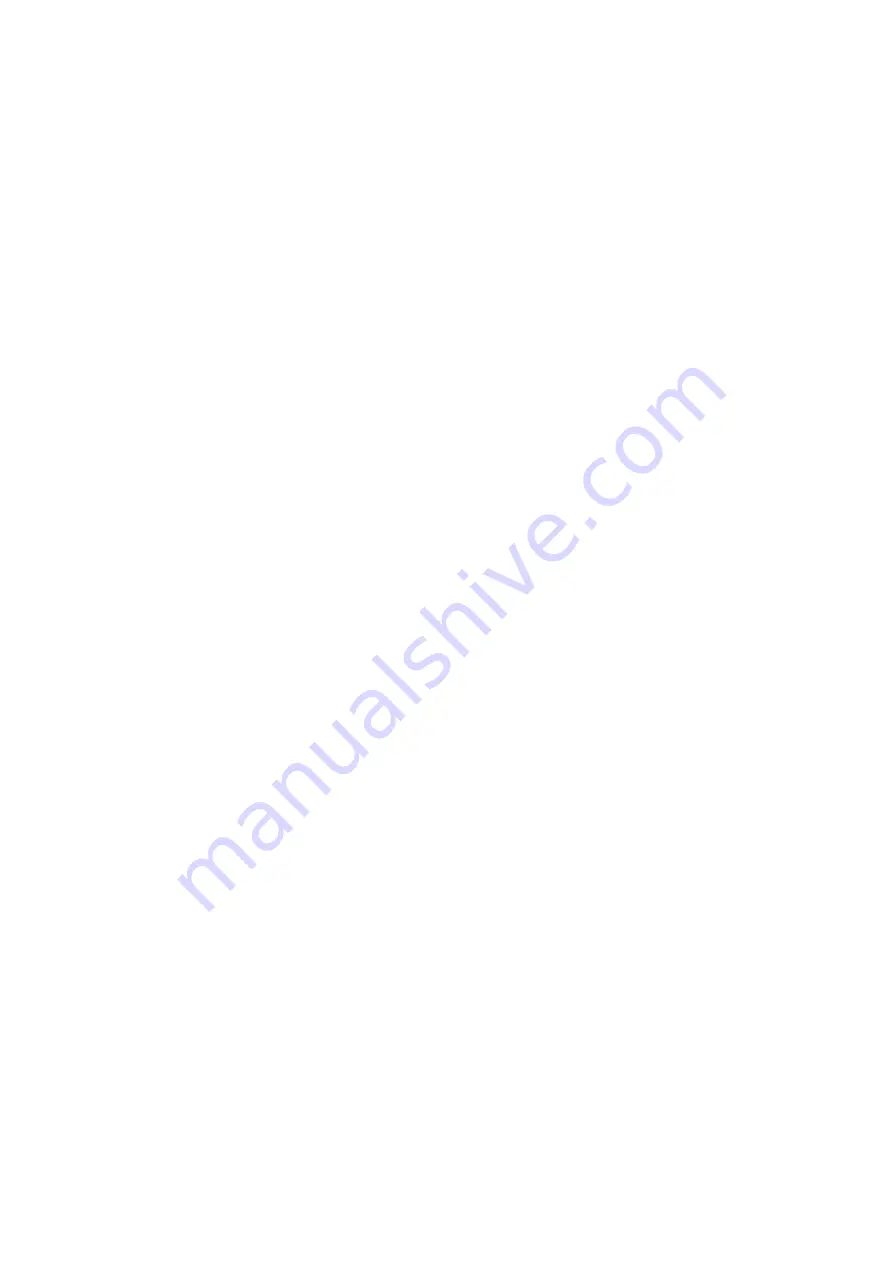
Page
4 -43
Figure 4- 26
Manual Feed Unit
4 -44
Figure 4- 27
Paper Feed Assembly
4 -45
Figure 4- 28
Paper Delivery Assembly
4 -47
Figure 4- 29
Electrical function
4 -48
Figure 4- 30
System Controller
4 -52
Figure 4- 31
Image Process Controller
4 -53
Figure 4- 32
Head Controller
4 -54
Figure 4- 33
Carriage Controller
4 -56
Figure 4- 34
Mech. Controller
4 -58
Figure 4- 35
Motor Controller
4 -60
Figure 4- 36
Power Supply Block Diagra m
4 -62
Figure 4- 37
Covers/Cassettes Sensor Layout
4 -64
Figure 4- 38
Schematic Diagram of Sensors for Ink Passage 2
4 -65
Figure 4- 39
Schematic Diagram of Sensors for Ink Passage 2
4 -66
Figure 4- 40
Suction Cap Sensor Flag
4 -66
Figure 4- 41
Preventive Cap/Wiper Up/Down Sensor Flag
4 -67
Figure 4- 42
Pump Sensor Flag
4 -67
Figure 4- 43
A-C/C-S Valve Sensor Flag
4 -68
Figure 4- 44
Pump Valve Sensor Flag
4 -68
Figure 4- 45
Y/PC/PM Air Valve Sensor Flag
4 -69
Figure 4- 46
C/M/K Air Valve Sensor Flag
4 -69
Figure 4- 47
A-H Valve Sensor Flag
4 -70
Figure 4- 48
Blade Sensor Flag (detects the position of the wiper blade)
4 -71
Figure 4- 49
Sub Tank Ink Sensor (Conceptual Representation)
4 -72
Figure 4- 50
Schematic Diagram of Sensors for Carriage Components
4 -73
Figure 4- 51
Print Position Sensor (Conceptual Representation)
4 -74
Figure 4- 52
Nozzle Check Sensor (Conceptual Representation)
4 -76
Figure 4- 53
Schematic Diagram of Sensors for Components Relating to Paper
Path 1
4 -77
Figure 4- 54
Schematic Diagram of Sensors for Components Relating to Paper
Path 2
4 -78
Figure 4- 55
Photo Reflection Sensor (Conceptual Representation)
4 -79
Figure 4- 56
Skew Sensors (Conceptual Representation)
4 -80
Figure 4- 57
Pressure Roller Sensor Flag
4 -80
Figure 4- 58
Manual Set (Skew) Sensors (Conceptual Representation)
4 -81
Figure 4- 59
Spur sensor flag
Part 5: MAINTENANCE
5 - 4
Figure 5- 1
Using the Cover Switch Tool
5 - 5
Figure 5- 2
Applying Grease onto the Feed Roller Gear
5 - 6
Figure 5- 3
"Right side up" Sign
5 - 8
Figure 5- 4
Example of Locations Where Disassembly is Prohibited or Careful
Adjustment is required (1)
5 - 9
Figure 5- 5
Example of Locations Where Disassembly is Prohibited or Careful
Adjustment is required (2)
5 -10
Figure 5- 6
Manual Carriage Operation
5 -11
Figure 5- 7
Units Needing to be Drained of Ink When the Printer is Disassembledt
5 -12
Figure 5- 8
Rear Lower Cover
5 -12
Figure 5- 9
Top Cover Unit and Cover Sensor
5 -13
Figure 5- 10
Right Cover/ Left Cover (Right cover removal: imaginal view)
5 -14
Figure 5- 11
Removing the Carriage Unit
5 -15
Figure 5- 12
Joint part of tubes on the carriage unit and sub-tank unit
5 -16
Figure 5- 13
Joints on the sub-tank unit and ink bottle uni
XIII
Содержание BJ-W9000
Страница 2: ...0201 GR 0 35 0 ...
Страница 3: ......
Страница 20: ...This page is intentionaly left blank ...
Страница 131: ...3 81 BJ W9000 Part 3 Operations This page intentionally left blank ...
Страница 143: ...4 5 BJ W9000 Part 4 Technical Reference This page intentionally left blank ...
Страница 199: ...4 61 Part 4 Technical Reference BJ W9000 This page intentionally left blank ...
Страница 251: ...5 31 BJ W9000 Part 5 Maintenance This page intentionally left blank ...
Страница 358: ...9 CIRCUIT DIAGRAM Refer to the Parts Catalog for the part layouts on each board Part 5 Maintenance BJ W9000 5 138 ...
Страница 359: ...5 139 BJ W9000 Part 5 Maintenance This page intentionally left blank ...
Страница 420: ...SERVICE MANUAL ...
Страница 440: ...Page 4 1 1 OPERATION OVERVIEW OVER Part 4 OPERATION VIEW ...
Страница 452: ...Page A 1 1 CIRCUIT DIAGRAM A 2 2 LOCATION OF ELECTRICAL COMPONENT ON THE PCB Part 6 APPENDIX ...
Страница 455: ...This document is printed on 100 recycled paper PRINTED IN JAPAN IMPRIME AU JAPON CANON INC ...