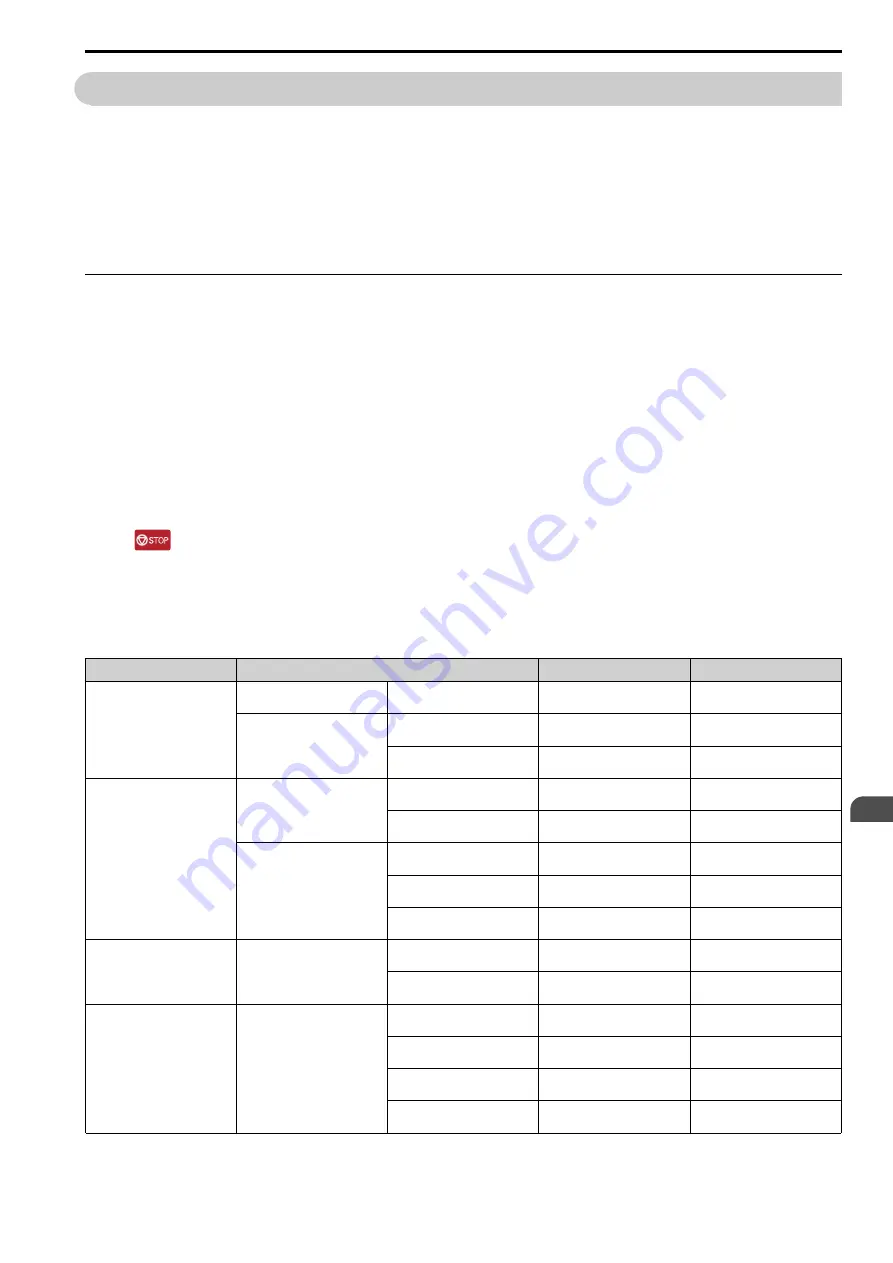
SIEPYEUOQ2A01G AC Drive Q2A Technical Manual
147
4.6
Auto-Tuning
Auto-Tuning uses motor characteristics to automatically set drive parameters for vector control. Think about the
type of motor, drive control method, and the motor installation environment and select the best Auto-Tuning
method.
The keypad will show the messages with prompts to input the necessary parameter information. These prompts
are specified by the selected Auto-Tuning method and the control method setting in
A1-02 [Control Method]
.
WARNING!
Crush Hazard. Rotational Auto-Tuning rotates the motor at a frequency that is 50% or more of the rated frequency
of the motor. Make sure that there are no issues related to safety in the area around the drive and motor. Failure to obey can
cause death or serious injury and damage to machinery.
◆
Precautions before Auto-Tuning
Examine the topics in this section before you start Auto-Tuning.
■
Prepare for Basic Auto-Tuning
•
You must input data from the motor nameplate or motor test report to do Auto-Tuning. Make sure that this data
is available before Auto-Tuning the drive.
•
For best performance, make sure that the drive input supply voltage is equal to or more than the motor rated
voltage.
Note:
Better performance is possible when you use a motor with a base voltage that is less than the input supply voltage (20 V for 200 V class
models and 40 V for 400 V class models). This is very important when operating the motor at more than 90% of base speed, where high
torque precision is necessary. If the input power supply is equal to the motor rated voltage, the drive output voltage will not be sufficient,
and performance will decrease.
•
Push
on the keypad to cancel Auto-Tuning.
•
If a Safe Disable input signal is input to the drive during Auto-Tuning, Auto-Tuning measurements will not
complete successfully. If this occurs, cancel the Auto-Tuning, then do it again.
•
The following table gives information about the terminal operations of digital inputs and outputs during Auto-
Tuning.
Table 4.6 Status of Input/Output Terminals during Auto-Tuning
Auto-Tuning Type
Mode
Digital Input
Digital Output
Induction Motor Auto-Tuning
Rotational
Rotational Auto-Tuning
Disabled
Functions the same as during
usual operation.
Stationary
Stationary Auto-Tuning
Disabled
Keeps the status at the start of
Auto-Tuning.
Stationary Auto-Tuning for Line-
to-Line Resistance
Disabled
Keeps the status at the start of
Auto-Tuning.
PM Motor Auto-Tuning
Rotational
Z-Pulse Offset Tuning
Disabled
Functions the same as during
usual operation.
PM Rotational Auto-Tuning
Disabled
Functions the same as during
usual operation.
Stationary
PM Motor Parameter Settings
Disabled
Keeps the status at the start of
Auto-Tuning.
PM Stationary Auto-Tuning
Disabled
Keeps the status at the start of
Auto-Tuning.
PM Stationary Auto-Tuning for
Stator Resistance
Disabled
Keeps the status at the start of
Auto-Tuning.
EZ Tuning
Stationary
Motor Parameter Setting
Disabled
Keeps the status at the start of
Auto-Tuning.
Stationary Auto-Tuning for Line-
to-Line Resistance
Disabled
Keeps the status at the start of
Auto-Tuning.
ASR and Inertia Tuning
Rotational
Inertia Tuning
Disabled
Functions the same as during
usual operation.
ASR Tuning
Disabled
Functions the same as during
usual operation.
Deceleration Rate Tuning
Disabled
Functions the same as during
usual operation.
KEB Tuning
Disabled
Functions the same as during
usual operation.
*1
A terminal to which
H2-xx = 3 [H2-xx: MFDO Function Select = Fault]
is assigned functions the same as during usual operation.
*2
In software versions PRG: 23011 and older, the output keeps the status at start of Auto-Tuning.
Содержание Q2A
Страница 2: ...This Page Intentionally Blank 2 SIEPYEUOQ2A01G AC Drive Q2A Technical Manual...
Страница 12: ...12 SIEPYEUOQ2A01G AC Drive Q2A Technical Manual...
Страница 18: ...i 2 Legal Information 18 SIEPYEUOQ2A01G AC Drive Q2A Technical Manual...
Страница 28: ...1 2 Features and Advantages of Control Methods 28 SIEPYEUOQ2A01G AC Drive Q2A Technical Manual...
Страница 64: ...2 9 Installation Methods 64 SIEPYEUOQ2A01G AC Drive Q2A Technical Manual...
Страница 166: ...4 9 Test Run Checklist 166 SIEPYEUOQ2A01G AC Drive Q2A Technical Manual...
Страница 172: ...5 2 European Standards 172 SIEPYEUOQ2A01G AC Drive Q2A Technical Manual...
Страница 173: ...Standards Compliance 5 5 2 European Standards SIEPYEUOQ2A01G AC Drive Q2A Technical Manual 173...
Страница 174: ...5 2 European Standards 174 SIEPYEUOQ2A01G AC Drive Q2A Technical Manual...
Страница 175: ...Standards Compliance 5 5 2 European Standards SIEPYEUOQ2A01G AC Drive Q2A Technical Manual 175...
Страница 176: ...5 2 European Standards 176 SIEPYEUOQ2A01G AC Drive Q2A Technical Manual...
Страница 258: ...6 2 Modbus Communications 258 SIEPYEUOQ2A01G AC Drive Q2A Technical Manual...
Страница 356: ...8 7 Storage Guidelines 356 SIEPYEUOQ2A01G AC Drive Q2A Technical Manual...
Страница 357: ...SIEPYEUOQ2A01G AC Drive Q2A Technical Manual 357 9 Disposal 9 1 Safety Precautions 358 9 2 Disposal Instructions 359...
Страница 360: ...9 2 Disposal Instructions 360 SIEPYEUOQ2A01G AC Drive Q2A Technical Manual...
Страница 526: ...11 20 Parameters Changed by PM Motor Code Selection 526 SIEPYEUOQ2A01G AC Drive Q2A Technical Manual...