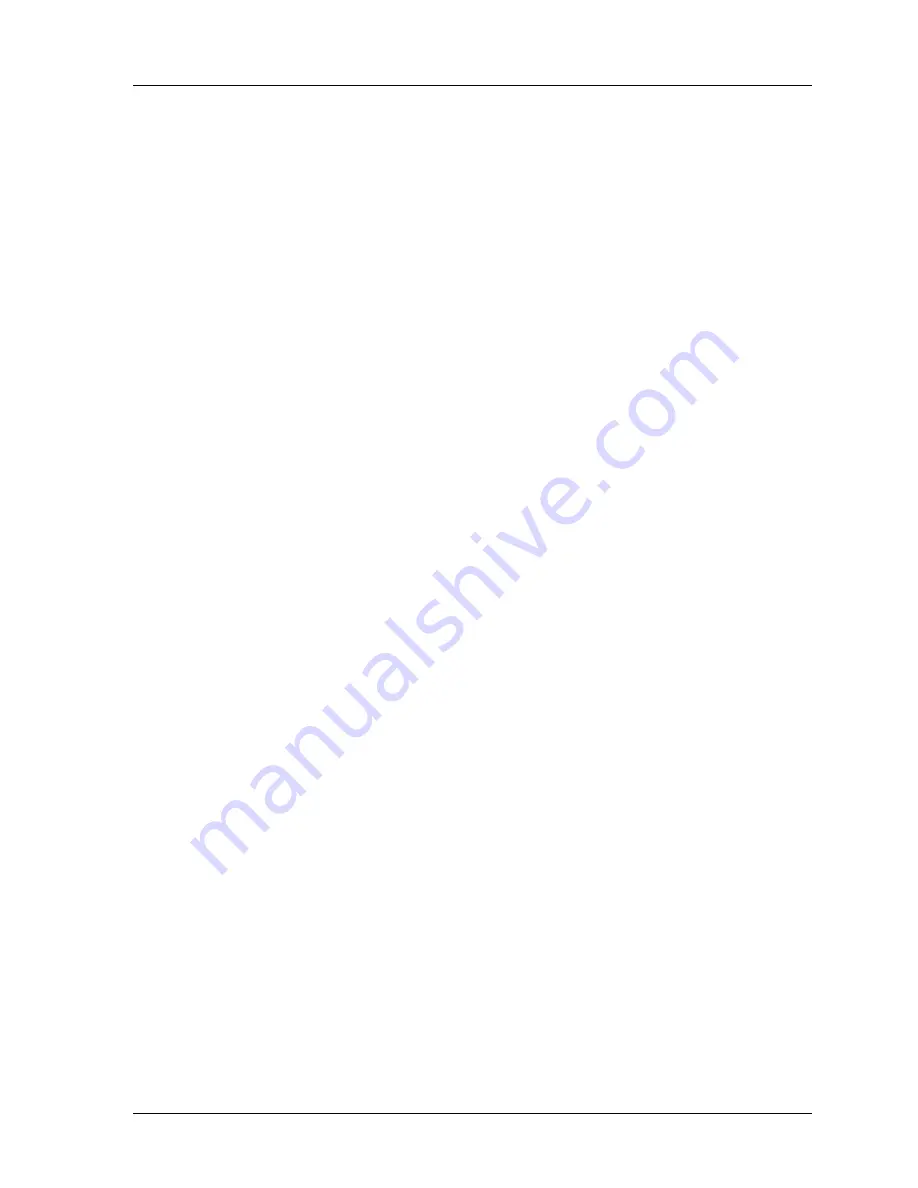
SmartPAC 2 with WPC Integration
1126800
Introduction to SmartPAC 2
Chapter 1
page 13
Impedance
The term
impedance
refers to the opposition to the flow of electric current. Some die
protection controls have inputs with different impedances for electromechanical sensors. As
a rule of thumb, use a high-impedance input if the part is dirty or covered with a non-
conductive lubricant. Use a low-impedance input if the part is covered with a water-based or
conductive lubricant.
An optional "low impedance" 16-channel DiProPAC module (#9632904) is available. This
option is necessary when wire probes depend upon a part/strip to complete the circuit, and
the part/strip is covered with a water-based conductive lubricant. If you decide that you
require this option rather than the standard DiProPAC, contact Wintriss Controls
immediately to order that part,
before installing DiProPAC
(discussed in Chapter 2).
Sensor Types
Sensors used with die protection systems are classified as red, yellow, or green. For
SmartPAC 2 with DiProPAC, there are four types of green sensors—green, green quick
check, green constant, and green special—all of which require something to happen on every
stroke, or at least once during a set number of strokes.
When you make settings for a tool, you select the sensor type for each sensor connected to
SmartPAC 2's sensor inputs. You can have any combination of reds, yellows, or greens for a
tool. You will see how to select sensor type in Chapter 5 where you learn how to make
sensor settings. Here we discuss what each type means.
Yellow sensors
Yellow sensors are normally open to ground. They are ideally suited to monitor events like
stock buckling, end of stock, or die overload. SmartPAC 2 sends a stop command to the
press as soon as the sensor actuates. The stop type can be set for either an emergency, top
stop, or Smart Stop (see "Considerations for setting sensor stop type" below). Because
yellow sensors work independent of the crankshaft angle and do not actuate every stroke like
green sensors, you do not set a ready signal for yellow sensors.
Red sensors
Red sensors are normally closed to ground. SmartPAC 2 sends a stop command to the press
— either top stop, emergency stop, or Smart Stop (see "Considerations for setting sensor stop
type" below) — as soon as the sensor opens (actuates). Red sensors are used where it is
more convenient to use a normally closed sensor instead of a normally open one. Red
sensors can monitor the same types of events as yellow sensors—die overload, end of stock,
buckling, etc. No ready signal is set for red sensors.
Содержание SmartPAC 2
Страница 192: ...1126800 SmartPAC 2 with WPC Integration Page 170 Chapter 2 Installing SmartPAC 2 and WPC ...
Страница 222: ...1126800 SmartPAC 2 with WPC Integration Page 200 Chapter 3 SmartPAC 2 Keyboard Displays and Operating Modes ...
Страница 294: ...1126800 SmartPAC 2 with WPC Integration Page 272 Chapter 4 SmartPAC 2 Initialization Mode ...
Страница 342: ...1126800 SmartPAC 2 with WPC Integration page 320 Chapter 5 SmartPAC 2 Program Mode ...
Страница 404: ...1126800 SmartPAC 2 with WPC Integration Page 382 Chapter 6 SmartPAC 2 Run Mode ...
Страница 448: ...1126800 SmartPAC 2 with WPC Integration Page 426 Chapter 7 SmartPAC 2 Fault Messages ...
Страница 476: ...1126800 SmartPAC 2 with WPC Integration page 454 Appendix C Updating SmartPAC 2 Firmware ...
Страница 478: ...1126800 SmartPAC 2 with WPC Integration page 456 Appendix D SmartView Remote Viewing and E mail Setup ...
Страница 480: ...1126800 SmartPAC 2 with WPC Integration page 458 Appendix E Upgrade from Original SmartPAC to SmartPAC 2 ...
Страница 482: ...1126800 SmartPAC 2 with WPC Integration page 460 Appendix F Replacing SmartPAC 2 PC Board ...
Страница 492: ...1126800 SmartPAC 2 with WPC Integration page 470 Glossary ...