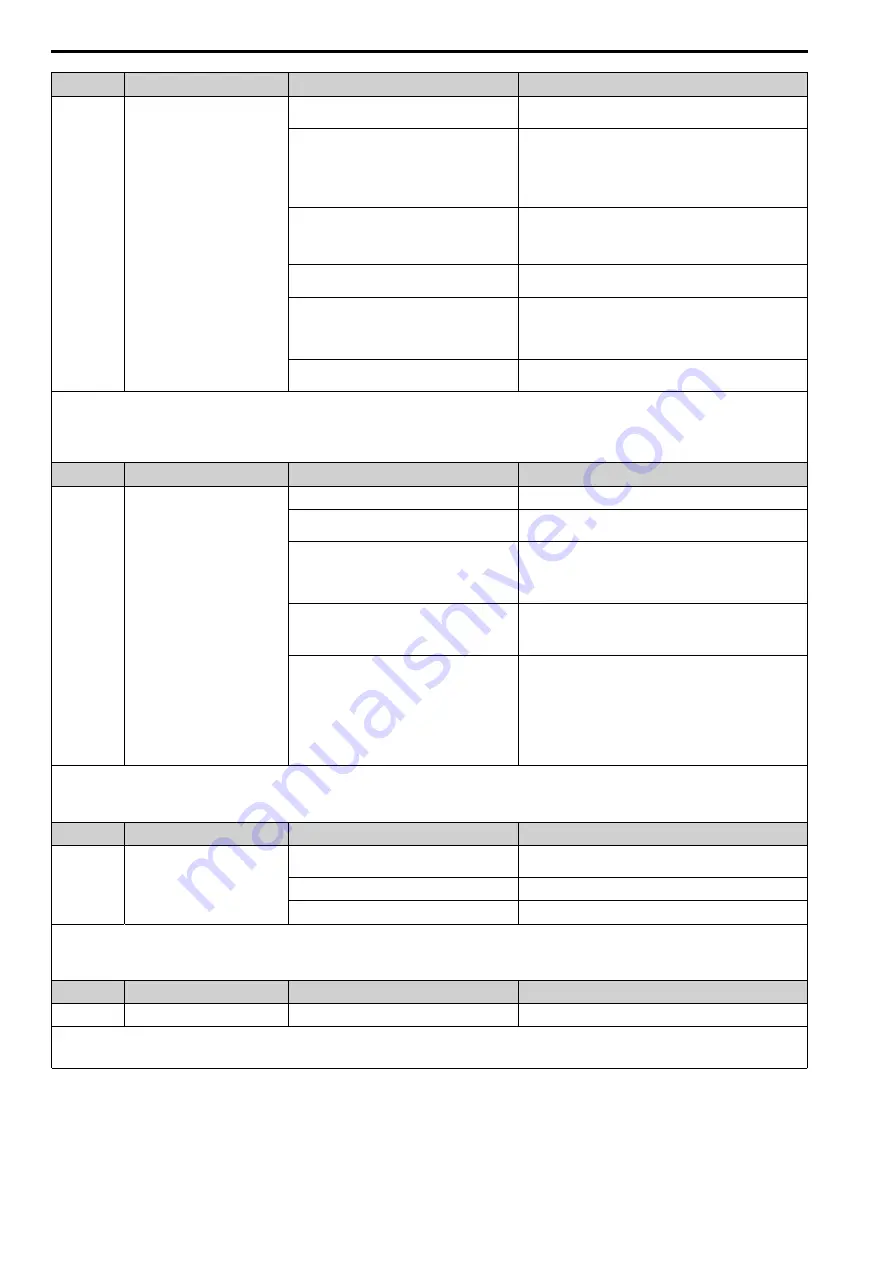
280
SIEPYEUOQ2A01G AC Drive Q2A Technical Manual
Code
Name
Causes
Possible Solutions
Noise interference along the encoder cable.
Isolate the encoder cable from the drive output line or a different
source of electrical interference.
Electrical interference caused a drive malfunction.
•
Examine the control circuit lines, main circuit lines, and
ground wiring, and decrease the effects of electrical
interference.
•
Make sure that a magnetic contactor is not the source of the
electrical interference, then use a Surge Protective Device if
necessary.
The load inertia is set incorrectly.
•
Examine the load inertia settings with KEB, overvoltage
suppression, or stall prevention during deceleration.
•
Adjust
L3-25 [Load Inertia Ratio]
to match the qualities of the
machine.
The Short Circuit Braking function used in OLV/
PM control method.
Connect a braking resistor to the drive.
There is motor hunting.
•
Adjust
n1-02 [HuntPrev Gain Setting]
settings.
•
Adjust
n2-02 [AFR Time 1]
and
n2-03 [AFR Time 2]
settings.
•
Adjust
n8-45 [SpdFbck Det.Gain]
and
n8-47 [Pull-In Comp.
Time Constant]
settings.
Speed search does not complete at start when you
use an induction motor in EZOLV control.
When
E9-01 = 0 [Motor Type Selection = IM]
, set
b3-24 = 2
[SpSrch Method Selection = Current Det2]
.
Note:
•
The drive detects this error if the DC bus voltage is more than the
ov
detection level while the drive is running.
•
The
ov
detection level is approximately 410 V with 200 V class drives. The detection level is approximately 820 V with 400 V class drives.
•
Do a Fault Reset to clear the fault.
•
Parameter
L5-08 [U/OV,OH,GF A-Reset Select]
disables the Auto Restart function.
Code
Name
Causes
Possible Solutions
PF
Input Phase Loss
There is a phase loss in the drive input power.
Correct errors with the wiring for main circuit drive input power.
There is loose wiring in the drive input power
terminals.
Tighten the terminal screws to the correct tightening torque.
The drive input power voltage is changing too
much.
•
Examine the input power for problems.
•
Make the drive input power stable.
•
If the input power supply is good, examine the magnetic
contactor on the main circuit side for problems.
There is unsatisfactory balance between voltage
phases.
•
Examine the input power for problems.
•
Make the drive input power stable.
•
Set
L8-05 = 0 [In PhaseLoss Selection = Disabled]
.
The main circuit capacitors have become
unserviceable.
•
Examine the capacitor maintenance time in monitor
U4-05
[Capacitor Maintenance]
. If
U4-05
is more than 90%, replace
the control board or the drive. For information about replacing
the control board, contact the manufacturer or your nearest
sales representative.
•
If drive input power is correct and the fault stays, replace the
control board or the drive. For information about replacing the
control board, contact the manufacturer or your nearest sales
representative.
Note:
•
The drive detects this error if the DC bus voltage changes irregularly without regeneration.
•
Do a Fault Reset to clear the fault.
•
Use
L8-05
to enable and disable
PF
detection.
Code
Name
Causes
Possible Solutions
PGo
Encoder (PG) Feedback Loss
The encoder cable is disconnected or wired
incorrectly.
Examine for wiring errors or disconnected wires in the encoder
cable, and repair problems.
The encoder is not receiving power.
Examine the encoder power supply.
The holding brake is stopping the motor.
Release the holding brake.
Note:
•
The drive detects this error if it does not receive the speed detection pulse signal from the encoder in the detection time set in
F1-14 [Enc PGOpen Time for Detection]
.
•
Do a Fault Reset to clear the fault.
•
If the drive detects this error, it will operate the motor as specified by the Stopping Method set in
F1-02 [PGOpen Detection Select]
.
Code
Name
Causes
Possible Solutions
PGoH
Encoder (PG) Hardware Fault
The encoder cable is disconnected.
Connect all encoder cable wires.
Note:
•
Do a Fault Reset to clear the fault.
•
If the drive detects this error, it will operate the motor as specified by the Stopping Method set in
F1-02 [PGOpen Detection Select]
.
Содержание Q2A
Страница 2: ...This Page Intentionally Blank 2 SIEPYEUOQ2A01G AC Drive Q2A Technical Manual...
Страница 12: ...12 SIEPYEUOQ2A01G AC Drive Q2A Technical Manual...
Страница 18: ...i 2 Legal Information 18 SIEPYEUOQ2A01G AC Drive Q2A Technical Manual...
Страница 28: ...1 2 Features and Advantages of Control Methods 28 SIEPYEUOQ2A01G AC Drive Q2A Technical Manual...
Страница 64: ...2 9 Installation Methods 64 SIEPYEUOQ2A01G AC Drive Q2A Technical Manual...
Страница 166: ...4 9 Test Run Checklist 166 SIEPYEUOQ2A01G AC Drive Q2A Technical Manual...
Страница 172: ...5 2 European Standards 172 SIEPYEUOQ2A01G AC Drive Q2A Technical Manual...
Страница 173: ...Standards Compliance 5 5 2 European Standards SIEPYEUOQ2A01G AC Drive Q2A Technical Manual 173...
Страница 174: ...5 2 European Standards 174 SIEPYEUOQ2A01G AC Drive Q2A Technical Manual...
Страница 175: ...Standards Compliance 5 5 2 European Standards SIEPYEUOQ2A01G AC Drive Q2A Technical Manual 175...
Страница 176: ...5 2 European Standards 176 SIEPYEUOQ2A01G AC Drive Q2A Technical Manual...
Страница 258: ...6 2 Modbus Communications 258 SIEPYEUOQ2A01G AC Drive Q2A Technical Manual...
Страница 356: ...8 7 Storage Guidelines 356 SIEPYEUOQ2A01G AC Drive Q2A Technical Manual...
Страница 357: ...SIEPYEUOQ2A01G AC Drive Q2A Technical Manual 357 9 Disposal 9 1 Safety Precautions 358 9 2 Disposal Instructions 359...
Страница 360: ...9 2 Disposal Instructions 360 SIEPYEUOQ2A01G AC Drive Q2A Technical Manual...
Страница 526: ...11 20 Parameters Changed by PM Motor Code Selection 526 SIEPYEUOQ2A01G AC Drive Q2A Technical Manual...