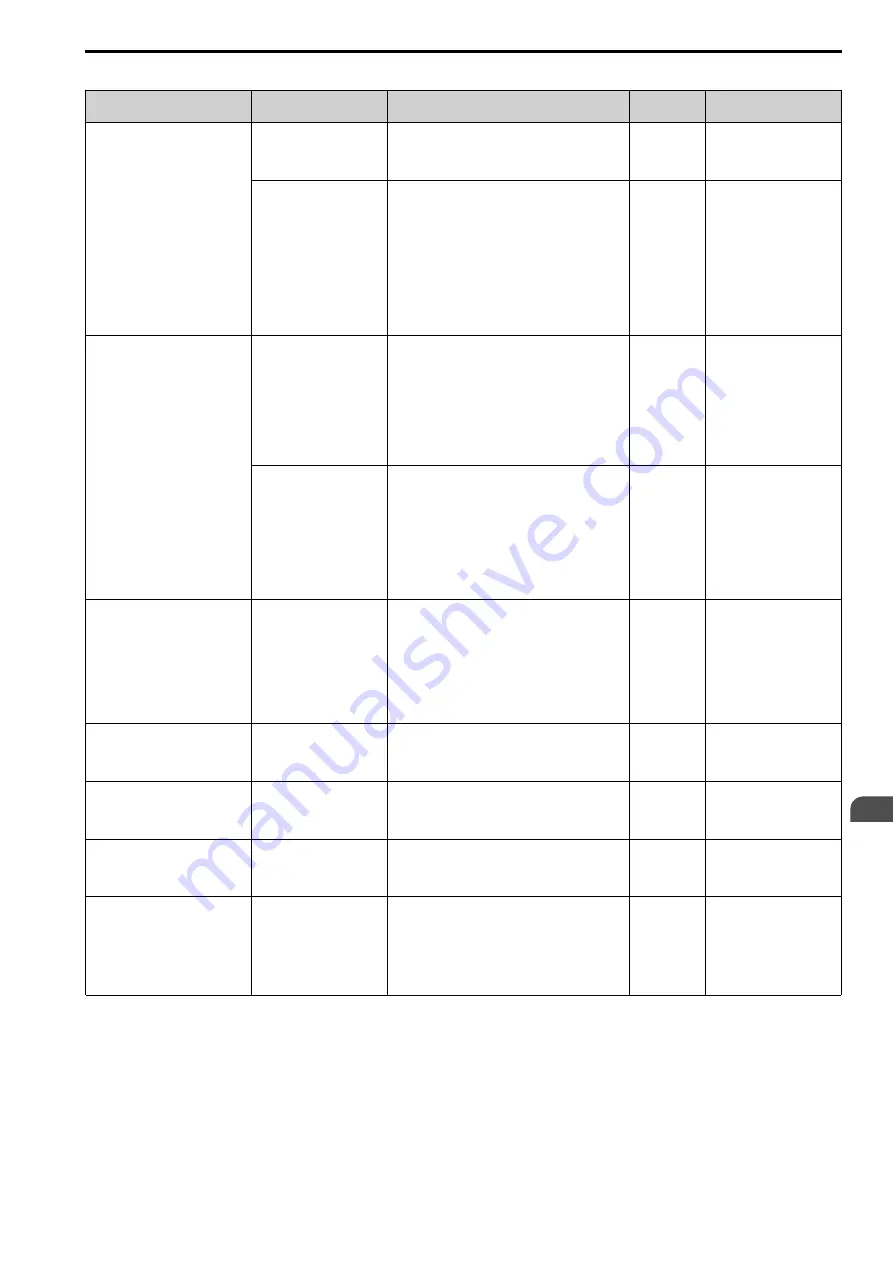
4.8 Fine Tuning during Test Runs (Adjust the Control Function)
SIEPYEUOQ2A01G AC Drive Q2A Technical Manual
159
Table 4.18 Parameters for Fine Tuning the Drive (Open Loop Vector Control Method)
Issue
Parameter Number
Solution
Default
Setting
Recommended Setting
•
Torque or speed response are
slow.
•
Hunting or oscillation at mid-
range speeds (10 Hz to 40 Hz)
n2-01 [AFR Gain]
•
To increase the speed of torque or speed response,
decrease the setting value in increments of 0.05.
•
If hunting or oscillation occur, decrease the setting
value in increments of 0.05.
1.00
0.50 - 2.00
n2-02 [AFR Time 1]
•
To increase the speed of torque or speed response,
decrease the setting value in increments of 10 ms
and examine the response.
•
If hunting or oscillation occur or if the load inertia is
too much, increase the setting value in increments of
50 ms and examine the response.
Note:
Make sure that this parameter setting is:
n2-02 ≤
n2-03 [AFR Time 2]
holds true.
When you adjust
n2-02
, you must also increase
the
C4-02 [Trq Comp Delay Time]
value by the
same ratio.
50 ms
50 - 2000 ms
ov [overvoltage]
occurs when the
drive stops accelerating, starts to
decelerate, or when there are large
changes in the load.
n2-03 [AFR Time 2]
•
If
ov
occurs, increase the setting value in increments
of 50 ms and examine the response.
•
If the response is not sufficient, decrease the setting
value in increments of 10 ms and examine the
response.
Note:
Make sure that this parameter setting is:
n2-02
[AFR Time 1] ≤ n2-03
. When you adjust
n2-03
you
must also increase the
C4-06 [M2 Trq Comp Delay
Time]
value by the same ratio.
750 ms
750 - 2000 ms
C4-06 [M2 Trq Comp Delay
Time]
•
If
ov
occurs, increase the setting value in increments
of 10 ms and examine the response.
•
If the response is not sufficient, decrease the setting
value in increments of 2 ms and examine the
response.
Note:
Make sure that this parameter setting is:
C4-02 [Trq
Comp Delay Time] ≤ C4-06
.
When you adjust
C4-06
, you must also increase the
n2-03 [AFR Time 2]
value by the same ratio.
150 ms
150 - 750 ms
•
Torque or speed response are
slow.
•
Hunting or oscillation
C4-02 [Trq Comp Delay
Time]
•
If torque or speed response are slow, decrease the
setting value in increments of 2 ms.
•
If hunting or oscillation occur, increase the setting
value in increments of 10 ms.
Note:
Make sure that this parameter setting is:
C4-02 ≤
C4-06 M2 Trq Comp Delay Time
.
When you adjust
C4-02
, you must also increase the
n2-02 AFR Time 1
value by the same ratio.
20 ms
20 - 100 ms
•
Speed response is slow.
•
Speed is not stable.
C3-02 [Slip Comp Delay
Time]
•
If speed response is slow, decrease the setting value
in increments of 10 ms.
•
If speed is not stable, increase the value in
increments of 10 ms.
200 ms
100 - 500 ms
Speed precision is unsatisfactory.
C3-01 [Slip Comp Gain]
•
If speed is too slow, increase the setting value in
increments of 0.1.
•
If speed is too fast, decrease the setting value in
increments of 0.1.
0.5 - 1.5
•
The volume of the motor
excitation sound is too high.
•
Hunting or oscillation at low
speeds (10 Hz or lower)
C6-02 [Carrier Frequency
Selection]
•
If the volume of the motor excitation sound is too
high, increase the carrier frequency.
•
If hunting or oscillation occur at low speeds,
decrease the carrier frequency.
1 (2 kHz)
0 to upper limit value
•
Torque at low speeds (10 Hz or
lower) is not sufficient. speed
response is slow.
•
Speed response is slow.
•
Large initial vibration at start up.
•
E1-08 [Mid A Voltage]
•
E1-10 [Min Output
Voltage]
•
If torque or speed response are slow, increase the
setting value.
•
If there is large initial vibration at start up, decrease
the setting value
Note:
If the setting value is set too high, a large torque
reference may be output even with light loads.
•
E1-08: 11.0
•
E1-10: 2.0
Default s/- 2 V
*1
Default value changes when
A1-02 [Control Method]
and
o2-04 [Drive KVA Selection]
values change.
*2
Default value changes when
A1-02 [Control Method]
and
E1-03 [V/f Pattern Selection]
values change.
*3
Default value changes when
Drive KVA Selection
and
ND/HD Duty Selection
values change.
*4
Recommended settings are for 200 V class drives. Multiply the voltage by 2 for 400 V class drives.
Содержание Q2A
Страница 2: ...This Page Intentionally Blank 2 SIEPYEUOQ2A01G AC Drive Q2A Technical Manual...
Страница 12: ...12 SIEPYEUOQ2A01G AC Drive Q2A Technical Manual...
Страница 18: ...i 2 Legal Information 18 SIEPYEUOQ2A01G AC Drive Q2A Technical Manual...
Страница 28: ...1 2 Features and Advantages of Control Methods 28 SIEPYEUOQ2A01G AC Drive Q2A Technical Manual...
Страница 64: ...2 9 Installation Methods 64 SIEPYEUOQ2A01G AC Drive Q2A Technical Manual...
Страница 166: ...4 9 Test Run Checklist 166 SIEPYEUOQ2A01G AC Drive Q2A Technical Manual...
Страница 172: ...5 2 European Standards 172 SIEPYEUOQ2A01G AC Drive Q2A Technical Manual...
Страница 173: ...Standards Compliance 5 5 2 European Standards SIEPYEUOQ2A01G AC Drive Q2A Technical Manual 173...
Страница 174: ...5 2 European Standards 174 SIEPYEUOQ2A01G AC Drive Q2A Technical Manual...
Страница 175: ...Standards Compliance 5 5 2 European Standards SIEPYEUOQ2A01G AC Drive Q2A Technical Manual 175...
Страница 176: ...5 2 European Standards 176 SIEPYEUOQ2A01G AC Drive Q2A Technical Manual...
Страница 258: ...6 2 Modbus Communications 258 SIEPYEUOQ2A01G AC Drive Q2A Technical Manual...
Страница 356: ...8 7 Storage Guidelines 356 SIEPYEUOQ2A01G AC Drive Q2A Technical Manual...
Страница 357: ...SIEPYEUOQ2A01G AC Drive Q2A Technical Manual 357 9 Disposal 9 1 Safety Precautions 358 9 2 Disposal Instructions 359...
Страница 360: ...9 2 Disposal Instructions 360 SIEPYEUOQ2A01G AC Drive Q2A Technical Manual...
Страница 526: ...11 20 Parameters Changed by PM Motor Code Selection 526 SIEPYEUOQ2A01G AC Drive Q2A Technical Manual...