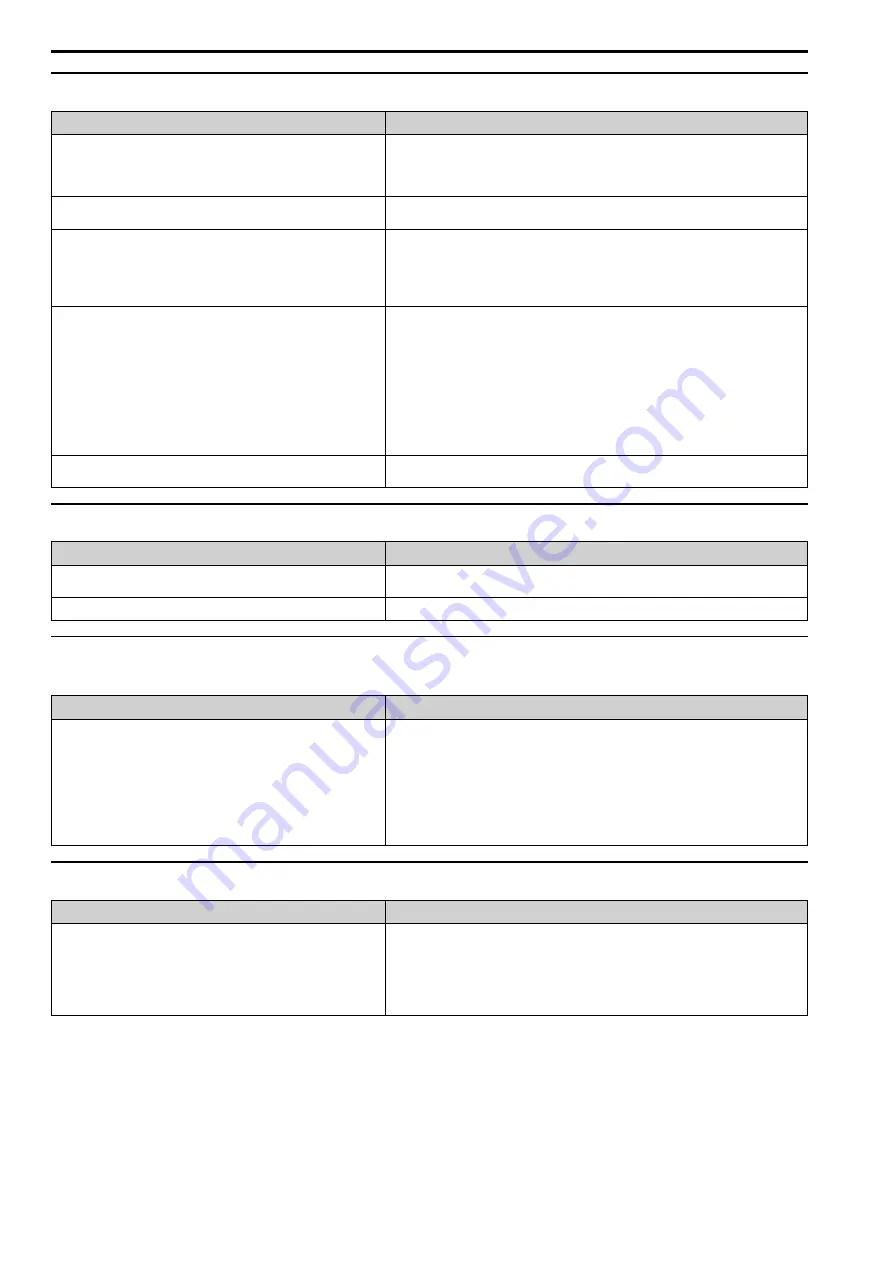
7.10 Troubleshooting Without Fault Display
312
SIEPYEUOQ2A01G AC Drive Q2A Technical Manual
◆
Deceleration Takes Longer Than Expected When Dynamic Braking Is Enabled
Causes
Possible Solutions
The stall prevention during deceleration setting is incorrect.
•
Examine the setting for
L3-04 [StallP@Decel Enable]
.
•
When the drive has a dynamic braking option installed, set
L3-04 = 0 [Disabled]
.
•
If the drive detects
ov [Overvoltage]
, set
L3-04 = 1 [Enabled]
and
L3-50 = 2 [Gen Purpose
w/ DB Resistor]
.
The deceleration time setting is too long.
Set
C1-02, C1-04, C1-06, or C1-08 [Decel Time 1, Decel Time 2, Decel Time 3, or Decel Time 4]
to applicable values.
The motor torque is not sufficient.
Use a larger motor.
Note:
If these items are correct, the demand on the motor is more than the motor capacity:
•
Parameter settings are correct.
•
The drive does not detect
ov [Overvoltage]
.
The drive and motor system reached the torque limit.
•
Examine the values set in
L7-01 to L7-04 [FW Torque Limit to RV Reg. TrqLimit]
and increase
them if necessary.
Note:
If the torque limit is enabled, deceleration time can increase because the drive cannot output
more torque than the limit.
•
If
H3-02, H3-10, H3-06 = 9, B, C, D [AI1 Function Selection, AI2 Function Selection, AI3
Function Selection = Torque Limit]
has been set, examine the settings for the MFAIs.
•
Examine the values set in
H3-02, H3-10, and H3-06
.
•
Use
U1-13, U1-14, and U1-15 [Terminal AI1 Input Lv, Terminal AI2 Input Lv, and
Terminal AI3 Input Lv]
to make sure that the analog input values set to terminals AI1, AI2,
and AI3 are applicable.
The load is more than the internal torque limit as specified by the drive rated
current.
Replace the drive with a larger capacity model.
◆
The Load Falls When a Brake Is Applied
Causes
Possible Solutions
The open/close timing of the brake is incorrect.
Refer to
“
Notes on Controlling the Brake when Using the Hoist Application Preset
”
in the
Technical Manual and take appropriate measures.
The DC injection braking is not sufficient.
Increase the value set in
b2-02 [DCI Braking Current]
.
◆
There Is Audible Noise from the Drive or Motor Cables When the Drive Is
Energized
Causes
Possible Solutions
The relay switching in the drive is making too much noise.
•
Use
C6-02 [Carrier Frequency Selection]
to decrease the carrier frequency.
•
Connect a noise filter to the input side of the drive power supply.
•
Connect a noise filter to the output side of the drive.
•
Isolate the control circuit wiring from the main circuit wiring.
•
Use a metal cable gland to wire the drive.
•
Shield the periphery of the drive with metal.
•
Make sure that the drive and motor are grounded correctly.
•
Make sure that ground faults have not occurred in the wiring or motor.
◆
Residual Current Monitoring/Detection (RCM/RCD) Trips During Run
Causes
Possible Solutions
There is too much leakage current from the drive.
•
Increase the RCM/RCD sensitivity or use RCM/RCD with a higher threshold.
•
Use
C6-02 [Carrier Frequency Selection]
to decrease the carrier frequency.
•
Decrease the length of the cable used between the drive and the motor.
•
Install a noise filter or AC reactor on the output side of the drive. Set
C6-02 = 1 [2.0 kHz]
when connecting an AC reactor.
•
Disable the internal EMC filter.
Содержание Q2A
Страница 2: ...This Page Intentionally Blank 2 SIEPYEUOQ2A01G AC Drive Q2A Technical Manual...
Страница 12: ...12 SIEPYEUOQ2A01G AC Drive Q2A Technical Manual...
Страница 18: ...i 2 Legal Information 18 SIEPYEUOQ2A01G AC Drive Q2A Technical Manual...
Страница 28: ...1 2 Features and Advantages of Control Methods 28 SIEPYEUOQ2A01G AC Drive Q2A Technical Manual...
Страница 64: ...2 9 Installation Methods 64 SIEPYEUOQ2A01G AC Drive Q2A Technical Manual...
Страница 166: ...4 9 Test Run Checklist 166 SIEPYEUOQ2A01G AC Drive Q2A Technical Manual...
Страница 172: ...5 2 European Standards 172 SIEPYEUOQ2A01G AC Drive Q2A Technical Manual...
Страница 173: ...Standards Compliance 5 5 2 European Standards SIEPYEUOQ2A01G AC Drive Q2A Technical Manual 173...
Страница 174: ...5 2 European Standards 174 SIEPYEUOQ2A01G AC Drive Q2A Technical Manual...
Страница 175: ...Standards Compliance 5 5 2 European Standards SIEPYEUOQ2A01G AC Drive Q2A Technical Manual 175...
Страница 176: ...5 2 European Standards 176 SIEPYEUOQ2A01G AC Drive Q2A Technical Manual...
Страница 258: ...6 2 Modbus Communications 258 SIEPYEUOQ2A01G AC Drive Q2A Technical Manual...
Страница 356: ...8 7 Storage Guidelines 356 SIEPYEUOQ2A01G AC Drive Q2A Technical Manual...
Страница 357: ...SIEPYEUOQ2A01G AC Drive Q2A Technical Manual 357 9 Disposal 9 1 Safety Precautions 358 9 2 Disposal Instructions 359...
Страница 360: ...9 2 Disposal Instructions 360 SIEPYEUOQ2A01G AC Drive Q2A Technical Manual...
Страница 526: ...11 20 Parameters Changed by PM Motor Code Selection 526 SIEPYEUOQ2A01G AC Drive Q2A Technical Manual...