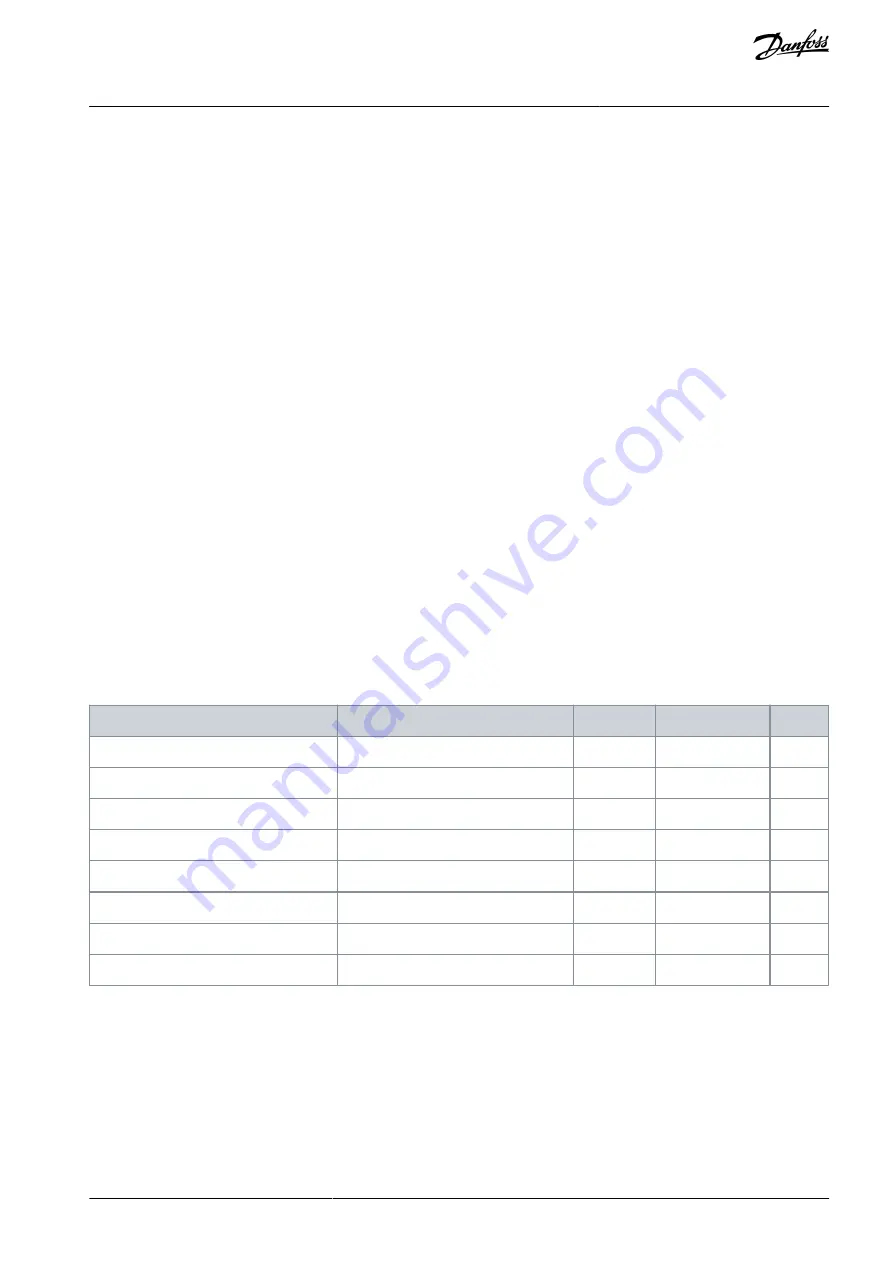
10.622 Parameters of Stall Protection (IDs 709–712)
The motor stall protection function gives protection to the motor against short overloads. An overload can be caused, for example,
by a stalled shaft. It is possible to set the reaction time of the stall protection shorter than that of the motor thermal protection.
The stall status of the motor is specified with parameters
ID 710
(
Stall current
) and
ID 712
(
Stall frequency limit
). If the current is higher
than the limit, and the output frequency is lower than the limit, the motor is in a stall status.
The stall protection is a type of overcurrent protection.
When using long motor cables (maximum 100 m) with small drives (≤1.5 kW), the motor current that the drive measures can be
much higher than the actual motor current. It is because there are capacitive currents in the motor cable.
10.623 Parameters of Underload Protection (IDs 713–716)
The motor underload protection makes sure that there is a load on the motor when the drive operates. If the motor loses the load, a
problem can occur in the process. For example, a belt can break or a pump become dry.
You can adjust the motor underload protection with parameters
ID 714
(
Field Weakening Area Load
) and
ID 715
(
Zero Frequency
Load
). The underload curve is a squared curve between the zero frequency and the field weakening point. The protection is not
active below 5 Hz.
The underload time counter does not operate below 5 Hz. The values of the underload protection parameters are set in percentage
of the nominal torque of the motor. To find the scaling ratio for the internal torque value, use the data in the nameplate data of the
motor, the motor nominal current, and the nominal current of the drive I
H
. When using another current than the nominal motor
current, the precision of the calculation decreases.
When using long motor cables (maximum 100 m) with small drives (≤1.5 kW), the motor current that the drive measures can be
much higher than the actual motor current. It is because there are capacitive currents in the motor cable.
10.624 Fieldbus Control Parameters (IDs 850–859)
The Fieldbus control parameters are used when the frequency or the speed reference comes from the fieldbus (Modbus, PROFIBUS,
DeviceNet, and so on). Use the Fieldbus Data Out Selection 1–8 to monitor values from the fieldbus.
10.624.1 Process Data Out (Slave -> Master)
The fieldbus master can read the actual values of the AC drive using process data variables. Basic, Standard, Local/Remote, Multi-
Step, PID Control, and Pump and Fan Control Applications use process data as follows:
Table 121: The Default Values for Process Data Out in Fieldbus
Data
Default value
Unit
Scale
ID
Process Data Out 1
Output frequency
Hz
0.01 Hz
1
Process Data Out 2
Motor speed
RPM
1 RPM
2
Process Data Out 3
Motor current
A
0.1 A
45
Process Data Out 4
Motor torque
%
0.1%
4
Process Data Out 5
Motor power
%
0.1%
5
Process Data Out 6
Motor voltage
V
0.1 V
6
Process Data Out 7
DC-link voltage
V
1 V
7
Process Data Out 8
Active fault code
-
-
-
The Multi-purpose Control Application has a selector parameter for every Process Data. The monitoring values and drive parameters
can be selected using the ID number. Default selections are as in the table.
10.624.2 Current Scaling in Different Size of Units
Monitoring value
ID 45
(usually in Process data OUT3) is given with one decimal only.
AB296635287482en-000301 / DPD00903 | 309
Danfoss A/S © 2023.02
Parameter Descriptions
VACON® NX All-in-One
Application Guide
Summary of Contents for VACON NX
Page 1: ...Application Guide VACON NX All in One drives danfoss com...
Page 2: ......