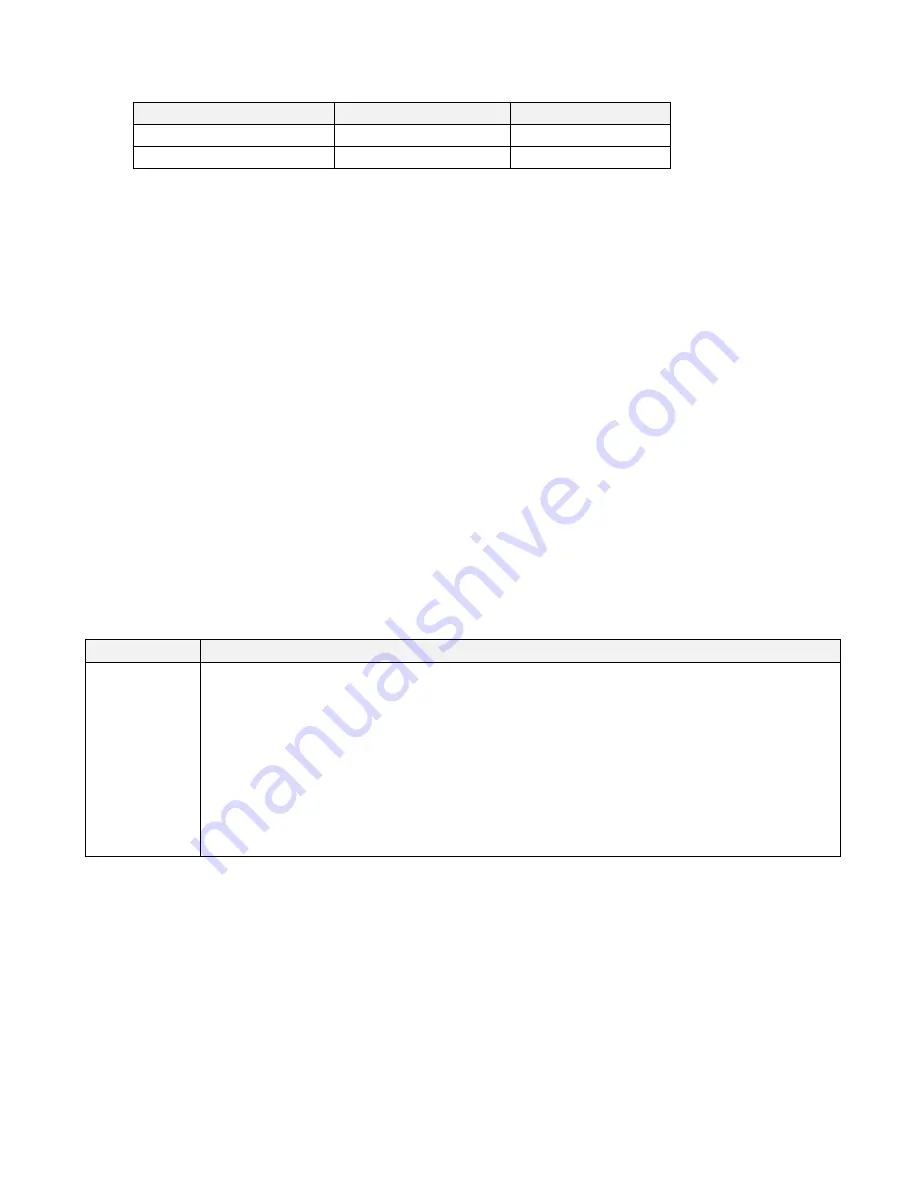
A-4
Horse Power ( HP )
Current ( A )
Voltage ( V )
1 - 50
5,000
240 / 480
51 - 200
10,000
240 / 480
Inverter Motor Overload Protection
Set parameter 02-01 (motor rated current) to the appropriate value to enable motor overload protection. The
internal motor overload protection is UL listed and in accordance with the NEC and CEC.
■
02-01 Motor Rated Current
Setting Range Model Dependent
Factory Default: Model Dependent
The motor rated current parameter (02-01) protects the motor. The motor protection parameter 08-05 is set as
factory default. Set 02-01 to the full load amps (FLA) as shown on the nameplate of the motor.
■
08-05 Motor Overload Protection Selection
The inverter has an electronic overload protection function (OL1) based on time, output current, and output
frequency, which protects the motor from overheating. The electronic thermal overload function is UL-recognized,
so it does not require an external thermal overload relay for single motor operation.
This parameter selects the motor overload curve used according to the type of motor applied.
08-05
Selection for motor overload protection (OL1)
Range
【
xxx0b
】:
Motor overload is disabled
【
xxx1b
】:
Motor overload is enabled
【
xx0xb
】:
Cold start of motor overload
【
xx1xb
】:
Hot start of motor overload
【
x0xxb
】:
Standard motor
【
x1xxb
】:
Special motor
【
0xxxb
】:
Reserved
【
1xxxb
】:
Reserved
Sets motor overload protection function in parameter 08-05 according to the applicable motor.
08-05 = 0:
Disables the motor overload protection function when two or more motors are connected to a single
inverter. Use an alternative method to provide separate overload protection for each motor such as connecting a
thermal overload relay to 1he power line of each motor.
08-05 = 1:
The motor overload protection function should be set to hot start protection characteristic curve when
the power supply is turned on and off frequently, because the thermal values are reset each time when the power
is turned off.