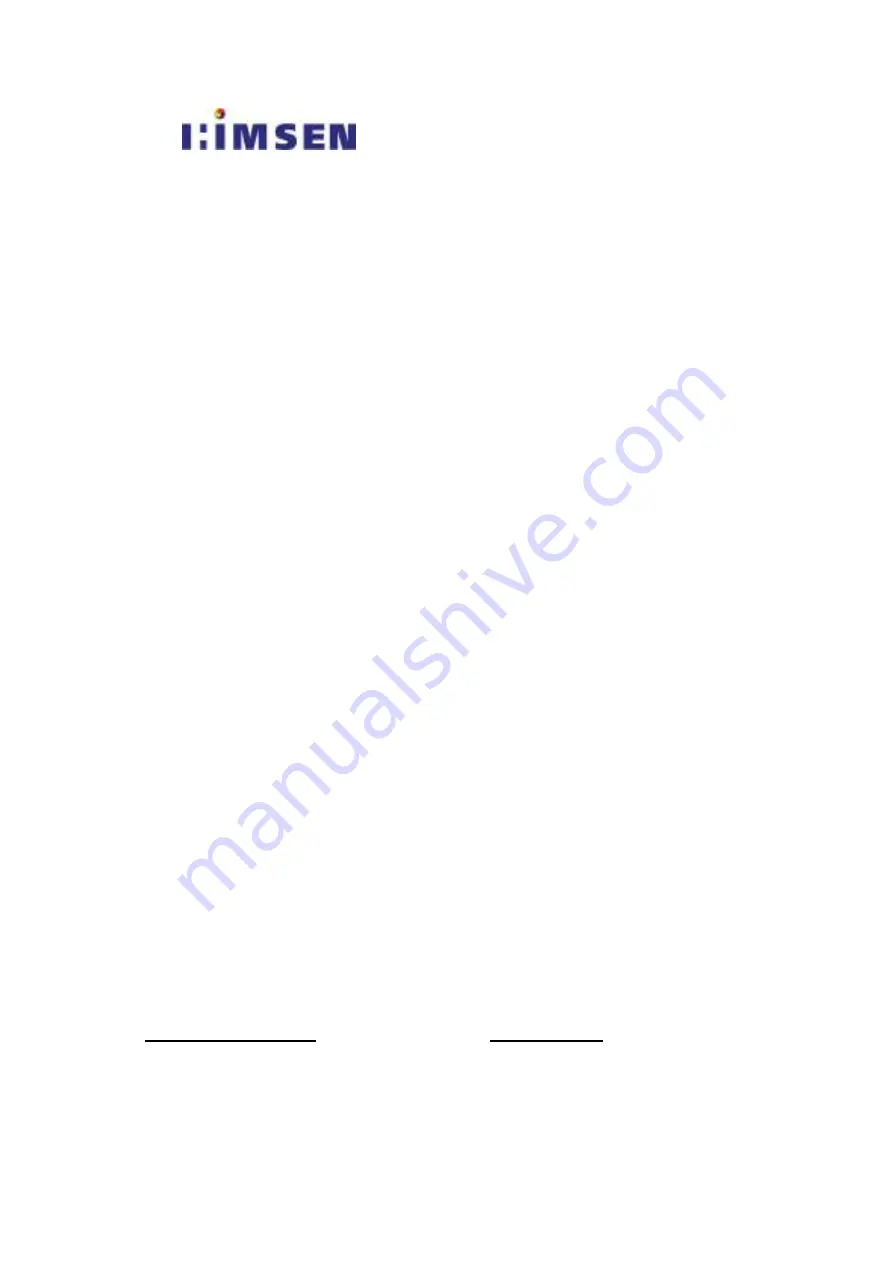
HYUNDAI
INSTRUCTION BOOK
VOLUME
I
Engine type
H21/32
Hyundai Heavy Industries Co., Ltd.
Engine & Machinery Division
1, Cheonha-Dong, Dong-Gu, Ulsan, Korea
http://www.hhi.co.kr
http://as.hyundai-engine.com
Engine After-sales Service Dept.
Warranty
Service
TEL : (82) 52-202-7412~20
FAX : (82) 52-202-7581
(82) 52-250-9841
E-mail : [email protected]
Parts Sales
TEL : (82) 52-202-7311~20
FAX : (82) 52-202-7582
E-mail : [email protected]