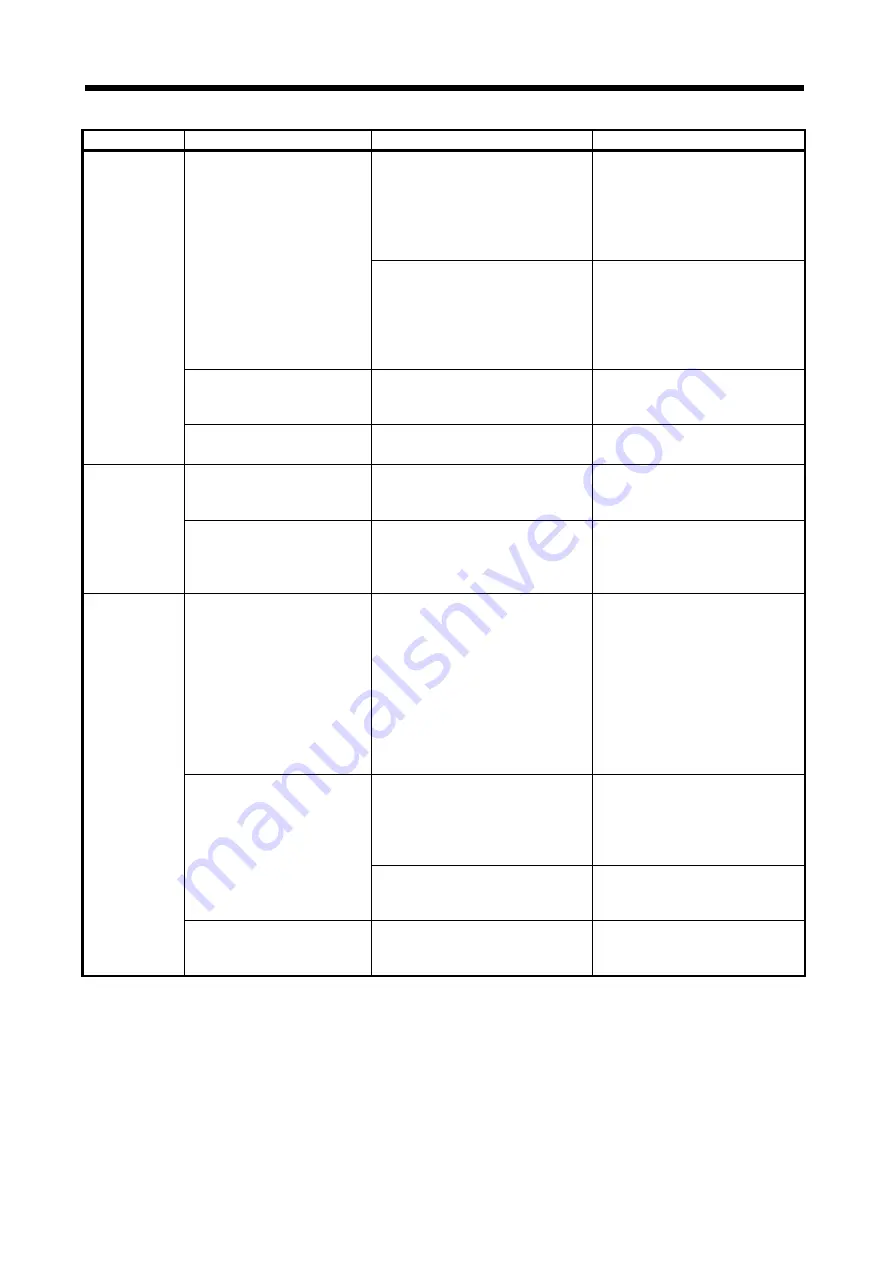
11 - 26
11. TROUBLESHOOTING
Description
Check method
Possible cause
Action
The position
deviates during
operation after
the home
position return.
The input value from the manual
pulse generator MR-HDP01 and
the command position (mm) do
not match.
Wiring or multiplication setting
(parameter No.PA05, manual pulse
generator multiplication 1 (TP1) and
manual pulse generator multiplication 2
(TP2)) of the manual pulse generator is
incorrect.
1. Check the wiring.
2. Check if multiplication setting is set
correctly.
1. Command input pulses are
miscounted by noises.
2. Shielding the command cable is
faulty.
3. The command cable has a contact
failure or disconnected.
Check the shield procedure of the
command cable.
The command from the controller
and the command position of the
amplifier do not match.
Communication command error.
(An unintended command is inputted).
Review the controller programs and
protocol.
(Refer to chapter 3.)
Check the in-position range
(parameter No.PA10).
The in-position range is too large.
Set a narrower in-position range.
In absolute
position detection
system, a
restored position
deviates at power
restoration.
For the geared servo motor,
check the setting of the electronic
gear (parameter No.PA06, PA07).
The reduction ratio is not calculated
correctly.
Review the setting of the reduction
ratio.
For positioning operation after the
home position return, the position
mismatch does not occur.
The maximum speed (3000r/min) at a
power failure was exceeded during
servo amplifier power-off.
Review the machine configuration so
that the servo motor will not rotate at
speed of 3000r/min or higher during
power-off.
Overshoot/
undershoot
occurs.
1. Check the velocity waveform
with “Graph” command of
"Monitor" menu on MR
Configurator, and check if
overshoot/undershoot is
occurring.
2. If the servo motor can be driven
safely, repeat acceleration and
deceleration three times or
more to complete auto tuning.
1. The servo gain is low or too high.
2. The auto tuning response is low or too
high.
Adjust the auto tuning response, and
readjust the gain. (Refer to chapter 9.)
Check if the maximum torque
exceeds the torque limit value.
1. Check the "instantaneous
torque" in the status display.
2. Check the torque ripple with
“Graph” command of "Monitor"
menu on MR Configurator.
The maximum torque is insufficient.
1. Shortage of servo capacity.
2. Too large load.
1. Reduce the load by changing the
mass and shape of work.
2. Reduce the effective load ratio by
increasing acceleration/deceleration
time.
The setting of the torque limit is
incorrect. (Set with parameter
No.PA11/PA12/PC35)
Review the torque limit setting.
Check if there is a backlash on
the machine part.
There is a backlash between the servo
motor and the machine (such as a gear
and coupling).
Adjust the backlash on the coupling
and the machine part.
Содержание Melservo-J3 Series MR-J3-B
Страница 19: ...10 MEMO ...
Страница 55: ...1 36 1 FUNCTIONS AND CONFIGURATION MEMO ...
Страница 61: ...2 6 2 INSTALLATION MEMO ...
Страница 179: ...4 58 4 SIGNALS AND WIRING MEMO ...
Страница 241: ...5 62 5 OPERATION MEMO ...
Страница 357: ...10 16 10 SPECIAL ADJUSTMENT FUNCTIONS MEMO ...
Страница 385: ...11 28 11 TROUBLESHOOTING MEMO ...
Страница 397: ...12 12 12 OUTLINE DRAWINGS MEMO ...
Страница 755: ...17 70 17 SPEED CONTROL OPERATION MEMO ...
Страница 793: ...App 38 APPENDIX MEMO ...
Страница 799: ...MEMO ...