10
--4
46.0
×
10
--4
67.5
×
10
--4
89
×
10
--4
125
×
10
--5
281
×
10
--6
315
×
10
--7
Torque constant*
Nm/A
1.64
1.65
1.68
1.46
1.66
1.82
1.74
2.0
2.56
2.64
Power rate*
kW/s
11.2
20.9
33.8
41.5
75.3
120
137
184
174
289
Mechanical time constant
ms
5.6
3.1
2.9
2.4
2
1.4
1.4
1.1
1.1
1.0
Built-in resistor resistance
Ω
108
108
108
45
45
32
18
18
14.3
14.3
Built-in resistor capacity
W
70
70
70
140
140
180
880
880
1760
1760
Minimum allowable
resistance
Ω
73
73
73
44
44
28
18
14.2
14.2
14.2
Regenerative power pro-
cessed by built-in resistor
W
14
14
14
28
28
180
880
880
1760
1760
Electrical time constant
ms
4.5
5.3
6.1
11.1
12.3
15.2
14.4
17.6
22.9
26.2
Allowable radial load
N
490
490
686
1176
1470
1470
1764
1764
1764
4998
Allowable thrust load
N
98
98
343
490
490
490
588
588
588
2156
Weight
Without
brake
kg
5.5
7.6
9.6
14
18
23
30
40
57.5
86
With
brake
kg
7.5
9.6
12
19
23.5
28.5
35.0
45.5
65
100
Applicable load inertia
5
×
5
×
5
×
5
×
5
×
5
×
5
×
5
×
5
×
5
×
Applicable Servo Driver (R88D-)
WT05HF
WT10HF
WT15HF WT20HF
WT30HF WT50HF
WT60HF
WT75HF WT110HF WT150HF
Brake inertia
kgm
2
x 10
4
2.1
2.1
2.1
8.5
8.5
8.5
8.5
8.5
18.8
37.5
Standard Models and Specifications
Chapter 2
AUDIN - 7 bis rue de Tinqueux - 51100 Reims - France - Tel : 03.26.04.20.21 - Fax : 03.26.04.28.20 - Web : http: www.audin.fr - Email : [email protected]