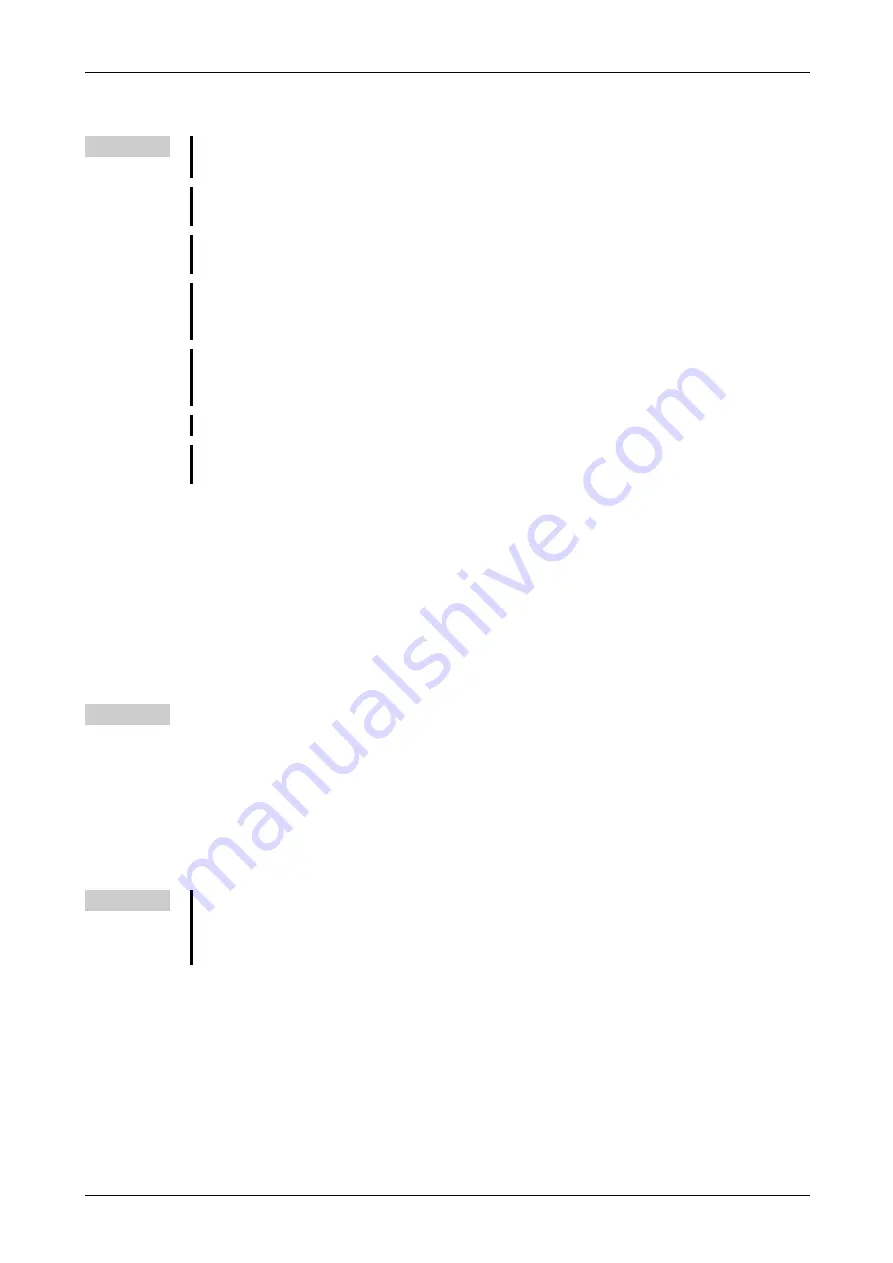
Parameters
(A) Application parameters
FR-A800
5 - 537
Servo rigidity adjustment (Pr. 362, Pr. 396 to Pr. 398) (Vector control)
To increase the servo rigidity
during orientation stop using Pr. 396 "Orientation speed gain (P term)"
or Pr. 397 "Orientation speed integral time", adjust with the following procedures.
Increase the Pr. 362 "Orientation position loop gain" value to the extent that rocking does not
occur during orientation stop.
Increase Pr. 396 and Pr. 397 at the same rate.
Normally, adjust Pr. 396 in the range from 10 to 100, and Pr. 397 from 0.1 to 1.0 s.
(Note that these do not need to be set to the same rate.)
Pr. 398 "Orientation speed gain (D term)" is the lag/advance compensation gain.
The limit cycle
can be prevented by increasing the value, and operation can be stopped stably.
However, the torque will decrease in relation to the position deviation, and the motor will stop
with deviation.
Servo rigidity: This is the response when a position control loop is configured.
When the servo rigidity is raised, the holding force will increase and operation will stabilize, but
vibration will more easily occur.
When the servo rigidity is lowered, the holding force will decrease, and the settling time will
increase.
Limit cycle: This is a phenomenon that generates ± continuous vibration centering on the target
position.
Rocking: Movement in which return occurs when the stopping position is exceeded.
NOTES
Couple the encoder with the motor shaft that stops the shaft at the specified position. Couple it
with the speed ratio of 1:1 and without any mechanical looseness.
To ensure correct positioning, the encoder must be set in the proper rotation direction, and the A
and B phases must be connected correctly.
If the pulse signal from the encoder stops due to encoder signal loss, etc. during orientation, orien-
tation may not be completed.
To terminate orientation, the start signal (STF or STR) must be first switched OFF, and then the ori-
entation signal (X22) must be switched OFF. As soon as this orientation signal is switched OFF, ori-
entation control ends.
When performing orientation control, properly set Pr. 350 "Stop position command selection" and
Pr. 360 "16-bit data selection".
If the values set are incorrect, proper orientation control will not be performed.
When orientation control is performed, PID control is disabled.
If Signal loss detection(E.ECT) is displayed when the X22 signal is ON, causing the inverter to trip,
check for a break in the cable of the Z phase of the encoder.
Example
When the Pr. 396 value is multiplied by 1.2, divide the Pr. 397 value by 1.2.
If vibration occurs during orientation stop, the scale cannot be raised any higher.
NOTE
Application of lag/advance control and PI control
PI control can be applied by setting Pr. 398 to 0. Normally, use the lag/advance control. PI control
should be used when using a machine with a high spindle static friction torque and requires a stop
position accuracy.
Summary of Contents for FR-A820-00046 (0.4K)
Page 2: ......
Page 4: ......
Page 144: ...System configuration for Ethernet communication FR A800 E Installation and wiring 2 114 ...
Page 202: ...Basic operation procedure JOG operation Basic operation 4 32 ...
Page 1090: ...Check first when you have a trouble Protective functions 6 50 ...
Page 1189: ...Appendix EC Declarations of Conformity FR A800 A 49 ...
Page 1190: ...EC Declarations of Conformity Appendix A 50 ...
Page 1191: ...Appendix EC Declarations of Conformity FR A800 A 51 ...
Page 1192: ...EC Declarations of Conformity Appendix A 52 ...
Page 1193: ...Appendix EC Declarations of Conformity FR A800 A 53 ...
Page 1194: ...EC Declarations of Conformity Appendix A 54 ...
Page 1195: ...Appendix EC Declarations of Conformity FR A800 A 55 ...
Page 1196: ...EC Declarations of Conformity Appendix A 56 ...
Page 1197: ...Appendix EC Declarations of Conformity FR A800 A 57 ...
Page 1198: ...EC Declarations of Conformity Appendix A 58 ...
Page 1199: ...Appendix EC Declarations of Conformity FR A800 A 59 ...
Page 1200: ...EC Declarations of Conformity Appendix A 60 ...
Page 1201: ...Appendix EC Declarations of Conformity FR A800 A 61 ...
Page 1202: ...EC Declarations of Conformity Appendix A 62 ...
Page 1203: ...Appendix EC Declarations of Conformity FR A800 A 63 ...
Page 1204: ...EC Declarations of Conformity Appendix A 64 ...
Page 1205: ...Appendix EC Declarations of Conformity FR A800 A 65 ...
Page 1206: ...EC Declarations of Conformity Appendix A 66 ...
Page 1207: ...Appendix EC Declarations of Conformity FR A800 A 67 ...
Page 1208: ...EC Declarations of Conformity Appendix A 68 ...
Page 1209: ...Appendix EC Declarations of Conformity FR A800 A 69 ...
Page 1210: ...EC Declarations of Conformity Appendix A 70 ...
Page 1211: ...Appendix EC Declarations of Conformity FR A800 A 71 ...
Page 1212: ...EC Declarations of Conformity Appendix A 72 A 7 2 FR A846 series ...
Page 1213: ...Appendix EC Declarations of Conformity FR A800 A 73 ...
Page 1214: ...EC Declarations of Conformity Appendix A 74 ...
Page 1215: ...Appendix EC Declarations of Conformity FR A800 A 75 ...
Page 1217: ......