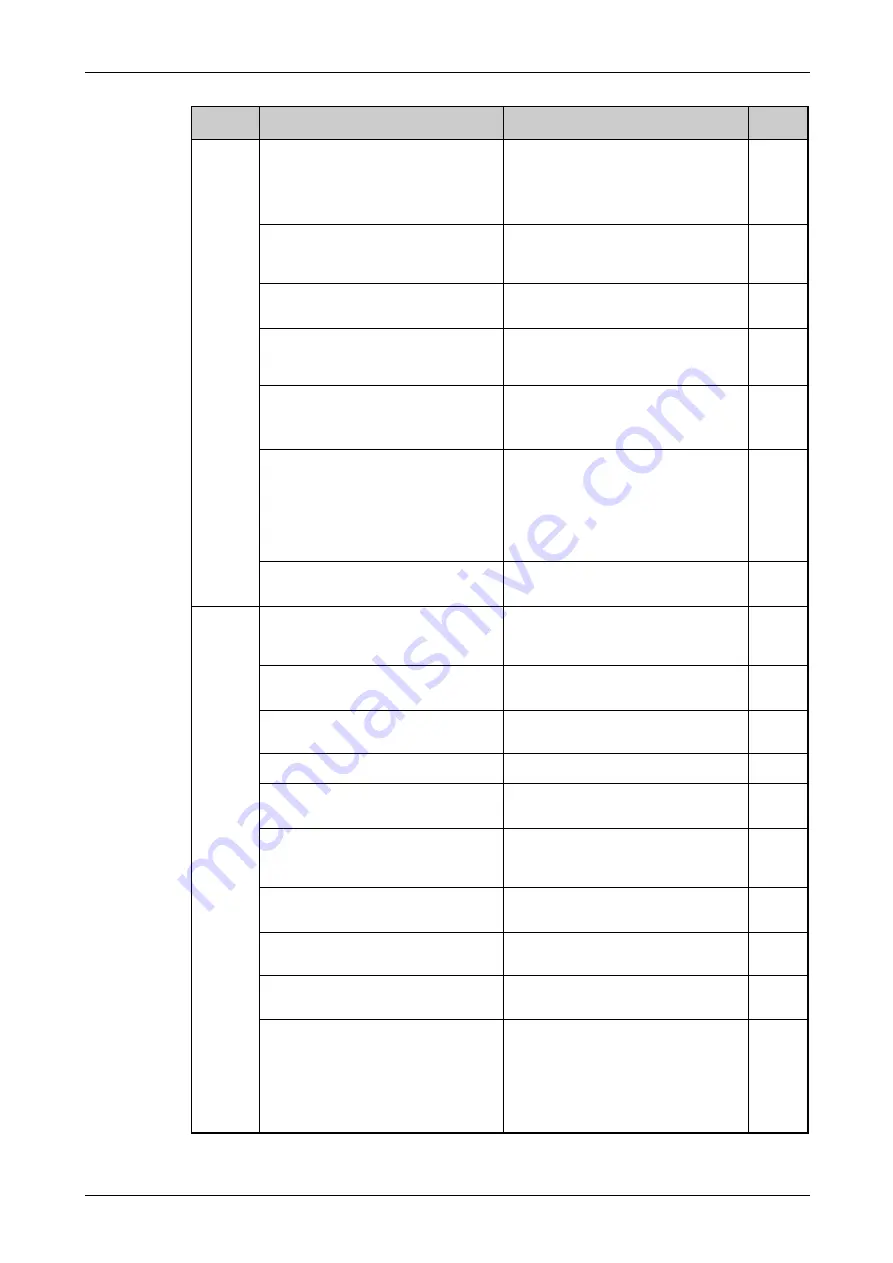
Protective functions
Check first when you have a trouble
FR-A800
6 - 41
Input
signal
CS signal is OFF while the automatic restart
after instantaneous power failure function is
selected (Pr. 57 "Restart coasting time"
≠
9999).
(FWD or REV LED on the operation panel is
flickering.)
Turn ON the automatic restart after
instantaneous power failure/flying start (CS)
signal.
When the CS signal is assigned to an input
terminal, automatic restart operation is
enabled when the CS signal is turned ON.
Jumper connector of sink - source is incorrectly
selected. (FWD or REV LED on the operation
panel is flickering.)
Check that the control logic switchover jumper
connector is correctly installed.
If it is not installed correctly, input signal is not
recognized.
Wiring of encoder is incorrect.
(Under encoder feedback control or vector
control)
Check the wiring of encoder.
Voltage/current input switch is not correctly set
for analog input signal (0 to 5 V/0 to 10 V, 4 to
20 mA). (FWD or REV LED on the operation
panel is flickering.)
Set Pr. 73 "Analog input selection", Pr. 267
"Terminal 4 input selection", and a voltage/
current input switch correctly, then input an
analog signal in accordance with the setting.
STOP/RESET key was pressed.
(Operation panel indication is "PS".)
During the External operation mode, check the
method of restarting from a STOP/RESET key
input stop from PU.
For the separated converter type, terminals
RDA and SE of the converter unit are not
connected to terminals MRS (X10 signal) and
SD (PC for source logic) of the inverter
respectively.
Check for the wiring.
Refer to
the In-
struction
Manual
(Hard-
ware) of
the FR-
A802.
Two-wire or three-wire type connection is
incorrect.
Check the wiring.
Use the Start self-holding selection (STP
(STOP)) signal when the three-wire type is used.
Parameter
setting
Under V/F control, Pr. 0 "Torque boost" setting
is improper.
Increase the Pr. 0 setting by 0.5% increments
while observing the rotation of a motor.
If that makes no difference, decrease the
setting.
Pr. 78 "Reverse rotation prevention selection" is
set.
Check the Pr. 78 setting.
Set Pr. 78 when you want to limit the motor
rotation to only one direction.
Pr. 79 "Operation mode selection" setting is
incorrect.
Select the operation mode which corresponds
with input methods of start command and
frequency command.
Bias and gain (calibration parameters C2 to C7)
settings are improper.
Check the bias and gain (calibration
parameters C2 to C7) settings.
Pr. 13 "Starting frequency" setting is greater
than the running frequency.
Set running frequency higher than Pr.13.
The inverter does not start if the frequency
setting signal is less than the value set in Pr. 13.
Frequency settings of various running
frequency (such as multi-speed operation) are
zero.
Especially, Pr. 1 "Maximum frequency" is zero.
Set the frequency command according to the
application.
Set Pr. 1 higher than the actual frequency used.
Pr. 15 "Jog frequency" is lower than Pr. 13
"Starting frequency" for JOG operation.
Set Pr. 15 higher than Pr. 13.
The Pr. 359 (852) "Encoder rotation direction"
setting is incorrect under encoder feedback
control or under vector control.
If the "REV" on the operation panel is lit even
though the forward-rotation command is
given, set Pr. 359 (852) = "1".
When a vector control option is used, the
option to be used and parameter settings do
not match.
Correctly set Pr. 862 "Encoder option selection"
according to the option to be used.
Operation mode and a writing device do not
correspond.
Check Pr. 79
"
Operation mode selection
"
,
Pr. 338 "Communication operation command
source", Pr. 339 "Communication speed
command source", Pr. 550 "NET mode
operation command source selection" and
Pr. 551"PU mode operation command source
selection", and select an operation mode
suitable for the purpose.
Check
points
Possible cause
Countermeasure
Refer to
page
Summary of Contents for FR-A820-00046 (0.4K)
Page 2: ......
Page 4: ......
Page 144: ...System configuration for Ethernet communication FR A800 E Installation and wiring 2 114 ...
Page 202: ...Basic operation procedure JOG operation Basic operation 4 32 ...
Page 1090: ...Check first when you have a trouble Protective functions 6 50 ...
Page 1189: ...Appendix EC Declarations of Conformity FR A800 A 49 ...
Page 1190: ...EC Declarations of Conformity Appendix A 50 ...
Page 1191: ...Appendix EC Declarations of Conformity FR A800 A 51 ...
Page 1192: ...EC Declarations of Conformity Appendix A 52 ...
Page 1193: ...Appendix EC Declarations of Conformity FR A800 A 53 ...
Page 1194: ...EC Declarations of Conformity Appendix A 54 ...
Page 1195: ...Appendix EC Declarations of Conformity FR A800 A 55 ...
Page 1196: ...EC Declarations of Conformity Appendix A 56 ...
Page 1197: ...Appendix EC Declarations of Conformity FR A800 A 57 ...
Page 1198: ...EC Declarations of Conformity Appendix A 58 ...
Page 1199: ...Appendix EC Declarations of Conformity FR A800 A 59 ...
Page 1200: ...EC Declarations of Conformity Appendix A 60 ...
Page 1201: ...Appendix EC Declarations of Conformity FR A800 A 61 ...
Page 1202: ...EC Declarations of Conformity Appendix A 62 ...
Page 1203: ...Appendix EC Declarations of Conformity FR A800 A 63 ...
Page 1204: ...EC Declarations of Conformity Appendix A 64 ...
Page 1205: ...Appendix EC Declarations of Conformity FR A800 A 65 ...
Page 1206: ...EC Declarations of Conformity Appendix A 66 ...
Page 1207: ...Appendix EC Declarations of Conformity FR A800 A 67 ...
Page 1208: ...EC Declarations of Conformity Appendix A 68 ...
Page 1209: ...Appendix EC Declarations of Conformity FR A800 A 69 ...
Page 1210: ...EC Declarations of Conformity Appendix A 70 ...
Page 1211: ...Appendix EC Declarations of Conformity FR A800 A 71 ...
Page 1212: ...EC Declarations of Conformity Appendix A 72 A 7 2 FR A846 series ...
Page 1213: ...Appendix EC Declarations of Conformity FR A800 A 73 ...
Page 1214: ...EC Declarations of Conformity Appendix A 74 ...
Page 1215: ...Appendix EC Declarations of Conformity FR A800 A 75 ...
Page 1217: ......