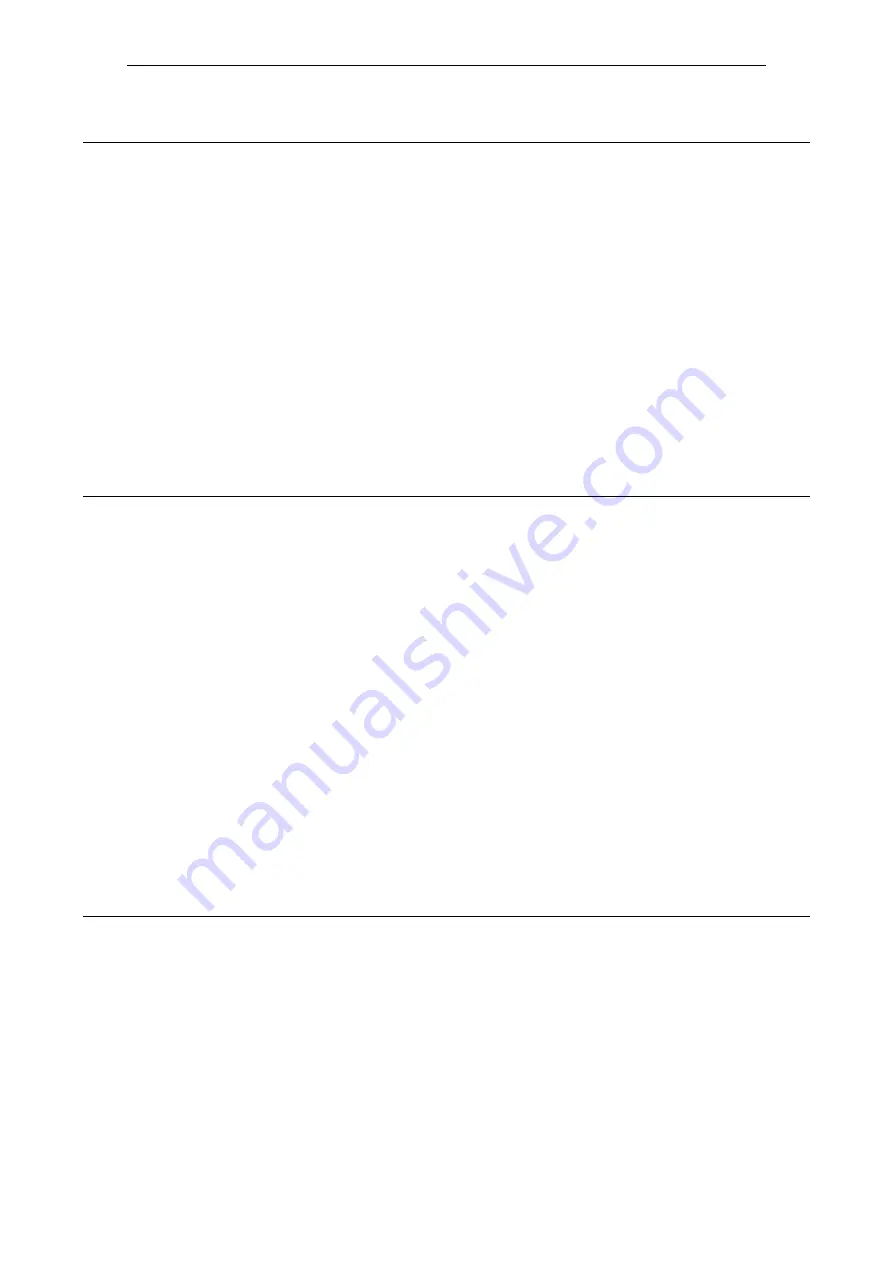
List of parameters
Parameter
1-557
© Siemens AG 2012 All Rights Reserved
SINAMICS S110 List Manual (LH7), 06/2012, 6SL3097-4AP10-0BP3
Description:
Setting for clock cycle synchronous communication between PROFIdrive controller and Control Unit.
The parameter is only relevant, if the safety-relevant motion monitoring functions integrated in the drive have been
enabled (p9601.2 =1 ).
If a PROFIdrive controller exchanges process data in clock cycle synchronism with the Control Unit, then p9510
must be set to 1. This also applies if the drive itself does not exchange process data in clock cycle synchronism.
Examples for clock cycle synchronous communication:
- clock-cycle synchronous control for the motion control (e.g. SIMOTION).
- clock-cycle synchronous PROFIsafe master (e.g. SIMATIC S7-400F).
Value:
0:
Communication not isochronous
1:
Communication isochronous
Dependency:
Refer to: C01711, A01796
Notice:
As of firmware V2.6, the parameter has no effect.
Description:
Sets the clock cycle time of the actual value sensing for safe motion monitoring.
Setting criteria if the motion monitoring functions are executed with an encoder.
- A slower clock cycle time reduces the maximum permissible velocity - however, it ensures a lower load of the Con-
trol Unit for safe actual value sensing.
- The maximum permissible velocity which, when exceeded, can mean that errors occur during safe actual value
sensing, is displayed in r9730.
- Setting criteria if the motion monitoring functions are executed without an encoder:
- The actual value sensing clock cycle must be set to the same value as the current controller clock cycle (p0115).
Dependency:
Refer to: F01652
Note:
The parameter is only active for drive-based motion monitoring functions (p9601.2 = 1).
The monitoring clock cycle from p9500 must be an integer multiple of this parameter.
In the case of motion monitoring functions with encoder, the clock cycle time for actual value sensing must be an
integer multiple of the current controller clock cycle and at least 4 times slower than the current controller clock
cycle. A factor of at least 8 is recommended. The value for the parameter must also be greater than or equal to 2
ms.
A change only becomes effective after a POWER ON.
Description:
Sets the encoder configuration for the redundant coarse position value.
p9510
SI Motion clock-cycle synchronous PROFIBUS master / SI Mtn sync master
SERVO_S110-CAN,
SERVO_S110-DP,
SERVO_S110-PN
Can be changed:
C2(95)
Calculated:
-
Access level:
4
Data type:
Integer16
Dynamic index:
-
Func. diagram:
-
P-Group:
Safety Integrated
Units group:
-
Unit selection:
-
Not for motor type:
-
Scaling:
-
Expert list:
1
Min Max
Factory
setting
0 1
0
p9511
SI Motion actual value sensing clock cycle (processor 1) / SI Mtn act clk P1
SERVO_S110-CAN,
SERVO_S110-DP,
SERVO_S110-PN
Can be changed:
C2(95)
Calculated:
-
Access level:
3
Data type:
FloatingPoint32
Dynamic index:
-
Func. diagram:
-
P-Group:
Safety Integrated
Units group:
-
Unit selection:
-
Not for motor type:
-
Scaling:
-
Expert list:
1
Min Max
Factory
setting
0.2500 [ms]
8.0000 [ms]
2.0000 [ms]
p9515
SI Motion encoder coarse pos. val. configuration (processor 1) / SI Mtn s config P1
SERVO_S110-CAN,
SERVO_S110-DP,
SERVO_S110-PN
Can be changed:
C2(95)
Calculated:
-
Access level:
3
Data type:
Unsigned32
Dynamic index:
-
Func. diagram:
-
P-Group:
Safety Integrated
Units group:
-
Unit selection:
-
Not for motor type:
-
Scaling:
-
Expert list:
1
Min Max
Factory
setting
-
-
0000 0000 0000 0000 0000
0000 0000 0000 bin