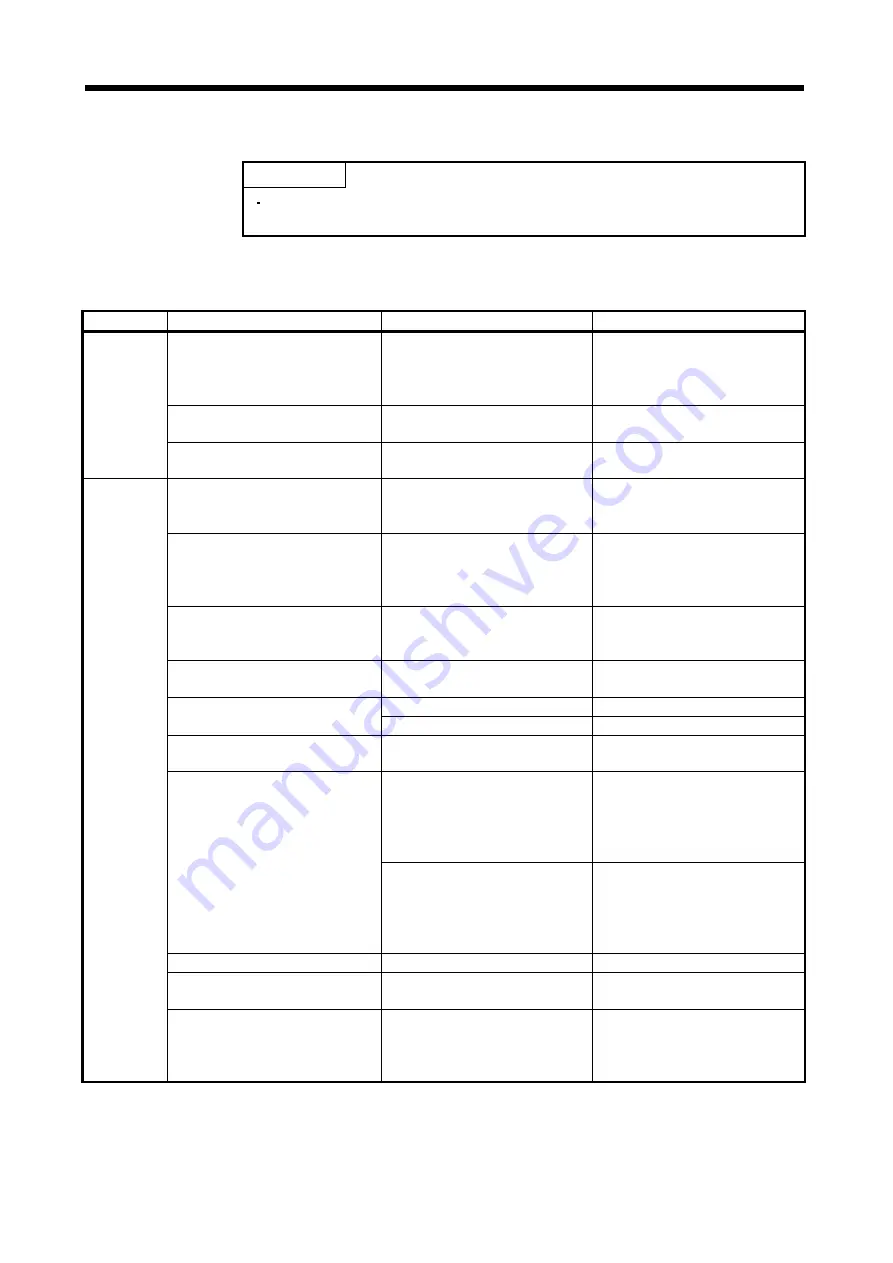
16 - 123
16. INDEXER POSITIONING OPERATION
16.12.6 Trouble which does not trigger an alarm/warning
POINT
When the servo amplifier, servo motor, or encoder malfunctions, the following
status may occur.
The following example shows possible causes which do not trigger alarm or warning. Remove each cause by
referring to this section.
Description
Check method
Possible cause
Action
The LED
display
disappears.
When the display is turned on by
disconnecting all connectors except
the power supply, check if the
disconnected wires are shorted.
The external I/O terminal is shorted.
Check the wiring of I/O signals.
Check if the control circuit power
supply of the servo amplifier is off.
The control circuit power supply is not
applied.
Turn on the control circuit power
supply.
Check if the voltage of the control
circuit power supply dropped.
The voltage of the control circuit
power supply has dropped.
Set the control circuit power supply
voltage within the rated range.
The servo
motor does
not operate.
Check if warning (A99) is occurring.
Forward rotation stroke end (LSP)
and reverse rotation stroke end (LSN)
are not on.
Switch on the forward rotation stroke
end (LSP) and reverse rotation stroke
end (LSN).
Check the connection of the servo
motor.
The output terminals (U, V, W) of the
servo amplifier do not match the input
terminals (U, V, W) of the servo
motor.
Connect each phase of the U, V, and
W correctly.
Check if warning (AE9) is occurring.
The servo-on was turned on while the
main circuit power of servo amplifier
is off.
Turn on the main circuit power
supply.
Check if a servo alarm or warning is
occurring.
A servo alarm occurred.
Check the alarm content and remove
its cause.
Check the on/off state of servo-on and
reset.
Servo-on is off.
Turn on servo-on.
Reset is on.
Turn off reset.
Check the setting of parameter
No.PA01 (control mode).
The setting of parameter No.PA01
(control mode) is incorrect.
Check the setting of parameter
No.PA01 (control mode).
Check if the generated torque
exceeds the torque limit value.
1. Check the "instantaneous torque" in
the status display.
2. Check the torque ripple with the
"Graph" command of "Monitor"
menu on MR Configurator.
1. The maximum torque is insufficient.
Servo capacity is insufficient or load
is too large.
1. Reduce the load by changing the
mass and shape of work.
2. Reduce the effective load ratio by
increasing
acceleration/deceleration time.
2. An unintended torque limit is
enabled. Or the setting of the torque
limit is 0 (no torque is generated).
(Set with Parameter PA11, PA12,
PC35)
Review the torque limit setting.
Check the point table setting.
The setting of point tables is incorrect. Review the point table setting.
Check if the load side is interfering.
The load side is interfering with the
servo motor.
Remove the interference of the load
side.
For a servo motor with an
electromagnetic brake, check the
power supply of the electromagnetic
brake.
The electromagnetic brake has not
been released.
Turn on the power supply of the
electromagnetic brake, and release
the electromagnetic brake.
Содержание Melservo-J3 Series MR-J3-B
Страница 19: ...10 MEMO ...
Страница 55: ...1 36 1 FUNCTIONS AND CONFIGURATION MEMO ...
Страница 61: ...2 6 2 INSTALLATION MEMO ...
Страница 179: ...4 58 4 SIGNALS AND WIRING MEMO ...
Страница 241: ...5 62 5 OPERATION MEMO ...
Страница 357: ...10 16 10 SPECIAL ADJUSTMENT FUNCTIONS MEMO ...
Страница 385: ...11 28 11 TROUBLESHOOTING MEMO ...
Страница 397: ...12 12 12 OUTLINE DRAWINGS MEMO ...
Страница 755: ...17 70 17 SPEED CONTROL OPERATION MEMO ...
Страница 793: ...App 38 APPENDIX MEMO ...
Страница 799: ...MEMO ...