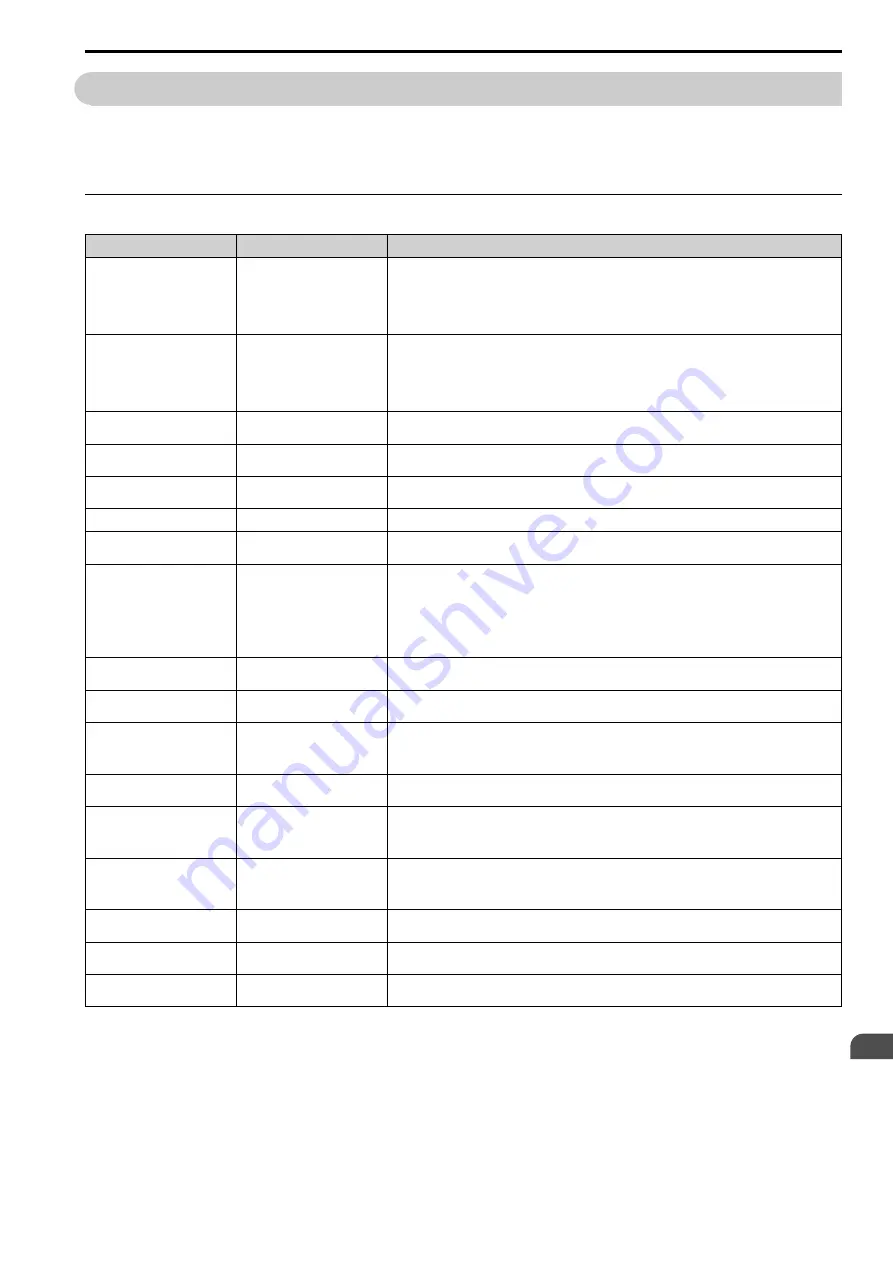
10.9 Peripheral Devices and Options
SIEPYEUOQ2A01G AC Drive Q2A Technical Manual
407
10.9
Peripheral Devices and Options
This chapter shows the available peripheral devices and options for the drive.
•
Selection: Refer to the drive catalog for information about available products.
•
Installation and wiring: Refer to the instruction manual for each option.
◆
Main Circuit Options
Name
Model
Purpose
DC Reactor
UZDA series
To improve the drive input power factor.
•
To prevent damage to the drive when the power supply capacity is large. You must only use this option
when the power supply capacity is more than 600 kVA.
•
To decrease harmonic current.
•
To improve the power supply total power factor.
AC Reactor
UZBA series
To improve the drive input power factor.
•
To prevent damage to the drive when the power supply capacity is large. You must only use this option
when the power supply capacity is more than 600 kVA.
•
To decrease harmonic current.
•
To improve the power supply total power factor.
Braking Resistor
ERF-150WJ Series
To decrease the regenerative energy of the motor and decrease the deceleration time (duty cycle of 3%
ED). You must also use the installation attachment.
Braking Resistor with Fuse
CF120-B579 Series
To decrease the regenerative energy of the motor and decrease the deceleration time (duty cycle of 3%
ED). You must also use the installation attachment.
Braking Resistor Unit
LKEB series
To decrease the regenerative energy of the motor and decrease the deceleration time (duty cycle of 10%
ED). The unit contains a thermal overload relay.
Braking Unit
CDBR series
Use with a braking resistor unit to decrease motor deceleration times.
Molded-Case Circuit Breaker
(MCCB)
NF series
To prevent short circuit damage to the power supply system and provide overload protection for wiring.
Residual Current Monitor/
Detector (RCM/RCD)
NV and NS series
To prevent short circuit damage to the power supply system, provide overload protection for wiring,
prevent electrical shock, and provide ground fault protection against earth leakage fires.
Note:
•
You can use a molded-case circuit breaker as a replacement for an RCM/RCD that is upstream in the
power supply system.
•
When you use a high frequency RCM/RCD at the power input side of the drive, make sure that each
drive has a minimum cumulative sensitivity amperage of 30 mA.
Input Side Magnetic Contactor
(MC)
SC series
To prevent burn damage when connecting a braking resistor. This option fully opens the circuit between
the power supply and drive.
Surge Protective Device
400 V class: RFN3AL-504KD
To absorb open/close surges from the magnetic contactor and control relay. You must connect this option
to magnetic contactors, control relays, magnetic valves, or magnetic brake coils.
Zero-Phase Reactor
F6045GB
F11080GB
F200160PB
To decrease wiring noise. You can use this option on the input side and the output side of the drive.
Note:
Install this option around the drive input power system and as near to the drive as possible.
Fuse
Fuse Holder
400 V class: CR6L series, CS5F
series, or FWH series
To prevent part failure, we recommend that you connect a fuse to the input side of the drive.
Input Side Noise Filter
LNFB, LNFD, and FN series
To decrease wiring noise.
Note:
Install this option around the drive input power system and as near to the drive as possible.
Output Side Noise Filter
LF series
To decrease wiring noise.
Note:
Install this option around the drive input power system and as near to the drive as possible.
Capacitor-Type Noise Filter
3XYG 1003
To decrease wiring noise. You must only use this option around the drive input power system. Do not
connect this option to the output side.
Momentary Power Loss Recovery
Unit
400 V class: P0020
To make sure that the drive has power during the momentary power loss ride-thru time (2 seconds).
Low-Voltage Manual Load
Switch
“
AICUT
”
LB series
PM motors act as generators when coasting to provide voltage to terminals. Install this option to prevent
electric shock.
Содержание Q2A
Страница 2: ...This Page Intentionally Blank 2 SIEPYEUOQ2A01G AC Drive Q2A Technical Manual...
Страница 12: ...12 SIEPYEUOQ2A01G AC Drive Q2A Technical Manual...
Страница 18: ...i 2 Legal Information 18 SIEPYEUOQ2A01G AC Drive Q2A Technical Manual...
Страница 28: ...1 2 Features and Advantages of Control Methods 28 SIEPYEUOQ2A01G AC Drive Q2A Technical Manual...
Страница 64: ...2 9 Installation Methods 64 SIEPYEUOQ2A01G AC Drive Q2A Technical Manual...
Страница 166: ...4 9 Test Run Checklist 166 SIEPYEUOQ2A01G AC Drive Q2A Technical Manual...
Страница 172: ...5 2 European Standards 172 SIEPYEUOQ2A01G AC Drive Q2A Technical Manual...
Страница 173: ...Standards Compliance 5 5 2 European Standards SIEPYEUOQ2A01G AC Drive Q2A Technical Manual 173...
Страница 174: ...5 2 European Standards 174 SIEPYEUOQ2A01G AC Drive Q2A Technical Manual...
Страница 175: ...Standards Compliance 5 5 2 European Standards SIEPYEUOQ2A01G AC Drive Q2A Technical Manual 175...
Страница 176: ...5 2 European Standards 176 SIEPYEUOQ2A01G AC Drive Q2A Technical Manual...
Страница 258: ...6 2 Modbus Communications 258 SIEPYEUOQ2A01G AC Drive Q2A Technical Manual...
Страница 356: ...8 7 Storage Guidelines 356 SIEPYEUOQ2A01G AC Drive Q2A Technical Manual...
Страница 357: ...SIEPYEUOQ2A01G AC Drive Q2A Technical Manual 357 9 Disposal 9 1 Safety Precautions 358 9 2 Disposal Instructions 359...
Страница 360: ...9 2 Disposal Instructions 360 SIEPYEUOQ2A01G AC Drive Q2A Technical Manual...
Страница 526: ...11 20 Parameters Changed by PM Motor Code Selection 526 SIEPYEUOQ2A01G AC Drive Q2A Technical Manual...