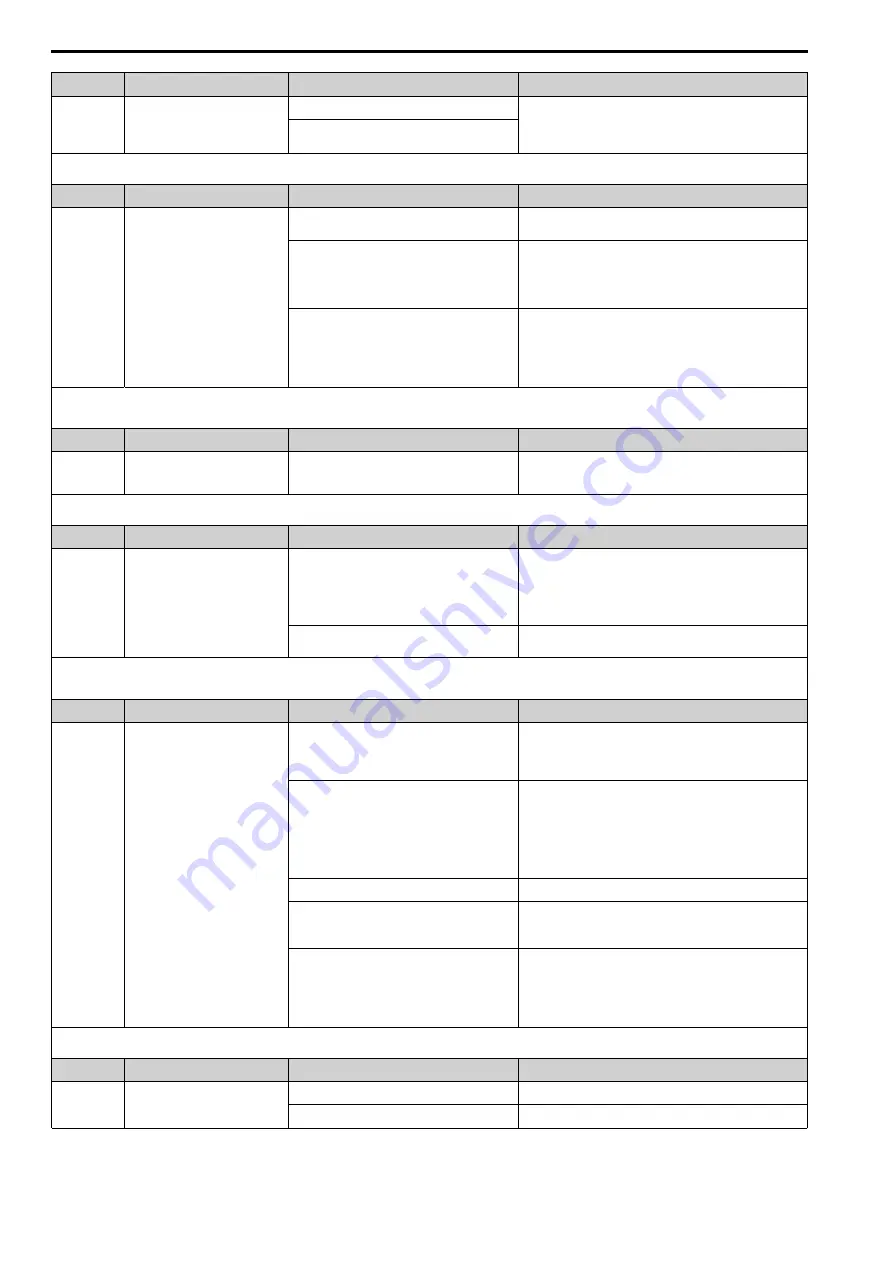
282
SIEPYEUOQ2A01G AC Drive Q2A Technical Manual
Code
Name
Causes
Possible Solutions
rr
Dynamic Braking Transistor Fault
The drive control circuit is damaged.
There is a malfunction in the internal braking
transistor of the drive.
•
Re-energize the drive.
•
If the fault stays, replace the control board or the drive. For
information about replacing the control board, contact the
manufacturer or your nearest sales representative.
Note:
Do a Fault Reset to clear the fault.
Code
Name
Causes
Possible Solutions
SC
Short Circuit/IGBT Failure
Overheating caused damage to the motor or the
motor insulation is not satisfactory.
Measure the motor insulation resistance, and replace the motor if
there is electrical conduction or unserviceable insulation.
The motor main circuit cable is contacting ground
to make a short circuit.
•
Examine the motor main circuit cable for damage, and repair
short circuits.
•
Measure the resistance between the motor main circuit cable
and the ground terminal. If there is electrical conduction,
replace the cable.
A short circuit or ground fault on the drive output
side caused damage to the output transistor of the
drive.
•
Make sure that there is not a short circuit in terminal B1 and
terminals U/T1, V/T2, and W/T3. Make sure that there is not a
short circuit in terminals - and terminals U/T1, V/T2, and W/
T3.
•
If there is a short circuit, contact the manufacturer or your
nearest sales representative.
Note:
•
The drive detects this error if there is a short circuit or ground fault on the drive output side, or an IGBT failure.
•
Do a Fault Reset to clear the fault.
Code
Name
Causes
Possible Solutions
SCF
Safety Circuit Fault
The safety circuit is broken.
Replace the control board or the drive. For information about
replacing the control board, contact the manufacturer or your
nearest sales representative.
Note:
Do a Fault Reset to clear the fault.
Code
Name
Causes
Possible Solutions
SEr
Speed Search Retries Exceeded
The speed search-related parameters are set
incorrectly.
•
Decrease the value set in
b3-10 [Speed Det Gain for
Estimation]
.
•
Increase the value set in
b3-17 [Speed Retry Current Level]
.
•
Increase the value set in
b3-18 [Speed Retry Delay]
.
•
Do Auto-Tuning again.
The motor is coasting in the opposite direction of
the Run command.
Set
b3-14 = 1 [Speed Bi-Directional Search = Enabled]
.
Note:
•
The drive detects this error if the number of speed search restarts is more than the value set in
b3-19 [Speed Retry Times]
.
•
Do a Fault Reset to clear the fault.
Code
Name
Causes
Possible Solutions
STPo
Motor Step-Out Detected
The motor code is set incorrectly for PM Control
Methods.
•
Enter the correct motor code to
E5-01 [PM Mot Code
Selection]
as specified by the PM motor.
•
For specialized motors, refer to the motor test report and set
E5-xx
correctly.
The load is too heavy.
•
Increase the value set in
n8-55 [Load Inertia]
.
•
Increase the value set in
n8-51 [Ac/Dec Pull-In Current]
. If the
drive detects
STPo
during deceleration when increasing the
value set in
n8-51
, set the value of
n8-79 [Pull-In
Curr@Deceleration]
lower than
n8-51
.
•
Decrease the load.
•
Replace the drive and motor with larger capacity models.
The load inertia is too heavy.
Increase the value set in
n8-55
.
The acceleration/deceleration times are too short.
•
Increase the acceleration/deceleration times set in
C1-01 to
C1-08 [Accel Time 1 to Decel Time 4]
.
•
Increase the value set in
C2-01 [Jerk@Start of Accel]
.
Speed response is too slow.
•
Increase the value set in
n8-55
.
•
If
STPo
occurs in Normal Duty mode when
A1-02 = 6
[Control Method = PM AOLVector]
, increase the value set in
n8-11 [Observ.Calc Gain2]
in increments of 10. If
STPo
occurs when starting a motor, decrease the value set in
n8-11
in
increments of 10.
Note:
Do a Fault Reset to clear the fault.
Code
Name
Causes
Possible Solutions
SvE
Zero Servo Fault
The value set in the torque limit is too small.
Adjust torque limit-related parameters
L7-01 to L7-04
.
The load torque is too large.
Decrease the load torque.
Содержание Q2A
Страница 2: ...This Page Intentionally Blank 2 SIEPYEUOQ2A01G AC Drive Q2A Technical Manual...
Страница 12: ...12 SIEPYEUOQ2A01G AC Drive Q2A Technical Manual...
Страница 18: ...i 2 Legal Information 18 SIEPYEUOQ2A01G AC Drive Q2A Technical Manual...
Страница 28: ...1 2 Features and Advantages of Control Methods 28 SIEPYEUOQ2A01G AC Drive Q2A Technical Manual...
Страница 64: ...2 9 Installation Methods 64 SIEPYEUOQ2A01G AC Drive Q2A Technical Manual...
Страница 166: ...4 9 Test Run Checklist 166 SIEPYEUOQ2A01G AC Drive Q2A Technical Manual...
Страница 172: ...5 2 European Standards 172 SIEPYEUOQ2A01G AC Drive Q2A Technical Manual...
Страница 173: ...Standards Compliance 5 5 2 European Standards SIEPYEUOQ2A01G AC Drive Q2A Technical Manual 173...
Страница 174: ...5 2 European Standards 174 SIEPYEUOQ2A01G AC Drive Q2A Technical Manual...
Страница 175: ...Standards Compliance 5 5 2 European Standards SIEPYEUOQ2A01G AC Drive Q2A Technical Manual 175...
Страница 176: ...5 2 European Standards 176 SIEPYEUOQ2A01G AC Drive Q2A Technical Manual...
Страница 258: ...6 2 Modbus Communications 258 SIEPYEUOQ2A01G AC Drive Q2A Technical Manual...
Страница 356: ...8 7 Storage Guidelines 356 SIEPYEUOQ2A01G AC Drive Q2A Technical Manual...
Страница 357: ...SIEPYEUOQ2A01G AC Drive Q2A Technical Manual 357 9 Disposal 9 1 Safety Precautions 358 9 2 Disposal Instructions 359...
Страница 360: ...9 2 Disposal Instructions 360 SIEPYEUOQ2A01G AC Drive Q2A Technical Manual...
Страница 526: ...11 20 Parameters Changed by PM Motor Code Selection 526 SIEPYEUOQ2A01G AC Drive Q2A Technical Manual...