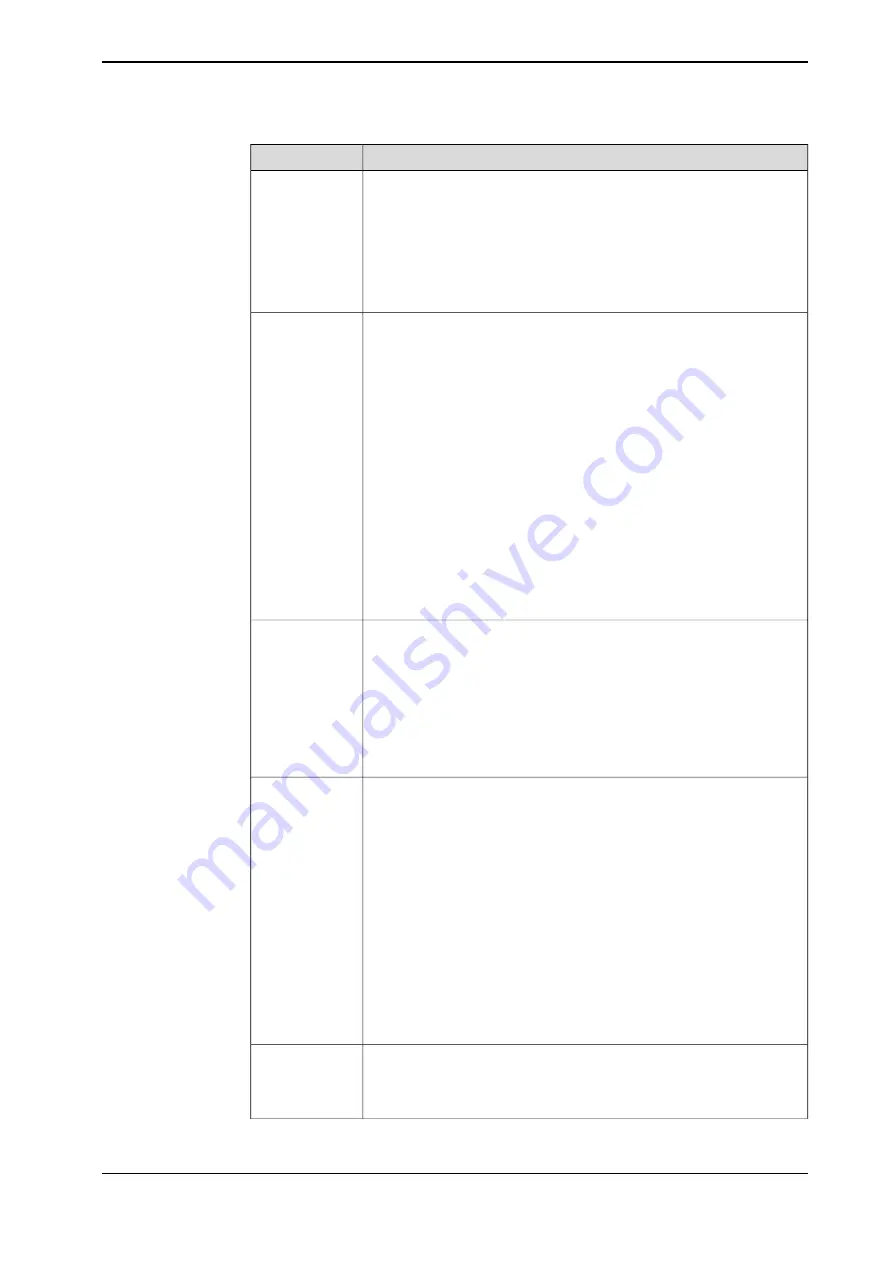
Description
Revision
Published in release 21C. The following updates are done in this revision:
•
Added a note to the procedure of enabling the lead-through device.
•
Added spare part parallel pin on extender unit and updated related
refitting procedure of extender unit.
•
Corrected the description of connection point on cabinet.
•
Updated the naming of timing belt tension adjustment tools, from
acoustic tensiometer and tensiometer to sonic tension meter and
dynamometer, respectively.
C
Published in release 22A. The following updates are done in this revision:
•
Added information about length of thread engagement for attach-
ment screws.
•
Added cautions in procedures of removing timing belts, motors
and gearboxes.
•
Updated dimension figures to include dimension for bottom con-
nector interface option.
•
Added troubleshooting for high motor temperature, see
temperature too high on page 688
•
Updated information about Gleitmo treated screws, see
.
•
Updated information of lead-through device and laser scanner
connection and configuration due to new introduction of Collabor-
ative Speed Control add-in and new laser scanner options. See
Installation of lead-through device on page 71
,
and
Configuring the software on page 94
•
Removed caution about not to use cleaning detergents containing
ethanol, organic solvent or similar to clean the lamp cover.
D
Published in release 22B. The following updates are done in this revision
•
Updated the optional port from LAN port to MGMT port, which is
used to connect the cable from robot to controller for lead-through
functionality.
•
Added installation and configuration of the two-button-type lead-
through device.
•
Added a list of general software configuration procedure.
•
Added a note about the requirement for connecting lamp unit
cabling.
E
Published in release 22C. The following updates are done in this revision
•
Updated robot power cable information, see
.
•
Updated spare part numbers for axes 1-6 motors.
•
Added expected life of gearboxes.
•
Updated cable connection figures for safetyIO-based scanner(s).
•
Added the lamp unit cabling when the controller is configured with
safety I/O device DSQC1042.
•
Added a caution about carefully using of the lead-through device
on the robot.
•
Updated information label figure.
•
Updated the connection figures and configuration procedure of
the safetyIO-based laser scanners.
•
Removed the troubleshooting for issue of RED flashing status on
Scalable I/O device and failure to move the robot.
F
Published in release 22D. The following updates are done in this revision:
•
Added information about Wrist Optimization in calibration chapter.
•
Added notes about installation and configuration of additional
scalable I/O device.
G
Continues on next page
Product manual - CRB 1100
11
3HAC078007-001 Revision: J
© Copyright 2021-2023 ABB. All rights reserved.
Overview of this manual
Continued
Summary of Contents for CRB 1100
Page 1: ...ROBOTICS Product manual CRB 1100 ...
Page 162: ...This page is intentionally left blank ...
Page 184: ...This page is intentionally left blank ...
Page 652: ...This page is intentionally left blank ...
Page 698: ...This page is intentionally left blank ...
Page 712: ...This page is intentionally left blank ...
Page 714: ...This page is intentionally left blank ...
Page 719: ......