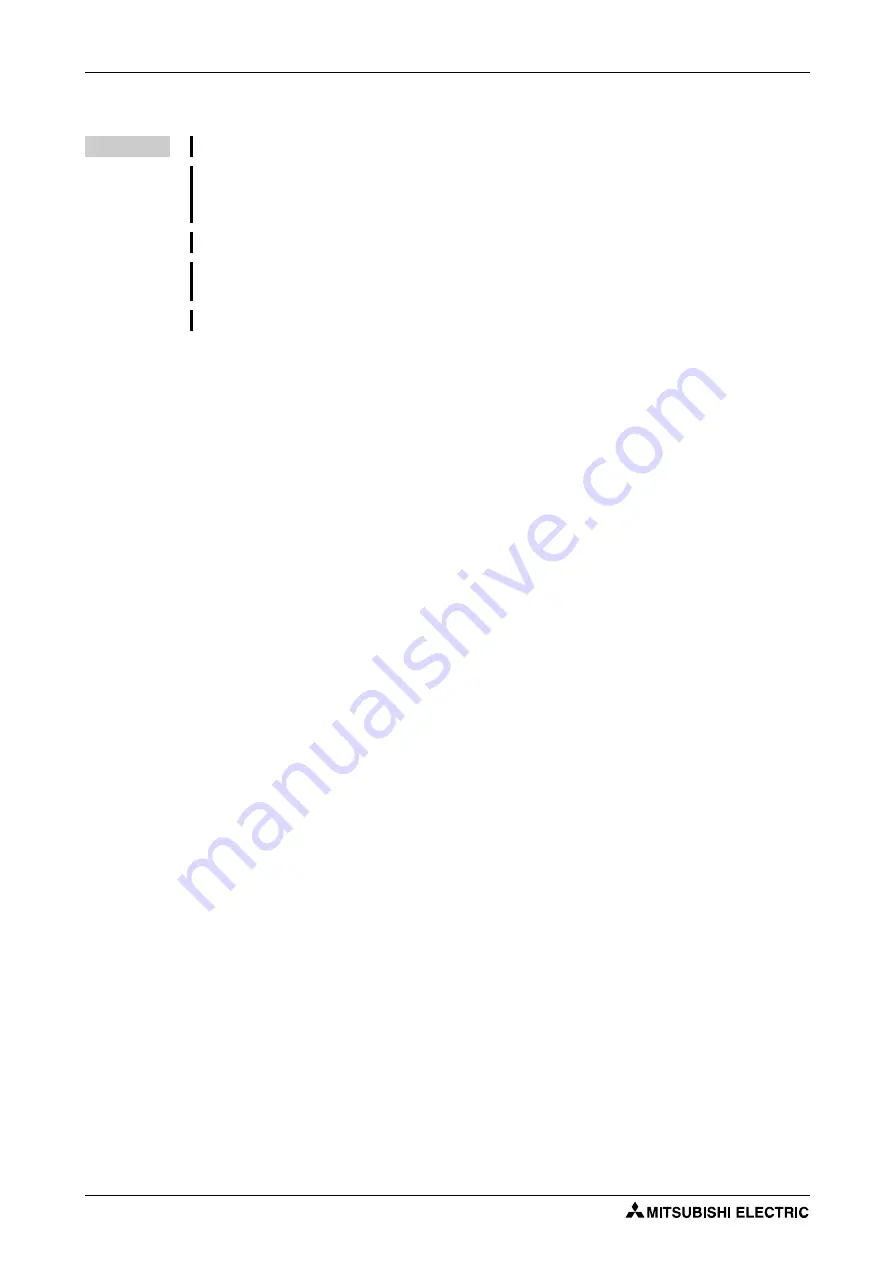
(C) Motor constant parameters
Parameters
5 - 474
Before performing offline auto tuning
Check the following points before performing offline auto tuning.
●
The PM sensorless vector control is selected.
●
A motor is connected. Note that the motor should be at a stop at a tuning start. (The motor should
not be rotated by the force applied from outside during the tuning.)
●
For the motor capacity, the rated motor current should be equal to or less than the inverter rated
current. (It must be 0.4 kW or higher.) If a motor with substantially low rated current compared
with the inverter rated current is used, speed and torque accuracies may deteriorate due to torque
ripples, etc. Set the rated motor current to about 40% or higher of the inverter rated current.
●
The maximum frequency under PM sensorless vector control is 400 Hz.
●
The motor may rotate slightly even if the offline auto tuning without motor rotation (Pr. 96 "Auto
tuning setting/status" = "1 or 11") is selected. (It does not affect the tuning performance.) Fix the
motor securely with a mechanical brake, or before tuning, make sure that it is safe even if the
motor rotates. (Caution is required especially in vertical lift applications.)
●
Tuning is not available during position control under PM sensorless vector control.
NOTES
The settings are valid under the PM sensorless vector control.
The offline auto tuning enables the operation with SPM motors and IPM motors other than
MM-CF. (When a PM motor other than the IPM motor MM-CF is used, always perform the offline
auto tuning.)
Tuning is enabled even when a load is connected to the motor.
Reading/writing of the motor constants tuned by offline auto tuning are enabled. The offline auto
tuning data (motor constants) can be copied to another inverter with the operation panel.
The offline auto tuning status can be monitored with the operation panel and the parameter unit.
Summary of Contents for FR-A820-00046 (0.4K)
Page 2: ......
Page 4: ......
Page 144: ...System configuration for Ethernet communication FR A800 E Installation and wiring 2 114 ...
Page 202: ...Basic operation procedure JOG operation Basic operation 4 32 ...
Page 1090: ...Check first when you have a trouble Protective functions 6 50 ...
Page 1189: ...Appendix EC Declarations of Conformity FR A800 A 49 ...
Page 1190: ...EC Declarations of Conformity Appendix A 50 ...
Page 1191: ...Appendix EC Declarations of Conformity FR A800 A 51 ...
Page 1192: ...EC Declarations of Conformity Appendix A 52 ...
Page 1193: ...Appendix EC Declarations of Conformity FR A800 A 53 ...
Page 1194: ...EC Declarations of Conformity Appendix A 54 ...
Page 1195: ...Appendix EC Declarations of Conformity FR A800 A 55 ...
Page 1196: ...EC Declarations of Conformity Appendix A 56 ...
Page 1197: ...Appendix EC Declarations of Conformity FR A800 A 57 ...
Page 1198: ...EC Declarations of Conformity Appendix A 58 ...
Page 1199: ...Appendix EC Declarations of Conformity FR A800 A 59 ...
Page 1200: ...EC Declarations of Conformity Appendix A 60 ...
Page 1201: ...Appendix EC Declarations of Conformity FR A800 A 61 ...
Page 1202: ...EC Declarations of Conformity Appendix A 62 ...
Page 1203: ...Appendix EC Declarations of Conformity FR A800 A 63 ...
Page 1204: ...EC Declarations of Conformity Appendix A 64 ...
Page 1205: ...Appendix EC Declarations of Conformity FR A800 A 65 ...
Page 1206: ...EC Declarations of Conformity Appendix A 66 ...
Page 1207: ...Appendix EC Declarations of Conformity FR A800 A 67 ...
Page 1208: ...EC Declarations of Conformity Appendix A 68 ...
Page 1209: ...Appendix EC Declarations of Conformity FR A800 A 69 ...
Page 1210: ...EC Declarations of Conformity Appendix A 70 ...
Page 1211: ...Appendix EC Declarations of Conformity FR A800 A 71 ...
Page 1212: ...EC Declarations of Conformity Appendix A 72 A 7 2 FR A846 series ...
Page 1213: ...Appendix EC Declarations of Conformity FR A800 A 73 ...
Page 1214: ...EC Declarations of Conformity Appendix A 74 ...
Page 1215: ...Appendix EC Declarations of Conformity FR A800 A 75 ...
Page 1217: ......