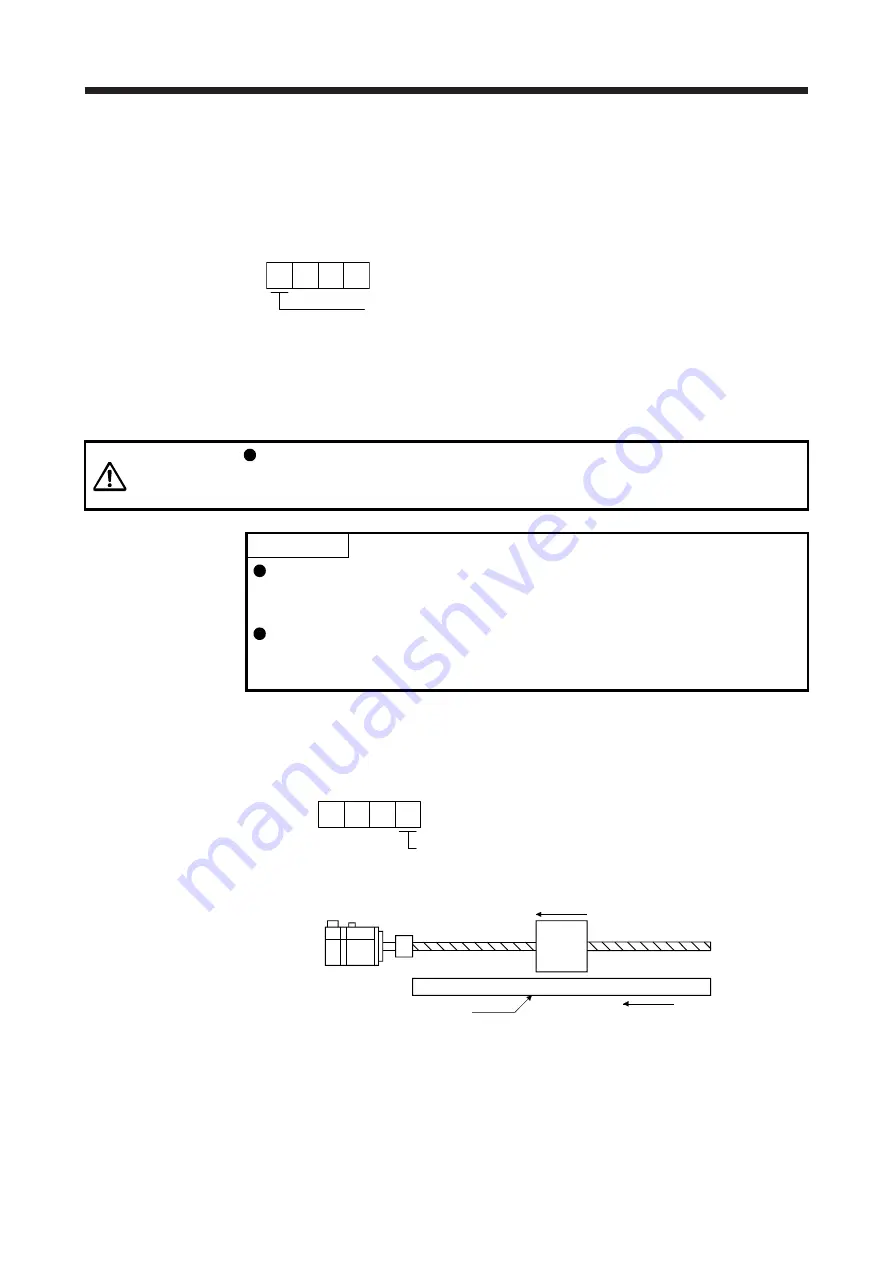
17. FULLY CLOSED LOOP SYSTEM
17 - 12
(3) Selection of load-side encoder communication method
The communication method changes depending on the load-side encoder type.
Refer to table 1.1 and "Linear Encoder Instruction Manual" for the communication method for each load-
side encoder.
Select the cable to be connected to CN2L connector in [Pr. PC44].
0 0 0
[Pr. PC44]
Load-side encoder cable communication method selection
0: Two-wire type
1: Four-wire type
When using a load-side encoder of A/B/Z-phase differential output method, set "0".
Incorrect setting will trigger [AL. 70] and [AL. 71]. Setting "1"
while using a servo amplifier other than MR-J4-_A_-RJ will trigger [AL. 37].
(4) Setting of load-side encoder polarity
CAUTION
Do not set an incorrect direction to "Encoder pulse count polarity selection" in [Pr.
PC45]. An abnormal operation and a machine collision may occur if an incorrect
direction is set, which cause a fault and parts damaged.
POINT
"Encoder pulse count polarity selection" in [Pr. PC45] is not related to [Pr. PA14
Rotation direction selection]. Make sure to set the parameter according to the
relationships between servo motor and linear encoder/rotary encoder.
Do not set an incorrect direction to "Encoder pulse count polarity selection" in
[Pr. PC45]. Doing so may cause [AL. 42 Fully closed loop control error] during
the positioning operation.
(a) Parameter setting method
Set the load-side encoder polarity to be connected to CN2L connector in order to match the CCW
direction of servo motor and the increasing direction of load-side encoder feedback.
0 0 0
[Pr. PC45]
Load-side encoder pulse count polarity selection
0: Load-side encoder pulse increasing direction in the servo motor CCW
1: Load-side encoder pulse decreasing direction in the servo motor CCW
Servo motor
Linear encoder
Servo motor CCW direction
Address increasing direction of linear encoder
(b) How to confirm the load-side encoder feedback direction
For the way of confirming the load-side encoder feedback direction, refer to (6) in this section.
Summary of Contents for MR-J4
Page 9: ...A 8 MEMO ...
Page 19: ...10 MEMO ...
Page 73: ...1 FUNCTIONS AND CONFIGURATION 1 54 MEMO ...
Page 155: ...3 SIGNALS AND WIRING 3 76 MEMO ...
Page 199: ...4 STARTUP 4 44 MEMO ...
Page 289: ...6 NORMAL GAIN ADJUSTMENT 6 24 MEMO ...
Page 335: ...8 TROUBLESHOOTING 8 8 MEMO ...
Page 357: ...9 OUTLINE DRAWINGS 9 22 MEMO ...
Page 517: ...12 ABSOLUTE POSITION DETECTION SYSTEM 12 30 MEMO ...
Page 617: ...16 USING A DIRECT DRIVE MOTOR 16 20 MEMO ...
Page 641: ...17 FULLY CLOSED LOOP SYSTEM 17 24 MEMO ...
Page 725: ...18 MR J4 03A6 SERVO AMPLIFIER 18 84 MEMO ...
Page 763: ...APPENDIX App 38 ...
Page 789: ...MEMO ...
Page 793: ......