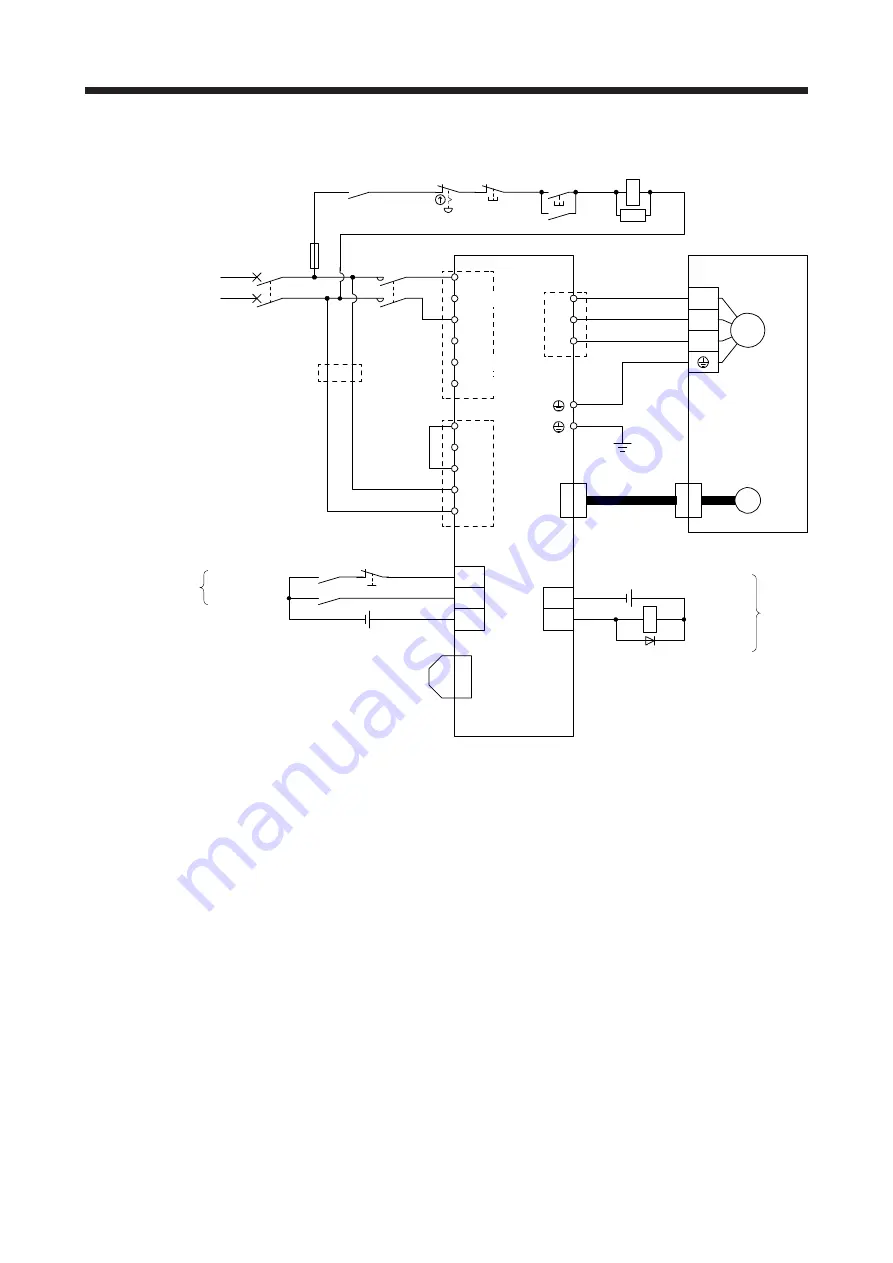
3. SIGNALS AND WIRING
3 - 11
3.1.3 100 V class
ALM
DOCOM
CN1
RA1
L1
L2
P+
L11
L21
N-
D
C
U
V
W
CNP1
CNP3
CNP2
U
V
W
M
CN2
MC
MC
SK
CN1
EM2
SON
DICOM
CN8
MCCB
(Note 6)
MC
(Note 4)
24 V DC (Note 11)
Malfunction
1-phase
100 V AC to
120 V AC
Servo amplifier
(Note 9)
(Note 2)
Servo motor
Motor
Encoder
(Note 3)
Encoder cable
(Note 5)
Malfunction
RA1
OFF
ON
EMG stop switch
Forced stop 2
Servo-on
(Note 4)
(Note 8)
Short-circuit connector
(Packed with the servo amplifier)
(Note 7)
Main circuit power supply
(Note 10)
(Note 10)
24 V DC (Note 11)
Unassigned
Unassigned
Unassigned
Note 1. The power factor improving DC reactor cannot be used.
2.
Always connect between P+ and D terminals (factory-wired). When using the regenerative option, refer to section 11.2.
3. For the encoder cable, use of the option cable is recommended. For selecting cables, refer to "Servo Motor Instruction Manual
(Vol. 3)".
4. This diagram shows sink I/O interface. For source I/O interface, refer to section 3.9.3.
5. For connecting servo motor power wires, refer to "Servo Motor Instruction Manual (Vol. 3)".
6. Use a magnetic contactor with an operation delay time (interval between current being applied to the coil until closure of
contacts) of 80 ms or less. Depending on the main circuit voltage and operation pattern, bus voltage decreases, and that may
cause the forced stop deceleration to shift to the dynamic brake deceleration. When dynamic brake deceleration is not
required, slow the time to turn off the magnetic contactor.
7. Configure a circuit to turn off EM2 when the main circuit power is turned off to prevent an unexpected restart of the servo
amplifier.
8. When not using the STO function, attach the short-circuit connector came with a servo amplifier.
9. When wires used for L11 and L21 are thinner than wires used for L1 and L2, use a molded-case circuit breaker. (Refer to
section 11.10.)
10. Connecting a servo motor of the wrong axis to U, V, W, or CN2 of the servo amplifier may cause a malfunction.
11. The illustration of the 24 V DC power supply is divided between input signal and output signal for convenience. However, they
can be configured by one.
Summary of Contents for MR-J4
Page 9: ...A 8 MEMO ...
Page 19: ...10 MEMO ...
Page 73: ...1 FUNCTIONS AND CONFIGURATION 1 54 MEMO ...
Page 155: ...3 SIGNALS AND WIRING 3 76 MEMO ...
Page 199: ...4 STARTUP 4 44 MEMO ...
Page 289: ...6 NORMAL GAIN ADJUSTMENT 6 24 MEMO ...
Page 335: ...8 TROUBLESHOOTING 8 8 MEMO ...
Page 357: ...9 OUTLINE DRAWINGS 9 22 MEMO ...
Page 517: ...12 ABSOLUTE POSITION DETECTION SYSTEM 12 30 MEMO ...
Page 617: ...16 USING A DIRECT DRIVE MOTOR 16 20 MEMO ...
Page 641: ...17 FULLY CLOSED LOOP SYSTEM 17 24 MEMO ...
Page 725: ...18 MR J4 03A6 SERVO AMPLIFIER 18 84 MEMO ...
Page 763: ...APPENDIX App 38 ...
Page 789: ...MEMO ...
Page 793: ......