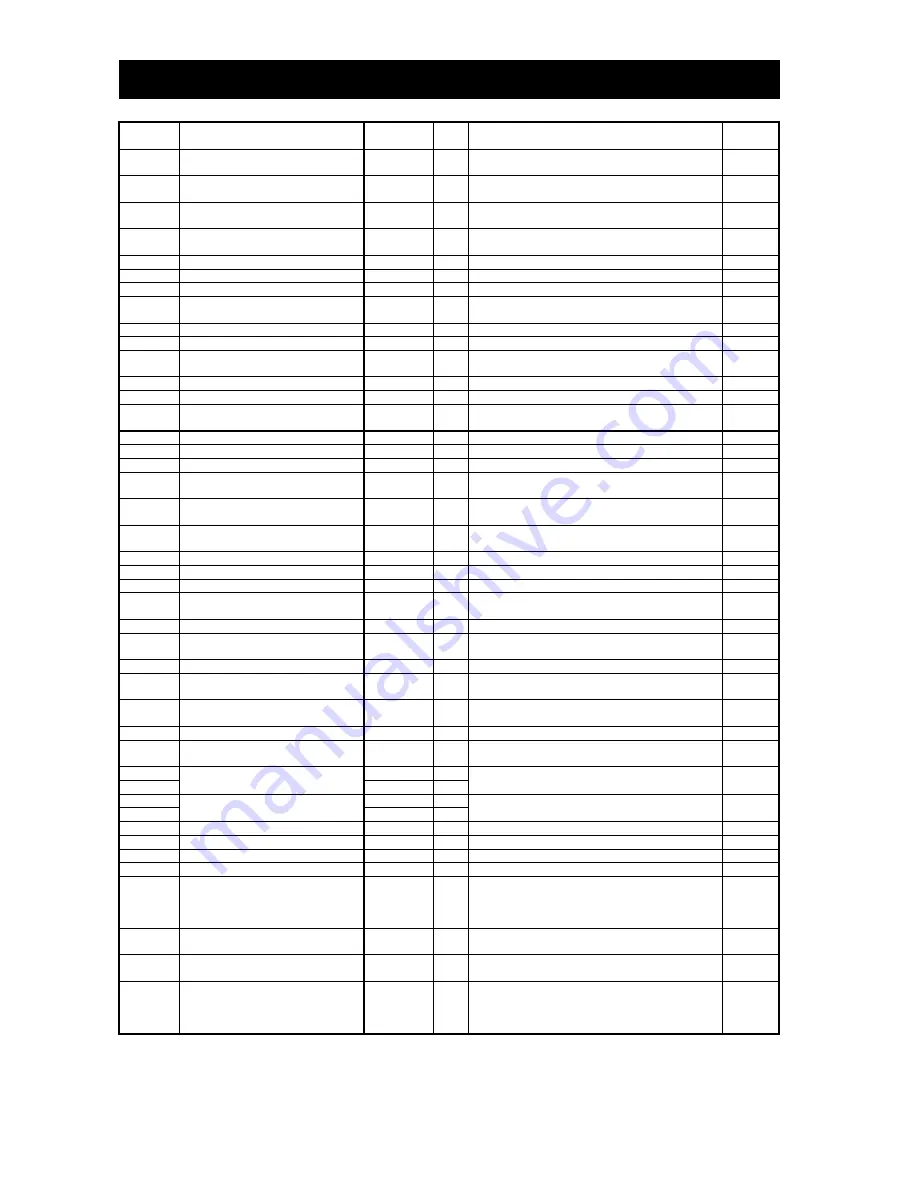
Chapter 4
Explanation of Functions
4-160
Register No.
Function name
Function code R/W
Monitoring and setting items Data resolution
Data
resolution
1601h
Operation mode on expansion card 1
error
P001
R/W 0 (tripping), 1 (continuing operation)
-
1602h
Operation mode on expansion card 2
error
P002
R/W 0 (tripping), 1 (continuing operation)
-
1603h to
160Ah
(Reserved)
-
-
Inaccessible
-
160Bh
Encoder pulse-per-revolution (PPR)
setting
P011
R/W 128 to 65000
1
160Ch
Control pulse setting
P012
R/W 0 (ASR), 1 (APR)
-
160Dh
Pulse train mode setting
P013
R/W 0 (mode 0), 1 (mode 1), 2 (mode 2)
-
160Eh
Home search stop position setting
P014
R/W 0 to 4095
1
160Fh
Home search speed setting
P015
R/W
"start frequency" to "maximum frequency " (up to
12000)
0.01 [Hz]
1610h
Home search direction setting
P016
R/W 0 (forward), 1 (reverse)
-
1611h
Home search completion range setting
P017
R/W 0 to 10000
1
1612h
Home search completion delay time
setting
P018
R/W 0 to 999
0.01 [sec.]
1613h
Electronic gear set position selection
P019
R/W 0 (feedback side), 1 (commanding side)
-
1614h
Electronic gear ratio numerator setting
P020
R/W 1 to 9999
-
1615h
Electronic gear ratio denominator
setting
P021
R/W 1 to 9999
-
1616h
Feed-forward gain setting
P022
R/W 0 to 65535
0.01
1617h
Position loop gain setting
P023
R/W 0 to 10000
0.01
1618h
Position bias setting
P024
-
-2048 to 2048
1
1619h
Temperature compensation thermistor
enable
P025
R/W 00 (no compensation), 01 (compensation)
-
161Ah
Over-speed error detection level
setting
P026
R/W 0 to 1500
0.1 [%]
161Bh
Speed deviation error detection level
setting
P027
R/W 0 to 12000
0.01 [Hz]
161Ch
Numerator of the motor gear ratio
P028
R/W 1 to 9999
1
161Dh
Denominator of the motor gear ratio
P029
R/W 1 to 9999
1
161Eh
(Reserved)
-
-
Inaccessible
-
161Fh
Accel/decel time input selection
P031
R/W
0 (digital operator), 1 (option 1), 2 (option 2), 3 (easy
sequence)
-
1620h
Positioning command input selection
P032
R/W 0 (digital operator), 1 (option 1), 2 (option 2)
-
1621h
Torque command input selection
P033
R/W
0 (O terminal), 1 (OI terminal), 2 (O2 terminal), 3
(digital operator)
-
1622h
Torque command setting
P034
R/W 0 to 200 <0 to 180>
1 [%]
1623h
Polarity selection at the torque
command input via O2 terminal
P035
R/W
0 (as indicated by the sign), 1 (depending on the
operation direction)
-
1624h
Torque bias mode
P036
R/W
0 (disabling the mode), 1 (digital operator), 2 (input
via O2 terminal)
-
1625h
Torque bias value
P037
R/W -200 to +200 <-180 to +180>
1 [%]
1626h
Torque bias polarity selection
P038
R/W
0 (as indicated by the sign), 1 (depending on the
operation direction)
-
1627h
Speed limit for torque-controlled
operation (forward rotation)
P039 (high)
R/W
0 to "maximum frequency "
0.01 [Hz]
1628h
P039 (low)
R/W
1629h
Speed limit for torque-controlled
operation (reverse rotation)
P040 (high)
R/W
0 to "maximum frequency "
0.01 [Hz]
162Ah
P040 (low)
R/W
162Bh
(Reserved)
-
-
Inaccessible
-
162Ch
(Reserved)
-
-
Inaccessible
-
162Dh
(Reserved)
-
-
Inaccessible
-
162Eh
DeviceNet comm watchdog timer
P044
R/W 0 to 9999
0.01 [sec.]
162Fh
Inverter action on DeviceNet comm
error
P045
R/W
0 (tripping), 1 (tripping after decelerating and
stopping the motor), 2 (ignoring errors), 3 (stopping
the motor after free-running), 4 (decelerating and
stopping the motor)
-
1630h
DeviceNet polled I/O: Output instance
number
P046
R/W 20, 21, 100
-
1631h
DeviceNet polled I/O: Input instance
number
P047
R/W 70, 71, 101
-
1632h
Inverter action on DeviceNet idle mode
P048
R/W
0 (tripping), 1 (tripping after decelerating and
stopping the motor), 2 (ignoring errors), 3 (stopping
the motor after free-running), 4 (decelerating and
stopping the motor)
-
(Note) <>indicate the setting range of 75 to 150kW
Summary of Contents for SJ700D-004L
Page 16: ...Contents Appendix Appendix A 1 Index Index Index 1 ...
Page 44: ...Chapter 2 Installation and Wiring 2 23 Memo ...
Page 70: ...Chapter 3 Operation 3 25 Memo ...
Page 248: ...Chapter 5 Error Codes 5 11 Memo ...
Page 256: ...Chapter6 Maintenance and Inspection 6 7 Memo ...